
リスクアセスメントとは?ISO12100の3ステップメソッドと安全化対策の落とし穴を現場で新人が学んだ事例【4日目】

目次
はじめに:「安全」をナメていた日
こんにちは!機械安全コンサルタントのジュンイチロウさんの弟子、新人ガンタです!
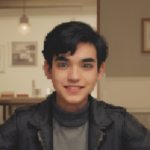
ガンタです!今日も頑張っていきます!
4日間にわたる、初めてのリスクアセスメント現場研修。正直に言うと、最初は「安全なんて、要は気をつけるかどうかの話でしょ?」くらいに考えていました。チェックリストを埋めて、危なそうなところに印をつければ終わり。そんな風に、どこか「安全」というものを少しナメていたかもしれません。
でも、この4日間で私のその考えは、良い意味で完全に打ち砕かれました。ジュンイチロウさんの隣で現場を見て、話を聞くうちに、「安全」がどれだけ深く、体系的で、そして時には直感に反するほどの専門知識を要する分野であるかを痛感したんです 。
このブログでは、そんなリスクアセスメント初心者の私が経験した「もっと早く知っておけばよかった!」という衝撃と学びのポイントを、私自身の言葉でシェアしていきたいと思います。これは、ただの研修記録ではありません。私が「安全」の本当の意味を初めて知った、変革の物語です 。
最初の衝撃:「安全」だと思っていたマットスイッチの落とし穴
研修最終日、私たちの前に現れたのはマットスイッチが設置された機械でした。それを見た瞬間、私は「あ、やっぱり…」と心の中でつぶやきました。エリアセンサーが置けないレイアウトやコストの問題で採用されることが多い、おなじみの安全対策です。
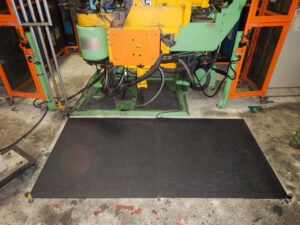
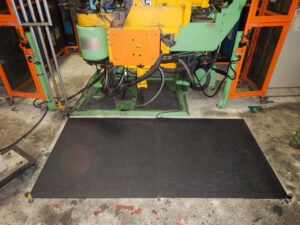
しかし、そのマットスイッチを一瞥したジュンイチロウさんは、私には見えていなかった「本質」を瞬時に見抜いていました。
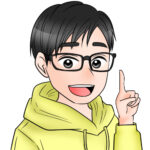
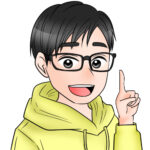
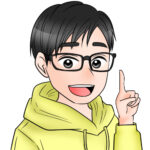
ガンタ君、このマットスイッチは『汎用』やん!
その一言が、私にとって最初の衝撃でした。インターネットで検索してヒットするマットスイッチのほとんどは、実は安全規格を満たさない「汎用機器」だというのです。見た目は同じでも、その中身は全くの別物。私たちの工場にあるものも、もしかしたら…と冷や汗が出ました 。
ジュンイチロウさんの解説は、私の浅い知識を根底から覆すものでした。安全回路の基本は「NC 接点(b 接点)」、つまり「常に安全であることを監視し、異常(断線など)があれば停止信号を出す」という考え方です。これを「フェールセーフ(fail-safe)」と言い、何かが壊れても安全側に倒れるという、安全設計の根幹をなす哲学です。
ところが、マットスイッチは構造上、「人が踏んだ時(危険な時)に回路が閉じる」、つまり「NO 接点(a 接点)」の仕組みになっています。これは「危険検出型」と呼ばれ、もし配線が切れてしまったら、人が踏んでも信号が送られず、機械は止まりません。システムが危険を検知できないまま、故障してしまうのです 。
この根本的な問題を解決するため、「安全マットスイッチ」は、必ず専用の「安全リレーユニット」や「安全PLC」とセットで使われるように指定されています。この専用コントローラが、NO 接点の信号や配線の状態を常に賢く監視し、万が一の断線があっても異常を検知して機械を止める、擬似的なフェールセーフ機能を実現しているのです。
つまり、私が学んだ教訓は、「安全は見た目では判断できない」ということ。そして、その本質を見抜くための具体的な方法があるということです。
特徴 | 汎用マット | 安全マット |
制御の考え方 | 危険検出型(危険な時だけ信号ON) | 安全確認型(常に安全を監視し、異常で信号OFF) |
断線時の挙動 | フェールアンセーフ(危険を検知できなくなる) | フェールセーフ(専用コントローラが異常を検知し停止) |
制御機器 | 一般のPLCやリレーに直接接続 | 専用の安全リレーユニットや安全PLC が必須 |
見分け方 | 制御盤に専用の安全制御機器がない | メーカー指定の安全制御機器が必ず存在する |
結果 | 隠れた危険源となり、規格の要求を満たせない | 要求されるパフォーマンスレベル(PLr)を満たすことができる |
この一件以来、私は現場で安全装置を見るとき、まず「これは本当に『安全』と呼べるものだろうか?」と疑うことから始めるようになりました。それは、安全への向き合い方が変わった瞬間でした。
安全の基本原則:「3 ステップメソッド」という考え方
マットスイッチの一件で、私はジュンイチロウさんの判断の裏には、何か体系的な思考プロセスがあるに違いないと感じ始めました。その問いに答えるように、ジュンイチロウさんが教えてくれたのが、機械安全の国際規格ISO 12100 で定められている、リスク低減の基本原則「3 ステップメソッド」でした 。
これは、安全対策を考える上での「優先順位」を示す、非常に強力な思考のフレームワークです。
ステップ1:本質的安全設計方策
これは最も優先されるべき、最強の安全対策です。「危険源そのものを、設計の段階でなくしてしまう」という考え方です。
例えば、鋭い角を丸くする、有害な物質を使わない、そもそも人が近づく必要のない自動化された工程にする、といったことが挙げられます。
ステップ2:安全防護および付加保護方策
ステップ1 で危険源を取り除けない場合に、次善の策として講じます。これが、いわゆる「安全装置」の追加です。
具体的には、物理的な柵(ガード)で危険な場所を囲ったり、センサーや先ほどの「安全マットスイッチ」のような保護装置を使って、人が近づいたら機械を止めたりします 。
ステップ3:使用上の情報
ステップ1 と2 を尽くしても、なおリスクが残ってしまう場合の最後の手段です。警告ラベルを貼ったり、取扱説明書に注意点を明記したり、作業員に特別なトレーニングを実施したりすることで、人に注意を促し、リスクを回避してもらう方法です。
しかし、ここでジュンイチロウさんは、私にとって非常に重要な実践的な視点を教えてくれました。私たちが今回扱っているような「既存の設備」の改善では、この優先順位が逆転することが多い、というのです。なぜなら、すでに完成している機械の根本的な設計を変える(ステップ1)のは、現実的に不可能か、莫大なコストがかかるからです。
そのため、既存設備のリスクアセスメントでは、まず「どこにガードが足りないか?(ステップ2)」「どんな情報提供が必要か?(ステップ3)」という視点から対策を考え始めることが、現実的なアプローチになるのです。この視点があったからこそ、ジュンイチロウさんが次に安全柵(ガード)のチェックに、あれほど時間をかけていた理由が、私にはっきりと理解できました。
ステップ | 目指すこと | 身近な例え | 現場での例 |
ステップ1 | 危険そのものを無くす | そもそも崖の近くに道を作らない | (既存設備では困難な)機械の根本的な設計変更 |
ステップ2 | 危険から人を隔離する | 崖に頑丈な柵を立てる | 適切な安全柵の設置、正しいマットスイッチの使用 |
ステップ3 | 危険を知らせる | 「この先、崖」の警告看板を立てる | 警告ラベルの貼付、操作マニュアルの改訂 |
この3ステップメソッドは、単なる手順ではありません。安全を確保するための「思考の地図」そのものなのです。
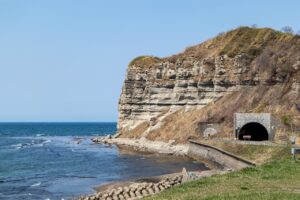
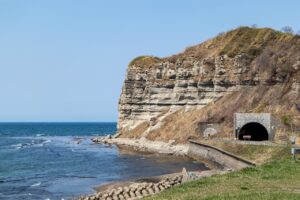
なぜ、ジュンイチロウさんはメジャーで隙間を測り続けるのか?
3ステップメソッドを理解した私の目の前で、ジュンイチロウさんはメジャーを取り出し、安全柵のあらゆる隙間を黙々と測り始めました。柵の上から乗り越えられないか、下から潜り込めないか、そして柵の網目のひとつひとつまで。最初は「そこまでやるのか…」と圧倒されるばかりでしたが、その行動のすべてに国際規格に基づいた明確な理由があることを知り、私は再び衝撃を受けました。
ジュンイチロウさんのメジャーが示していたのは、ISO 13857(危険区域に上肢及び下肢が到達することを防止するための安全距離)という規格の数値でした。この規格は、「ガードの開口部の大きさがこれくらいなら、危険源からこれだけ離しなさい」という具体的な距離を定めています。これは、人間の腕の長さや体の大きさといった、人間工学(エルゴノミクス)と身体測定(アントロポメトリー)の科学的なデータに基づいています。
例えば、ジュンイチロウさんが現場でつぶやいた
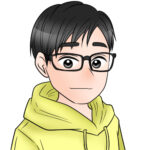
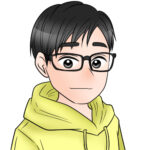
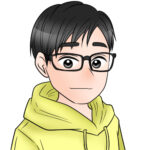
幅120 mmの隙間があれば、腕が肩まで入る可能性があるから、危険源まで850 mmの距離が必要になるよ!
「幅120 mmの隙間があれば、腕が肩まで入る可能性があるから、危険源まで850 mmの距離が必要になる」という言葉 。これは、まさにISO 13857に定められた数値そのものだったのです。つまり、「安全な距離」とは感覚で決めるものではなく、科学的な根拠に基づいて算出される、客観的な数値なのです。
さらに、ガードそのものの強度や材質にも、ISO 14120(ガードの設計及び製作のための一般要求事項)という厳しいルールがあります。この規格では、ガードは予見される衝撃に耐える強度を持ち、工具を使わなければ簡単に取り外せず、よじ登りにくい構造であることが求められます。
だからこそ、現場でよく見かけるプラスチックダンボールやネットは、ガードとは見なされないのです。それらは簡単に破壊したり、たわませたりして危険源に到達できてしまうからです。
ジュンイチロウさんがメジャーで隙間を測る行為は、単なる測定ではありませんでした。それは、機械と人の間に、科学的根拠に基づいた「絶対的な安全領域」を確保するための、極めて重要な作業だったのです。この学びを通じて、私は安全規格が単なる規則ではなく、人間を機械の危険から守るための、先人たちの知恵と科学の結晶であることを深く理解しました。
「そんなに費用がかかるの?!」報告書の重みと未来への投資
4日間の評価が終わり、対策事項がリストアップされた時、お客様の口から思わず漏れた一言が、私の心に突き刺さりました。「そんなに費用がかかるの?!」。
高っ!そんなに費用がかかるんや!
その時、私はリスクアセスメントのもう一つの側面、その「重み」を学びました。私たちが作成するリスクアセスメントのレポートは、単なる提案書ではありません。一度文書として記録されると、それは企業が対策を講じるべき「義務」となり、会社全体の経営判断に直結するのです。対策を怠れば、万が一事故が起きた際に企業の責任が厳しく問われることになります。ジュンイチロウさんの言葉を借りれば、「会社が傾きかねないレベルの話」に発展することもあるのです。
では、なぜこれほどまでに費用がかかってしまうのか。ジュンイチロウさんは、その背景にある歴史的・文化的な違いを話してくれました。ヨーロッパでは、産業革命の早期から大きな事故を経験し、また、言語の違う労働者が共に働く環境が当たり前だったため、「言わなくても分かる」という人に依存した安全ではなく、「仕組みで危険を防ぐ」機械安全の考え方が発展しました。
一方で、日本では高度なチームワークと「阿吽の呼吸」で、人に依存した安全対策でも多くの事故を防げてきた歴史があります。しかし、グローバル化が進み、多様な背景を持つ人々が働くようになった今、その前提は崩れつつあります。これまで安全にかけてこなかった投資のツケが、今、大きな負担となって現れているのです。
しかし、この話には続きがあります。ジュンイチロウさんは、この「コスト」を「未来への投資」と捉え直す視点を教えてくれました。
「日本のメーカーの多くは、まだこの安全構築が十分ではない。ということは、きちんとやれば、それは他社にはない強力な差別化要因になるんだ」と。
国際的な安全規格(例えばCEマーキングなど)に適合した機械は、海外市場への扉を開きます。品質や価格での競争が激化する中で、「安全」という新しい価値軸で勝負できる。それは、未開拓の広大な市場、「ブルーオーシャン」に乗り出すようなものだ、とジュンイチロウさんは語ります。
お客様の驚きの声を聞いた時、私はただコストの大きさに怯んでいました。しかし、今なら分かります。リスクアセスメントの報告書は、単なる「請求書」ではありません。それは、会社の未来を守り、新たな成長機会を掴むための「戦略的なロードマップ」なのです。
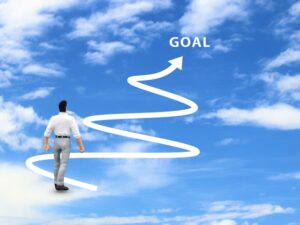
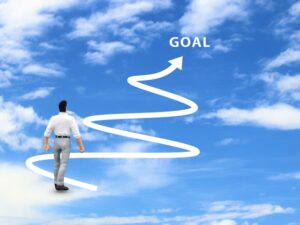
まとめ:リスクアセスメント初心者が明日からできること
4日間の現場研修は、私にとってまさに目から鱗が落ちる体験の連続でした。リスクアセスメントとは、お客様の会社の未来を左右するほど重要で、深い知識とコミュニケーションが求められる仕事なのだと、身をもって知りました。この経験を通じて私が学んだ、初心者が明日から心に留めておくべき3つのことを、最後にまとめたいと思います。
1. 「当たり前」を疑う目を持つこと
現場にあるマットスイッチや安全装置を見て、「安全なものだ」と鵜呑みにしないでください。私が学んだように、見た目が同じでも全く機能しない「汎用品」かもしれません。まずは「これは本当に安全だろうか?」と問いかけ、その証拠(例えば、専用の安全コントローラの有無)を探す癖をつけることが、第一歩です。
2. 最も強力な武器は「物理的なガード」だと知ること
複雑な安全回路を考える前に、まずやるべきことがあります。それは、危険源にそもそも近づけなくする、堅牢で適切な「安全柵」や「ガード」を設置することです。3ステップメソッドが示す通り、物理的に危険から人を隔離することが、最も効果的で基本的な安全対策です。まずは、ガードの隙間や強度から見直してみてはいかがでしょうか。
3. 安全を「コスト」ではなく「未来への投資」と捉えること
安全対策には確かにお金がかかります。しかし、それは事故を防ぐだけでなく、会社のブランドイメージを高め、グローバルな競争力を手に入れるための、最も確実な投資の一つです。今、安全に取り組むことは、未来の会社を支える大きな資産になる可能性があります。
この4日間、私に根気強く指導してくださったジュンイチロウさん、そして研修を受け入れてくださったお客様に、心から感謝しています。まだまだ未熟な私ですが、この経験を糧に、お客様の力になれる真の専門家を目指して、これからも学び続けていきたいと思います。
ここまで読んでくださった皆様、本当にありがとうございました!
ガンタでした!