
初心者向けリスクアセスメント入門:停止中の機械で学んだ安全対策の秘訣とは?【ISO 14119:2024】【ISO 13855:2024】アップデート
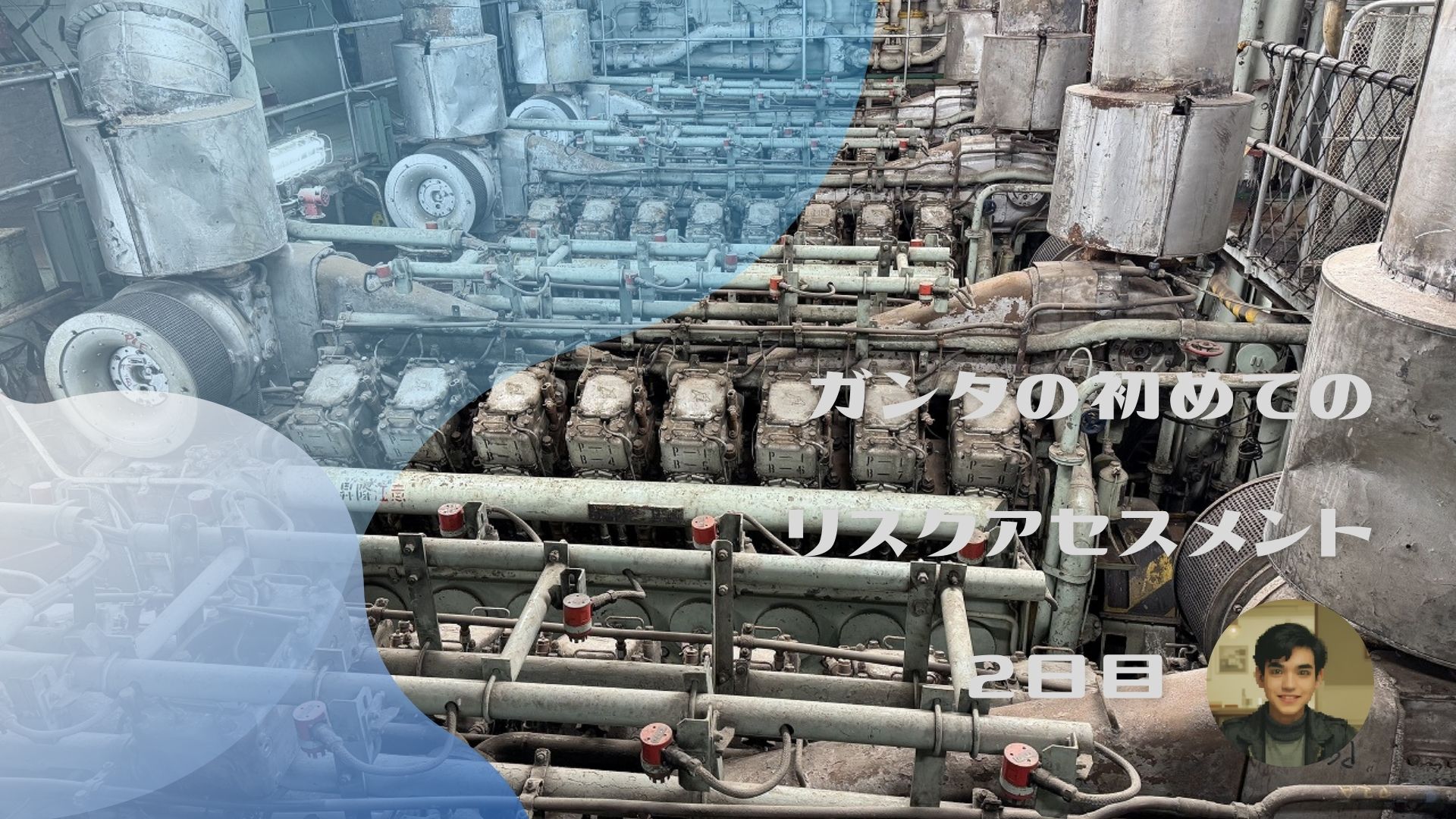
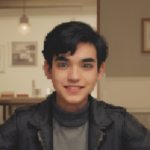
こんにちは! ジュンイチロウさんの弟子、ガンタです!
前回に引き続き、リスクアセスメント初心者の私が「やっててよかった!」と心から思ったポイントを、皆さんにシェアしますね!
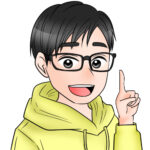
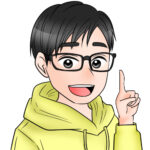
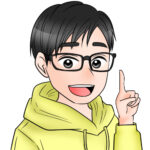
前回の記事を読んでくださった方、ありがとうございます!
今回は、現場での学びの2日目をお届けします。
目次
危険源の見定めかたの極意
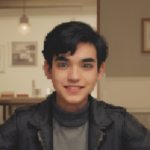
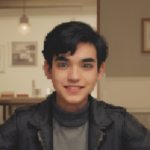
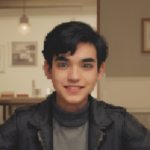
停止中の機械だからこそ、じっくり観察!
2日目は、機械が停止している状態でのリスクアセスメント。大きな設備を2つ、じっくり見ていく計画でした。前日は機械が動いている様子を確認しましたが、時間の関係で隅々までは見られませんでした。2日目は停止している機械を、時間をかけて一つ一つ丁寧に確認していきます。具体的には、こんなことをしました。
- 危険源の特定(どんな危険なことが起こりうるか、写真を撮りながら考えました)
- センサーの機能確認(ライトカーテンと危険源の距離を測りました)
- PLr(Performance Level required:要求パフォーマンスレベル)の算出
- 対策案と、対策に使う製品の選定リスト
タッチパネルは、現場の必需品!
ジュンイチロウさんが使っていたMicrosoft 社が販売している Surface のパソコン、これがもう、本当に便利でした!リスクアセスメントでは、停止時間中に上記のような作業を行います。どんな危険なことが起こりうるかを想定して、その原因となる場所(危険源)の写真を撮ります。
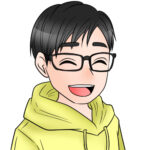
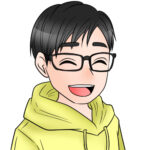
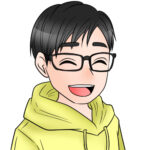
好きなタブレット端末で良いと思います!
リンク
リスクアセスメントのレポートは、基本的には文章で書きます。でも、文章だけだと、現場のどこについて言っているのか、後から見ると分かりにくいことが多いんです。ジュンイチロウさんのレポートは、分かりやすいように、該当箇所の写真と文章がリンクされていました。
いつ、どこで、誰が見ても分かるレポートにすることが、リスクアセスメントレポートのあるべき姿。なぜなら、このレポートをもとに安全対策をするということは、社内だけでなく、施工業者さんや第三者機関の方々にも見てもらう機会があるかもしれないからです。初めてその機械を見た人でも理解できるのが、理想的なリスクアセスメントレポートと言えるでしょう。
それに、レポートを後から書くときに、文章だけだと自分でも「あれ?ここ、どこだっけ?」となってしまいかねません。
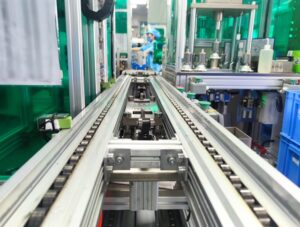
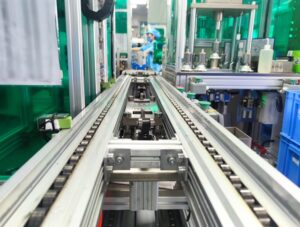
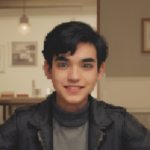
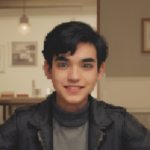
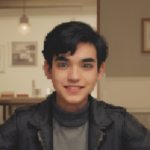
あれ?ここ、どこだっけ?
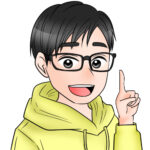
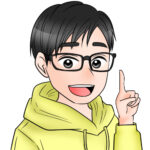
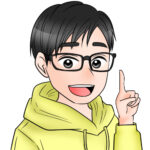
機械がたくさんあるから、メモは後で簡単に見返すことが大事なんすよ
特に今回は4日間という長丁場。似たような機械やラインも多いので、逆に写真を撮らないと、後で自分が困ってしまいます。リスクアセスメントでは、危険源の写真を撮るものだと覚えておきましょう。
あわせて読みたい

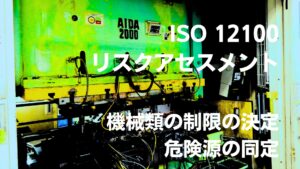
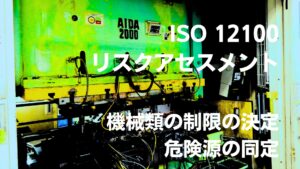
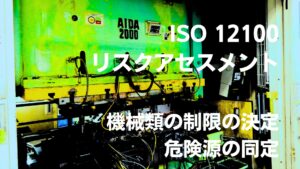
ISO12100リスクアセスメントによる機械類の制限の決定や危険源の同定の具体的なやり方とコツ
あらすじ こんにちは! ISO12100 リスクアセスメント機械類の制限の決定と危険源の同定について話してみたいと思います。 ISO12100 は、機械類の安全性に関する国際規格…
セーフティコンセプトレポートのコツ
同時に、現状の安全対策もメモします。
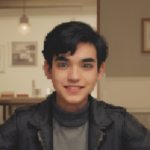
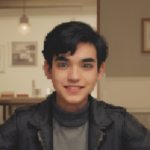
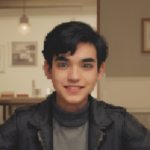
安全対策レポートをセーフティコンセプトレポートと呼びます!
使っている安全機器のメーカー名や型式を記録しておかないと、せっかく写真を撮って、オペレーターさんに状況を聞いて、現状のPLr を算出しても、現状の安全対策がそれを満たしているかどうかが分からなくなってしまいます。今回も、安全対策されているように見えて、実は安全機器ではない製品が使われていることがありました。安全機器かどうかを判断するには、製品の型式を把握していることが重要です。必ずメモするか、写真に記録しておきましょう。
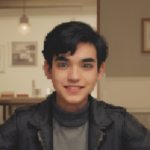
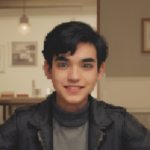
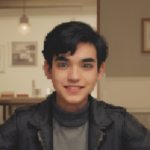
セーフティコンセプトレポートに、下記のようなSRP/CS のコンセプトを表現します!
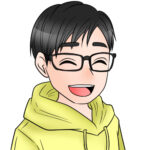
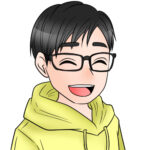
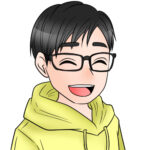
セーフティコンセプトレポートは、読む人にとってわかりやすくすることが重要です。また、設計者にとって使いやすい部品を提案することも重要な要素です。
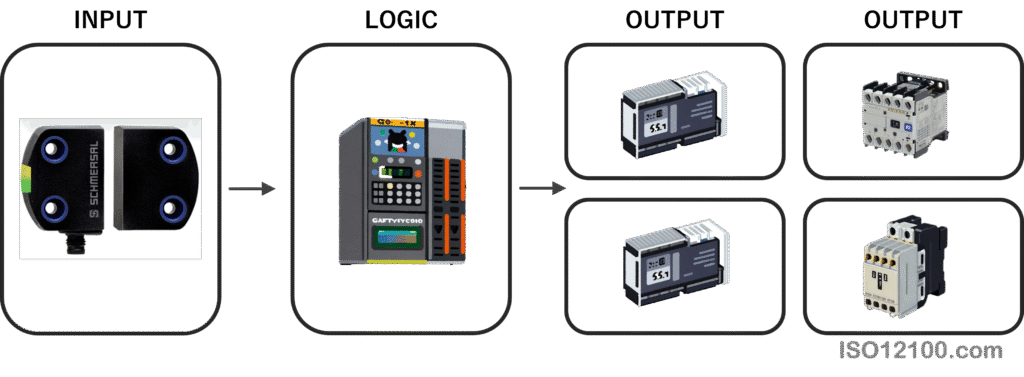
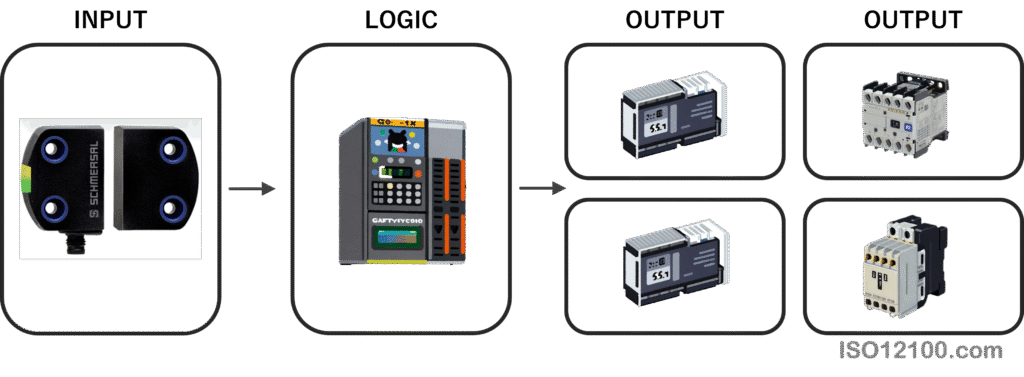
安全距離をメモするメリット
記録として重要な項目には、安全距離もあります。これは、停止状態でのリスクアセスメントにおいて、非常に重要な数値データになるので、必ずメモしておく必要があります。
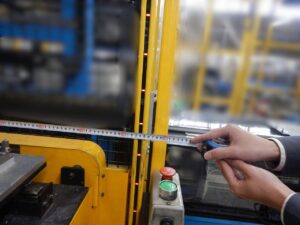
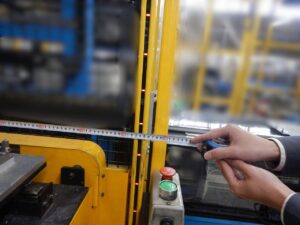
そして、可能であれば、その場でPLr まで想定してメモしておくと、後のレポート作成がとてもスムーズになります。これは経験則によるところも大きいのですが、ISO 13849-1 の付属書A に、PLr の決定方法が記載されています。ジュンイチロウさんは、この方法に基づいて、その場でPLr をメモしていました。PLr の決定にも、オペレーターさんへの質問が非常に重要でした!
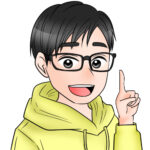
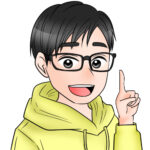
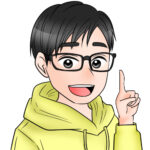
メモはこんな感じです!
SD=700 mm
PLr= S2/F1/P2, d
PLr をメモするメリット
最後によくあるのが、メーカーさんによっては安全対策のための安全機器が指定されていたり、エンドユーザーさんに支給されるケースもあることです。
この場合、PLr を満たす安全回路を組むといっても、指定メーカーの製品をいちいち調べなければなりません。特にセーフティコンセプトで必要なので、当日の現場ではここまでメモできなくても良いのですが、可能であれば、その場でPLr を達成可能な安全機器の型式もメモしておけると、レポートが格段に書きやすくなります。
だからこそ、Surface やiPad のような、インターネットに接続できて、写真も撮れるタッチパネル式のデバイスが、リスクアセスメントの効率化に最適だと言えます。ジュンイチロウさんは、以下の内容を危険な事象ごとに、ものすごく早いペースで進めていました。それができたのも、タッチパネルがあったからだと思います。
- 危険源の写真撮影
- 現状の安全機器の型式
- 現状の安全距離
- PLr
- 対策製品の型式リスト
面倒なことはガジェットに頼ろう!
以前、リスクアセスメントをやっている方にお話を聞いたところ、現場ではデジカメで危険源の写真を撮り、現状の対策品はメモ帳に型式をメモして、オフィスのパソコンでその製品のスペックを調べて、初めて適切かどうかが分かったとおっしゃっていました。
現場でメモできていなかったために「なんだったっけ?」となったり、撮り忘れが出てきてしまったこともあったそうです。
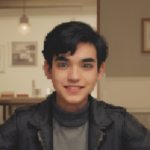
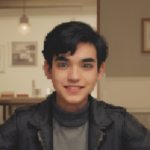
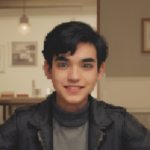
この写真なんやったっけ?
タッチパネルであれば、このような煩わしさや、工程の面倒さを排除できるだけでなく、何よりもリスクアセスメントのクオリティをすぐに上げられ、作業工数、作業時間も減らせるという点で、一番最初に取り入れたいと思うほど、実用的な発見でした。
リスクアセスメントはISO 12100 に手順が記載されていますが、具体的な方法は示されていません。どんどん最新の機器を取り入れて、効率よくリスクアセスメントをしていくことが大切だと学びました。
ただし、寒冷地や長時間作業ではバッテリーの減りが早いので、予備バッテリーや充電器を持参することをおすすめします!
新しい ISO 13855:2024 EN ISO 13855:2025 ―安全距離を正しく測定しよう―
今回の現場では、ライトカーテンが多く設置されていました。センサー機能の確認として、安全距離について補足します。ライトカーテンを取り付ける際には、ISO 13855:2024(人体部位の接近速度に基づく安全防護物の位置決め)という国際規格に基づいて、危険源との距離を正確に測る必要があります。
ISO




ISO 13855:2024
Safety of machinery — Positioning of safeguards with respect to the approach of the human body
iTeh Standards

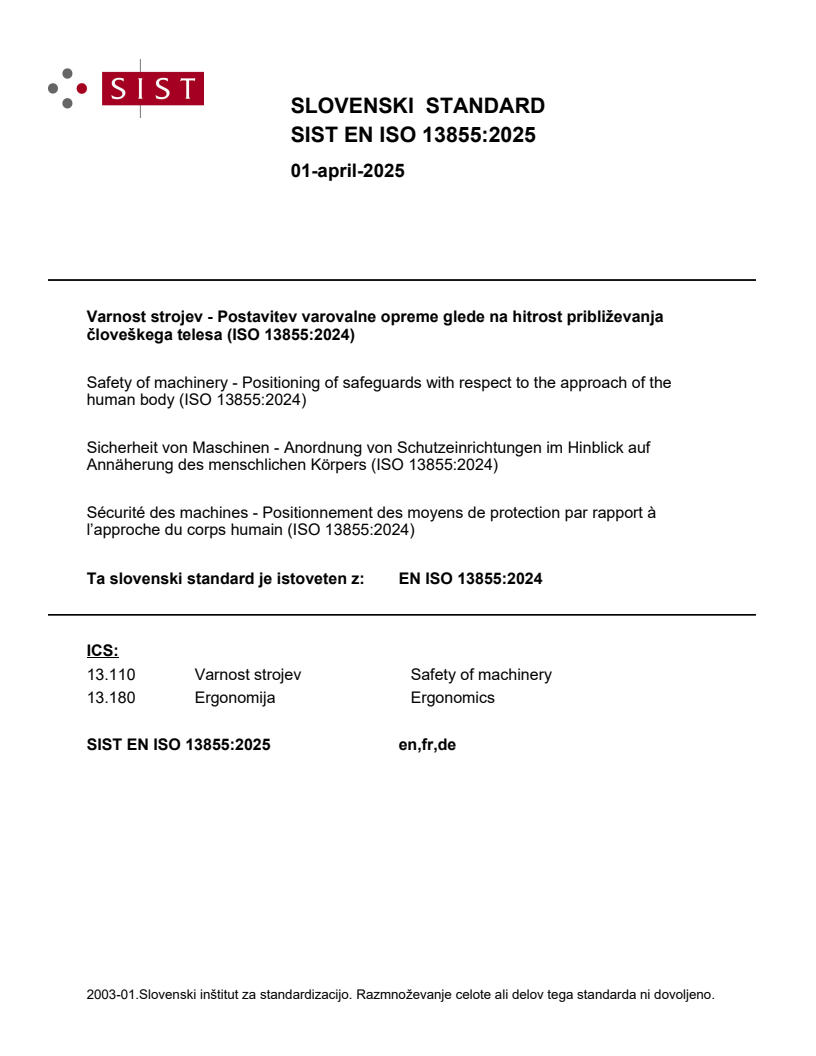
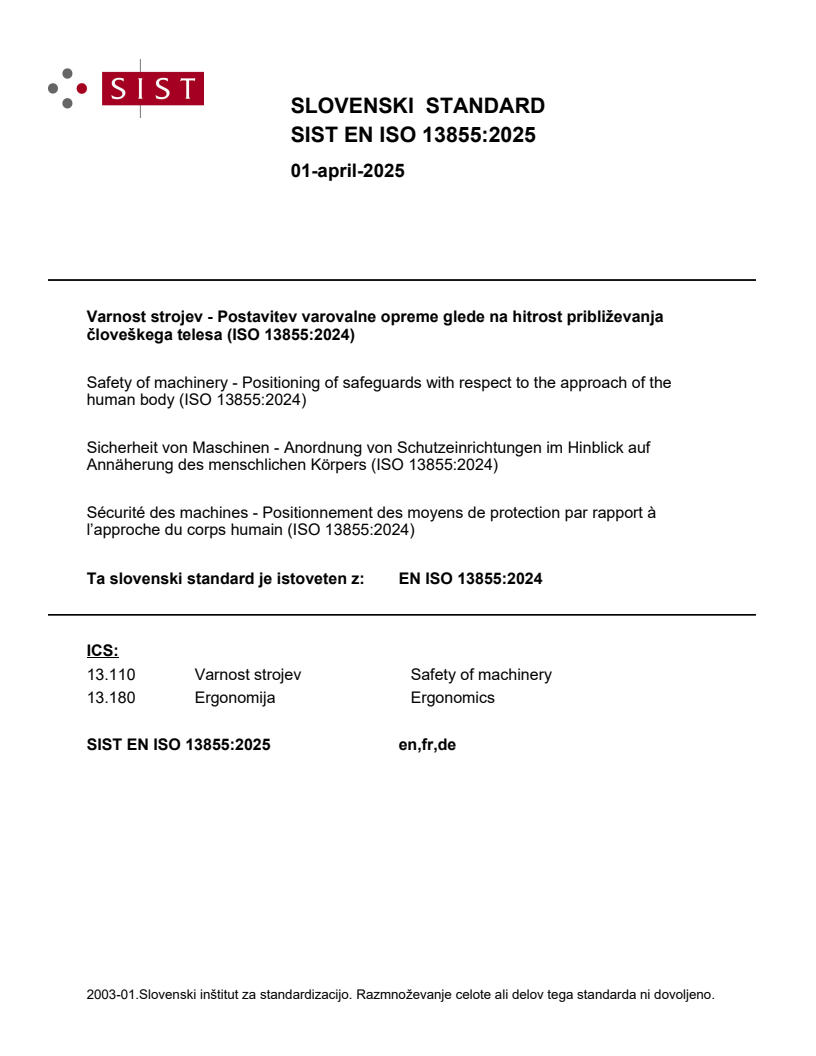
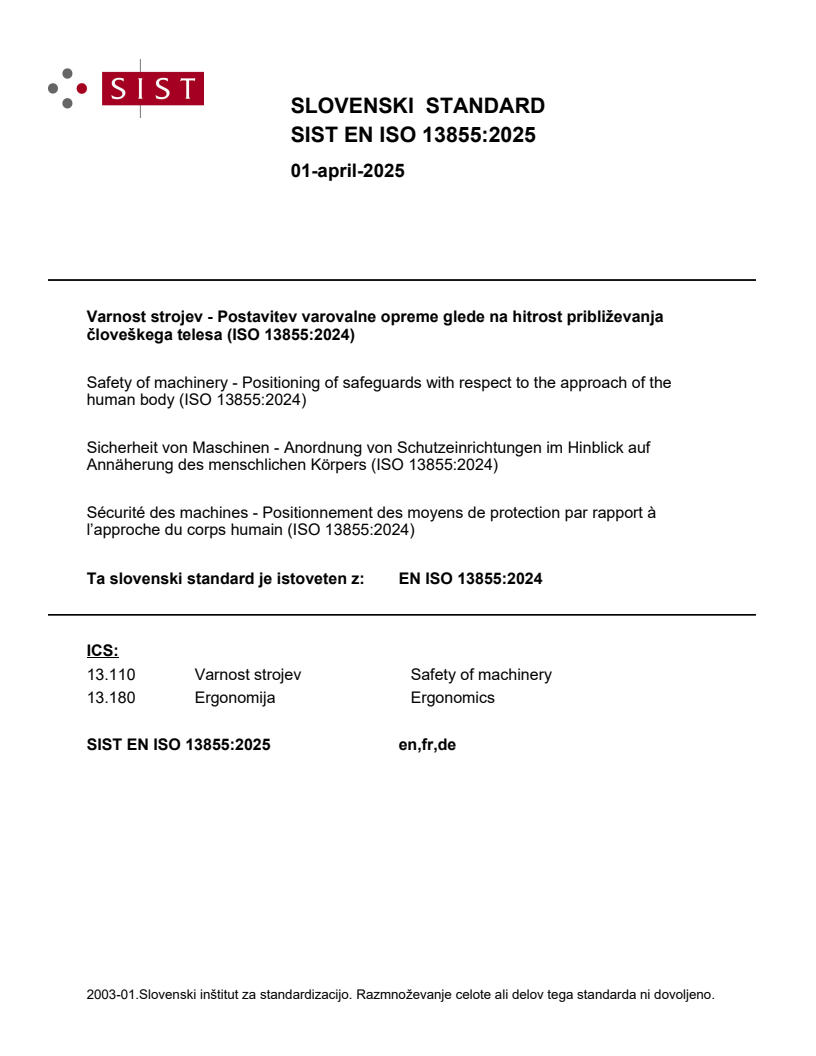
SIST EN ISO 13855:2025 – Safety of machinery – Positioning of safeguards with respect to the approac…
SIST EN ISO 13855:2025 – This document specifies requirements for the positioning and dimensioning of safeguards with respect to the approach of the human body …
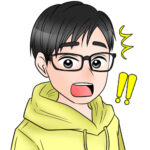
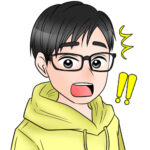
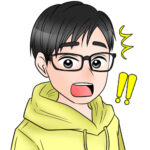
新しいバージョン ISO 13855:2024 、またはEN ISO 13855:2025 にアップデートしてくださいね!
多くの現場では、この安全距離がきちんと確保されておらず、せっかくライトカーテンをつけているのに、全くPLr を満たせていない、危険な事象を起こしてしまいそうな設備が多くあります。日本の工場は、特に土地が限られているせいか、スペースを有効活用しようとする傾向があり、適切な安全距離を分かってはいても確保できない、という状況に陥りがちです。だからこそ、安全距離を短くしても良い方策をしっかりと学んでおくと、社内でも安全規格を理解していて、生産性を上げられる重要な人材になれるでしょう!
そんな安全距離ですが、リスクアセスメントの現場では、本当に地道に一か所一か所測ります。これが非常に手間のかかる工程です。特にライトカーテンを使用していると、危険源までの測り方が垂直にすることが困難な場合が多いのです。
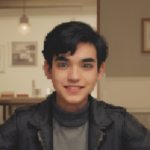
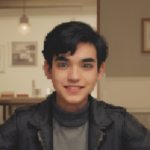
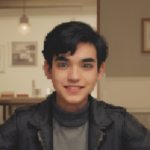
メジャーは2つ用意すること!
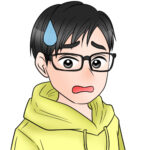
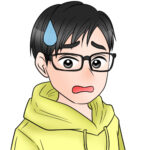
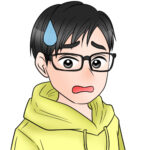
歳をとると、目盛りが読めないし、腰は痛いし
メジャーの二刀流!?
安全距離はメジャー(コンベックスって言ったりします?)1本でも測れますが、どうしても斜めになったり、正確な距離が測れない可能性があります。2本のメジャーを使って垂直に交差させれば、より正確な測定が可能です。工場内はスペースが限られているので、安全距離は適切にとらないといけないと思います。
このずれによって、極力抑えられるはずの距離が多めに取られてしまっていたり、オーバースペックのライトカーテンだったりなど、もったいない場面も多かったです。ちなみに、リスクアセスメントは基本的にチームで行うので、全員がメジャーを持参しておくと効率がアップしますよ!
安全距離の計算式
ここで、今ついているライトカーテンが適切かどうかを一目で判断できるコツがあります。ライトカーテンの安全距離の計算式は、
$$ S = K × T + C $$
$$ C = 8(d−14) $$
となります。このd は検出能力といい、センサーのピッチ間隔のことです。つまり、ライトカーテンの検出能力(ピッチ間隔)が14mm 以下であれば、侵入速度K と停止時間T との掛け算のみになるので、だいたい S=500mm 前後になることが多いです。
したがって、ライトカーテンの検出能力が14mm 以下であり、かつ危険源までの距離が500mm 以上あったときは、おそらく適切だろうと判断ができるのです。
もちろん、リスクアセスメントレポートやセーフティコンセプトレポートを作成中にきちんと計算するのですが、たいていが安全距離500mm 以下になることがほとんどでした。
ここでもやはり、図面情報や使用している製品を把握しておかなければ停止時間T を求めることもできないので、事前準備が非常に重要になります。リスクアセスメントにおいては、実施する誰もが測定と記録を行うつもりで事前準備をすることを推奨します!
ISO 14119:2024, EN ISO 14119:2025 ―ガードと共同するインターロック機器―
ISO 14119 では、エネルギー源の種類に関わらず適用可能なインターロック機器の設計および選定の原則を示し、インターロック機器が合理的に予見される範囲で無効化される可能性を最小限に抑えるための対策について指針を提供しています。
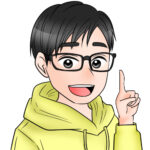
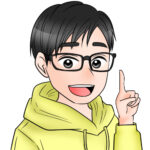
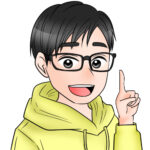
ISO 14119:2024, EN ISO 14119:2025 にアップデートしてくださいね!
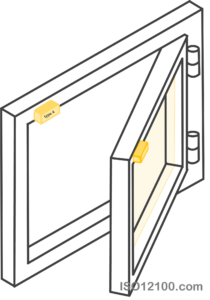
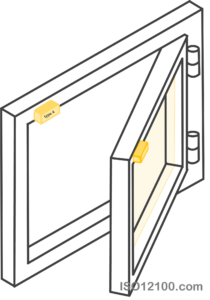
ISO




ISO 14119:2024
Safety of machinery — Interlocking devices associated with guards — Principles for design and selection
iTeh Standards

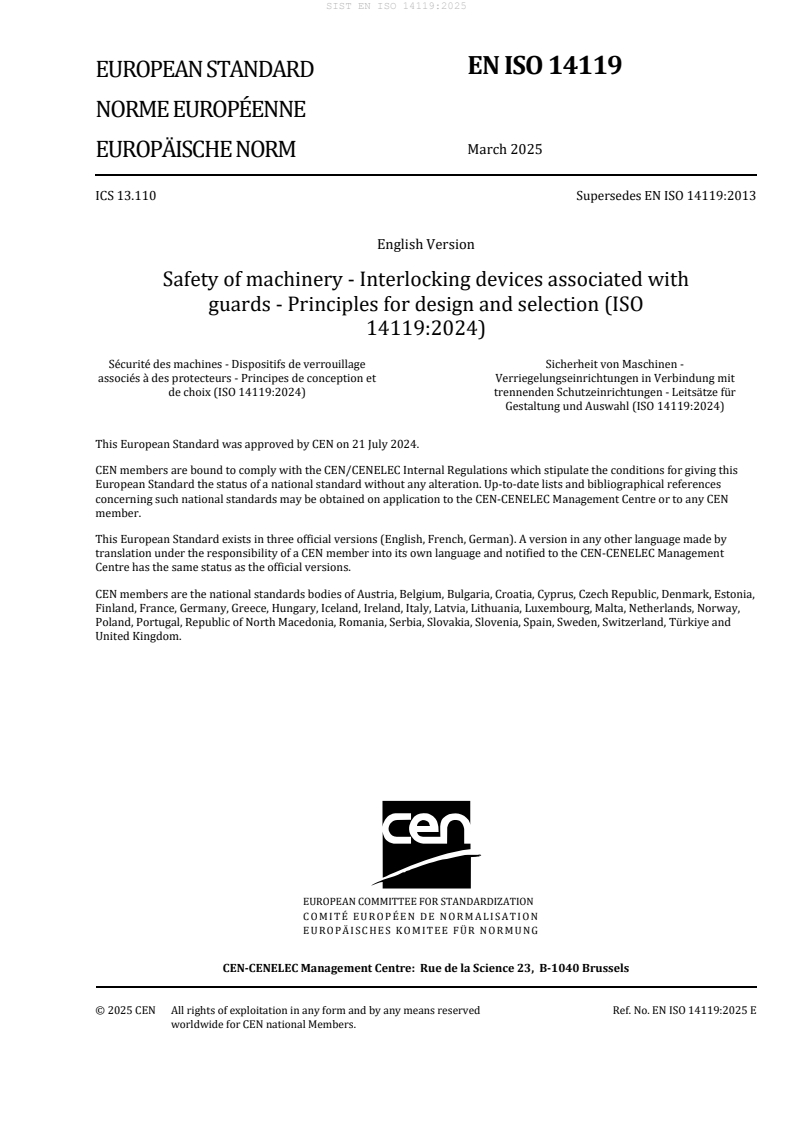
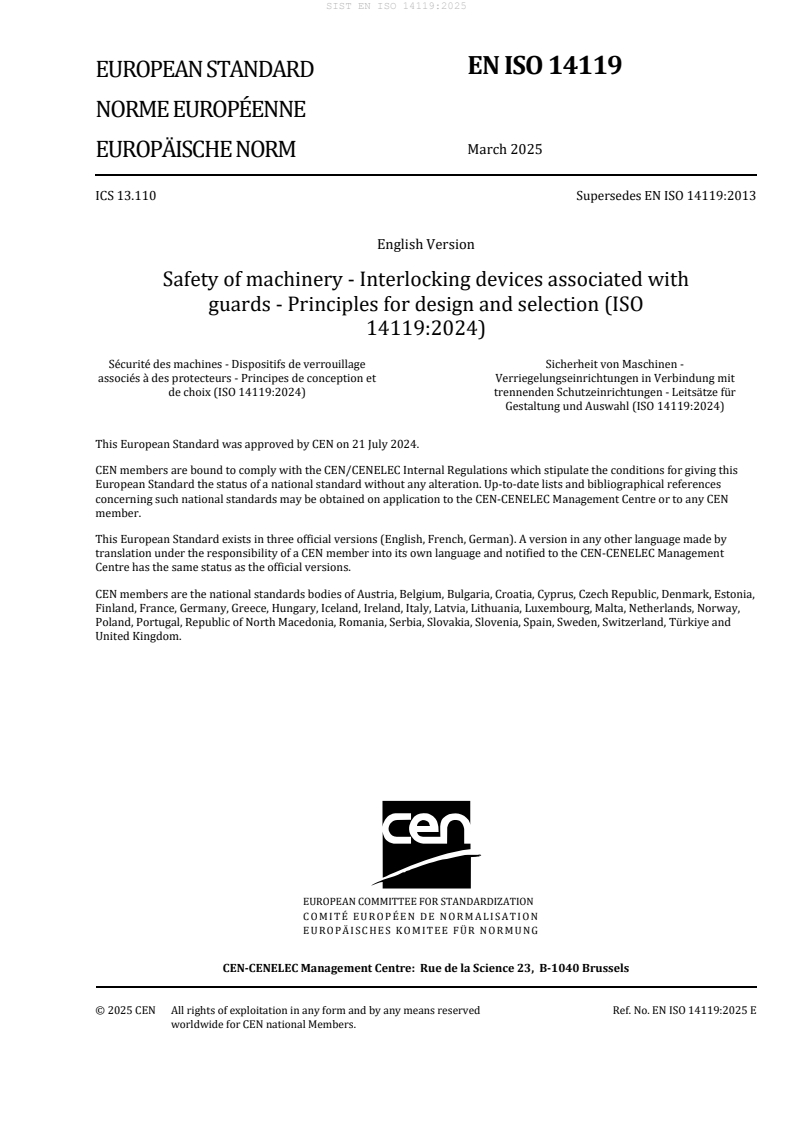
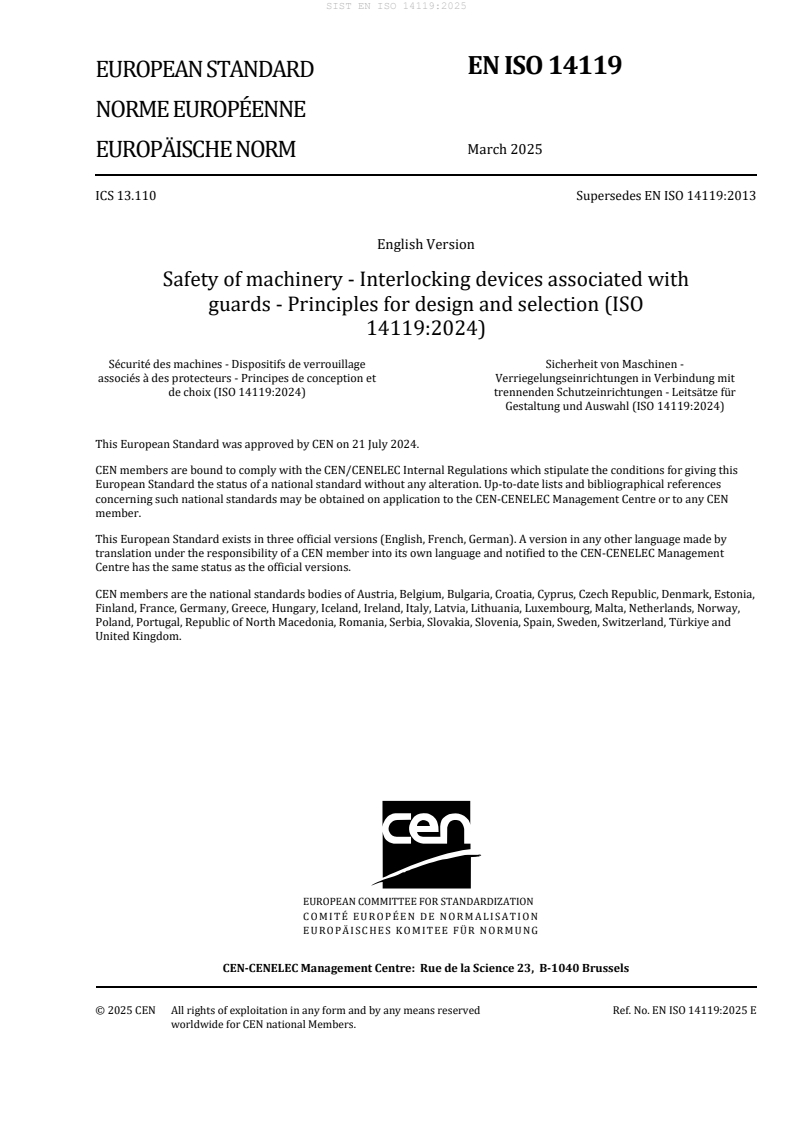
EN ISO 14119:2025 – Safety of machinery – Interlocking devices associated with guards – Principles f…
EN ISO 14119:2025 – This document specifies principles for the design and selection (independent of the nature of the energy source) of interlocking devices ass…
新しい ISO 14119:2024, EN ISO 14119:2025 の主な対象範囲
ISO 14119 が取り扱う内容は以下の通りです:
- ガードの一部
- インターロック機器を作動させる部品の設計および適用方法
- トラップキーインターロック機器およびシステム
- 機械用途向けに使用されるトラップキーインターロック機器およびそのシステムリスト
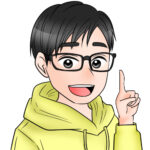
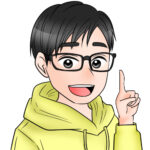
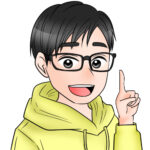
2025年は重要な規格が更新されています!
新しい ISO 14119:2024, EN ISO 14119:2025 の主な変更点
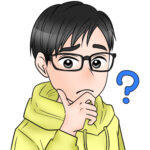
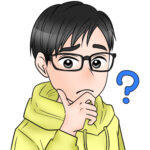
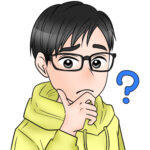
旧 ISO 14119:2013 に比べて以下の内容が主に変わっています!
- トラップドキーインターロック機器およびシステムの定義
- タイプ5インターロック機器およびトラップドキーインターロックシステムが正式に定義されました。
- 付属書K トラップドキーインターロックシステム
- 付属書K が新設され、タイプ5 インターロック機器(トラップドキーインターロック機器)に関する具体的な要件が追加されました。
- 表5「インターロック機器の種類によって、予見される無効化の動機が引き続き存在する場合の追加措置」の改善と名称変更
- 表5が改良され、より分かりやすい内容となり、新しい名称が付けられました。
- 新しい試験手順の追加
- 新設された付録Iにおいて、試験手順が具体的に記載されています。
- フォールトマスキングの統合
- フォールトマスキングの内容が新しい付属書J に統合されました。
えっ、それって安全機器じゃないの!?プラグスイッチの落とし穴
本日2つ目の機械では、ロボットを使用する工程があり、その周囲は柵で囲われていました。ただし、扉にはプラグスイッチが使われていました。このプラグスイッチ、日本では安価でよく使われていますが、実は安全機器ではないんです!
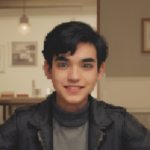
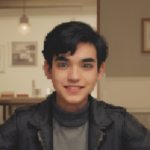
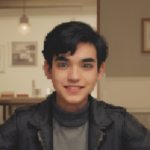
プラグスイッチは安全機器ではないんです!
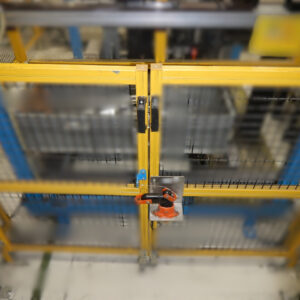
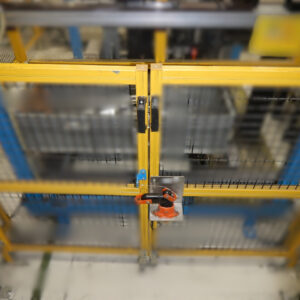
皆さん、何気なくプラグスイッチを使用していませんか?「あのメーカーさんがつけていたから付けました」という理由では、残念ながら安全にしたつもりでも、実際には安全が確保できていないことが非常に多いのが現実です。
この後詳しくお話しますが、まずは安全機器の定義からおさらいしておきましょう。
安全機器と危険側故障・安全側故障
簡単に説明すると、安全機器とは「故障した時に安全側故障になるよう設計されたもの」を指します。一方、プラグスイッチは構造上、安全側故障にはならず、危険側故障になる可能性があります。「そもそも安全側故障と危険側故障って何?」と思ったそこのあなた、このまま読み進めていただければと思います。
安全機器も安全側故障と危険側故障も、もうすでに知ってます!という方は、「リスクアセスメントで抑えるべき4つのポイント」の段落まで飛ばしてもらって結構です!
赤信号・青信号
まず、安全側故障と危険側故障を説明する上でよく用いられるのが、信号機の例です。説明する前に、問題です。
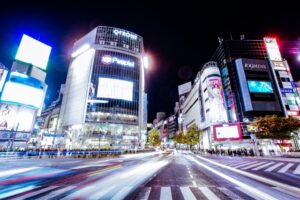
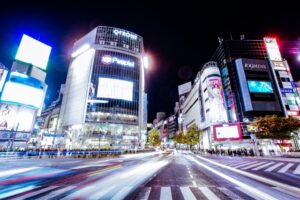
「信号機が1灯しかない場合、赤信号と青信号、どちらが事故が起こらない(安全)でしょうか?」
赤を選んだ方は、惜しい!
青を選んだ方は、素晴らしい!…が回答です。
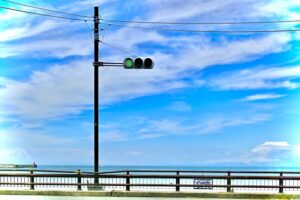
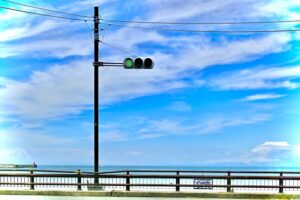
直感だと、「止まっている状態=安全=止まっている信号の色=赤」という思考になりやすいですよね?
私も初めて話を聞いた時は、自信をもって「赤!」と回答したことを覚えています。実は、安全の考え方は、万が一故障した状態を考慮するのです。
赤信号が故障したとき
もし赤信号が故障した時、消灯=動いていい、という状態になります。交差点で片方は正常に消灯(=動いていい状態)でも、片方が故障していた場合、本来こちらは点灯(=止まれの状態)していなければならないところが、こちらも消灯(=動いていい状態)となってしまいます。そうすると、ドライバーは交差点の両側とも動いてしまい、事故が起こってしまいます。
青信号が故障したとき
では、青信号だとどうなるのかというと、消灯=止まれ、になります。つまり、万が一青信号が故障した場合には、止まれになるのです。したがって、交差点で片方が消灯(=止まれの状態)でも、片方が故障していた場合、本来こちらは点灯(=動いていい状態)していなければならないところが消灯(=止まれの状態)となるので、ドライバーは交差点の両側とも止まっている状態をキープし続けます。交通としては問題がありますが、システムによる事故は起こらないですよね。
危険側故障・安全側故障
まとめると、故障には2種類あり、故障した時に危険になってしまう故障のことを危険側故障と言い、故障した時に危険にならないようにする仕組みがある故障のことを安全側故障と言います。信号の例を要約すると、下記のようになります。
- 赤色1灯:停電時に消灯し、車が動き出す(危険側故障)
- 青色1灯:停電時に消灯し、車が停止したまま(安全側故障)
通常、故障したら危険側故障と安全側故障の発生する確率としては、なんとなく直感で50%:50%ですよね?
安全機器とは、機構を変更したり、組み合わせたりすることで、この確率をできる限り安全側故障の比率を大きくした製品のことを示します。つまり、安全機器は「万が一の故障時にも安全を保てる」設計になっている必要があるのです。
残念ながら、プラグスイッチはその条件を満たしていないため、安全機器として認められていません。プラグスイッチはオレンジ色の形状のものが一般的ですが、アクチュエータを抜いて扉を開けられるような機構になっています。このアクチュエータは導体の金属棒が2本ついていて、アクチュエータ内部でコの字のように接続されているだけの単純な機構なことがほとんどです。
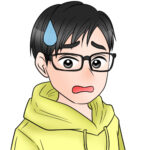
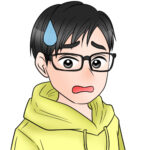
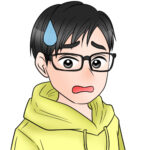
プラグスイッチは ISO 13849-2 で言う、「well-tried」「十分に吟味」した部品ではありません www
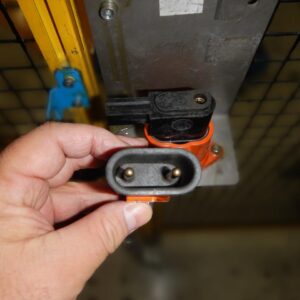
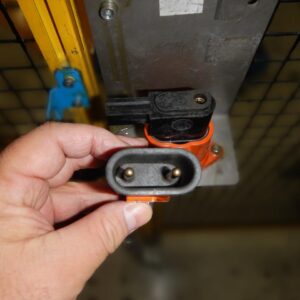
このような機構によって2線ですので、どこでもジャンパー可能ですし、故障などで万が一溶着してしまったりした際には、危険側故障になりかねません。
今回、ジュンイチロウさんもプラグスイッチの危険性を注意深く説明されていました。やっぱり、お客様の安全の責任者の方には、最低限知っておいてほしいことなのだと感じました。皆さんの設備には、プラグスイッチはつけられていますでしょうか。
そのインターロック機器は安全機器?
プラグスイッチの他にも、非接触のセンサーやライトカーテン、マットスイッチなども、安全機器かどうかを知らずにつけてしまっている例が非常に多いです。
見分けるポイントとしては、仕様書に「PFH:Probability of Dangerous Failure per Hour」(単位時間当たりの危険側故障確率)や「B10d」(10%の部品が危険側故障を起こすまでの運転回数)、「MTTFd:Mean Time to Dangerous Failure」(平均危険側故障時間)が記載されているかどうかを確認するとよいでしょう。
または、メーカーのHP には、だいたいセーフティコンポーネントというくくりで分類されていることがほとんどです。そこでも確認しておくと、より安心ですよね!
どうしても分からなければ、メーカーに直接問い合わせてみてください。「これ、○○という型式なのですが、本当に安全機器ですか?」と。答えられないようなメーカーの製品は、だいたいが汎用機器ですので、ご注意いただければと思います。
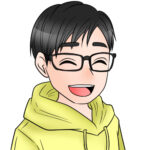
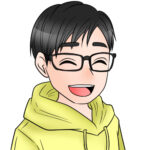
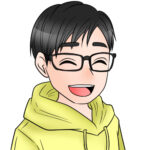
迷ったときには、SISTEMA ライブラリを用意しているメーカーをおすすめします!
それでもどうしても、ということであれば、安全機器の専門メーカーがあります。現在お取引のある商社様経由で聞いてみるのも、もしかしたら回答があるかもしれません。その際には、「この代替品はありますか?」と一緒に聞いてみれば、安全機器も推奨してもらえるかと思います。汎用機器は、リスクアセスメントする上で見つけた瞬間に指摘されてしまうところなので、早めの対策を推奨します!
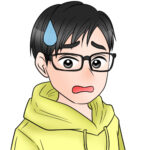
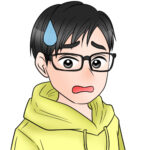
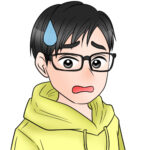
とは言え、
世の中には、お客様の知識が不足していることを利用し、ハイスペックな安全機器をダマして販売したり、品質の悪い粗悪品を売りつけたりする評判の良くない安全機器メーカーが存在するのも事実です。
現場作業で思うこと ―休憩は、こまめにしっかりと!―
今回のリスクアセスメントは4日間にわたる長丁場でしたが、あらかじめ計画を立てて、1日目は機械の作動状態の確認(5設備)、2、3、4日目は停止時間の確認(2設備ずつ、最終日1設備)というようなスケジュールでした。したがって、1日目はどうしてもタイトなスケジュールでせざるを得なかったのが現状でした。
そこでジュンイチロウさんは、2、3、4日目は適度に休憩時間を設けていました。というのも、通常のオフィス業務は、各個人で適度にトイレ休憩、たばこ休憩、お昼休憩等可能ですよね。オペレータさんたちも、工場ごとに適度に10分休憩が挟まれていたり、休憩時間が決まってあることが前提なので、「ここまで頑張ればひとまず休憩だ」という目安があります。
リスクアセスメントは、設備によって終わりの目安も、いつ休憩かも決まっておらず、流れで行ってしまうケースが多いと思います。実際に1日目は休憩時間が取れなかったので、同行したお客様は疲れ切っていました。リスクアセスメントを実際に行っている側は、ある程度手順や流れを把握しているので、終了時間の目安が分かります。ただし、リスクアセスメント初心者にとっては、今何を見ていて、どこまで時間がかかるのか全く不明の状況の中で、同じ場所にい続けなければいけないことが苦痛になってしまうこともあります。
だからこそ、もしリスクアセスメント経験者がリスクアセスメント初心者と同行する際には、下記のことを事前に伝えておくことをお勧めします!
- 設備全体の終了時間目安
- 休憩は何時間おきに取るか
- どのような流れで(場所、スペース、区画など)リスクアセスメントを行うか
- 箇所ごとに何を見ているか
コンサルティング業者にリスクアセスメントを依頼している場合は、リスクアセスメントをできる人間に育てたい人材に、上記を聞きながら行うように指示するとよいでしょう。
人間の集中力なんて大して持たないので、適度に休憩を挟みつつ、何ならこの休憩時間に質問等もできるので、一石二鳥にもなるかと思います。初心者は現場では聞きづらいこともありますし、現場はうるさすぎて互いの声も聞こえないことが多いです。したがって、見ているポイントごとに「次の休憩でここを聞きたい!」というように、意欲的にも取り組めると思います。
ジュンイチロウさんも2日目以降は、たくさん質問を受けていました。お客様の心をつかむ雑談はもちろんのこと、そこまで答えてくれるのかぁ、と思うほど専門的なところまで教えていらっしゃって、より信頼関係を築いていっているところが、さすがすぎました。


初心者としても、初めての経験で緊張感がありつつも、何をしているか分からない状態で終わりの見えない作業だと、どうしてもぼーっとしてしまう人も出てくると思います。休憩時間を通して徐々に質問しやすくなっていくことで、さらに知識と技術も吸収しやすくなると思いますし、今後の自分のリスクアセスメントの参考にもなるかと思います。こちらも事前に休憩時間と進め方についても打ち合わせを行っておいて、このような時間を有効活用して、より効率よくリスクアセスメントの実践と教育を充実させていくことをお勧めします!
リスクアセスメントで押さえるべき4つのポイント
今回の学びをまとめると、以下の4点が重要だと感じました。
- タッチパネルを活用する
- 現場で写真、数値データ、その他メモ等をその場で入力する手軽さと、写真付きでその場の状況を把握しておけるので、後からデータ整理に悩む時間を大幅に削減できます。
- 初期費用としても、後からの工数を考慮すると、圧倒的にコストを削減できると思うので、ぜひ導入をご検討ください。
- メジャーは2本以上持参する
- 特にISO 13855 に基づいた安全距離を測定する際には必須です。
- 最低限ライトカーテンを使用する際には、規格の理解と合わせてチーム全員でメジャーを持参するのがおすすめです!メジャーが1本だと精度に問題が出てきてしまい、現在の対策が適切かどうかの判断に誤りが生じかねないので、ご注意ください!
- 信頼性のある安全機器を選ぶ
- 日本ではプラグスイッチでも対応できてしまうことが多いですが、国際規格では認められていません。
- プラグスイッチはFA業界ではセーフティプラグと言われているのですが、安全をやっている人間からすると「どこがセーフティ?」と思ってしまうようなものですので、適切な認証を受けているメーカーの信頼性の高い安全機器を選ぶことで、リスクを減らしましょう。
- 休憩時間の確保を
- リスクアセスメントは初心者にとっては、思ったより重労働です。
- とくに今何を見ていて、次の休憩時間、終了時間が知らされていない状態ですと、ぼーっとしてしまって時間をやり過ごしてしまう可能性もあります。
- 全体の流れと、休憩時間、終了時間をきっちり伝えて、よりコミュニケーションがとりやすい環境づくりをしていくことを推奨します!
最後に
リスクアセスメントは、「なんとなく」でやると見落としが発生しやすいです。初めて行う方は、驚きが多いと思います。だからこそ、小さな工夫や準備で、リスクアセスメントにかかる時間も精度も、ぐっと向上すると思います!
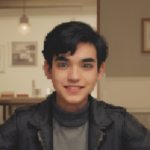
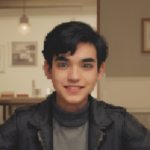
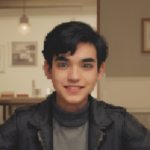
この機械にこんなにも時間が必要なのか!
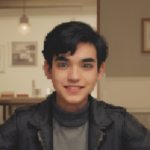
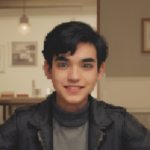
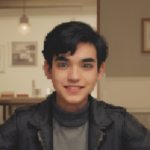
こんなにも危険事象を想定しなければならないのか!
初心者の方には、タッチパネルやメジャー2本持参など、簡単に実践できるポイントがあります。まず見られるのは安全機器か汎用機器かどうかを確認してみるのもいいでしょう!
忘れがちな休憩時間の確保も意外と重要ですので、ぜひ実践してみてください。
次回も、現場で得た学びや気づきをシェアしますので、お楽しみに!
それでは、また!
ガンタでした!