
初心者向けリスクアセスメント入門:具体例で学ぶ安全対策の第一歩|ガンタの初めてのリスクアセスメント体験記 |ジュンイチロウから学んだこと

みなさん、こんにちは!ジュンイチロウです。大変ご無沙汰しております!
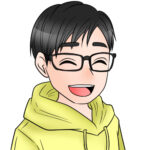
こんにちは!
「ブログ、まだ?」「いつも楽しみにしてますねん!」そんな皆様からの温かい応援メッセージ、本当に嬉しく、そして…更新が遅れてしまって、ごめんなさい!🙇♂️でも、「ブログ、役に立ってるよ!」というお声を聞くと、「ああ、続けてきてよかった…!」と、心から感謝の気持ちでいっぱいになります。本当にありがとうございます!
さて、今回の記事は、なんと!私の弟子、期待の新人・ガンタ君がメインライターを務めます!
先日、4日間のリスクアセスメントに同行してもらったのですが、そこで彼が感じたこと、学んだことを、フレッシュな視点で綴ってくれました。初めてのリスクアセスメント…きっと、ドキドキと発見の連続だったはず。
「なるほど、そういう見方もあるのか!」と、私自身も勉強になることがたくさんありました。
もちろん、まだまだ至らない点もあるかと思いますが、そこは「伸びしろ」ということで…(笑)、温かい目で見守っていただけると嬉しいです!
これからも、皆さんの「知りたい!」に寄り添えるような、そんなブログを目指して頑張りますので、どうぞ応援よろしくお願いします!📣
目次
ドキドキの初日!現場でジュンイチロウさんの背中を追いかけて
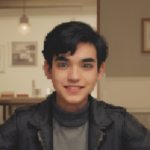
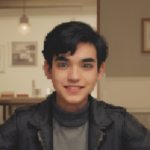
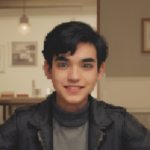
こんにちは!ジュンイチロウさんの弟子、ガンタです!
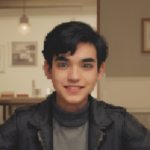
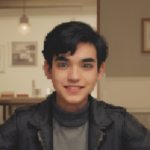
今回は、リスクアセスメント初心者の私が、初めて現場を体験して学んだことや気づきを、みなさんにシェアしたいと思います。「リスクアセスメント」って聞くと、なんだか難しそうなイメージがありますよね?
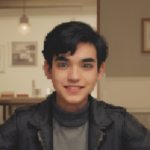
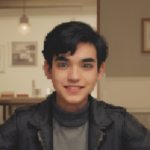
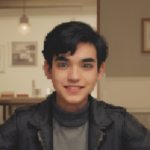
なるほど、こうすればいいのか!
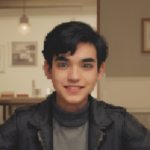
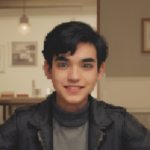
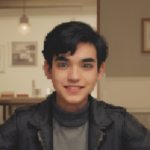
事前にこれを知っておけば…!
でも、実際に体験してみるとと思うことがたくさんありました。私の記念すべきリスクアセスメント初日は、ジュンイチロウさんに同行させていただく形でのスタートでした。
- 機械の稼働状況の確認
- 標準作業手順の確認
- 機械の動作と停止条件のチェック
- オペレーターの方々とのコミュニケーション
- 制御盤やレイアウト図の確認リスト
4日間にわたる現場作業の初日ということで、この日は特に準備と確認作業が中心でした。
正直に言うと、最初はもう何が何だか…(笑)。ジュンイチロウさんの後をひたすらついて回るだけで精一杯。どこを見て、何をどう確認すればいいのか、全くわかりませんでした。
でも、ジュンイチロウさんの動きを間近で見ているうちに、少しずつ「リスクアセスメントの視点」のようなものが分かってきたんです。例えば、ジュンイチロウさんは、機械の動きをただ見るだけでなく、オペレーターの方が普段どのように作業されているか、どんな時に危険を感じるかを、丁寧にヒアリングしていました。
「なるほど、リスクアセスメントって、ただ機械を見るだけじゃなくて、人と機械の関係性を見ることが大切なんだ!」
そう気づいた瞬間でした。
稼働中の機械観察から始まる、リスクアセスメントの第一歩
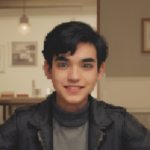
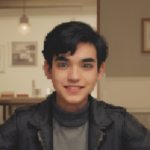
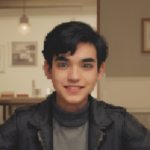
リスクアセスメントって、一体何から手を付ければいいんだろう?
初めてリスクアセスメントに同行した日、私の頭の中はそんな疑問でいっぱいでした。皆さんも、最初はそうではありませんか? ISO 12100 には手順が記載されていますが、実際に機械を目の前にすると、どこから危険を見つけ出せばいいのか、戸惑ってしまうものです。
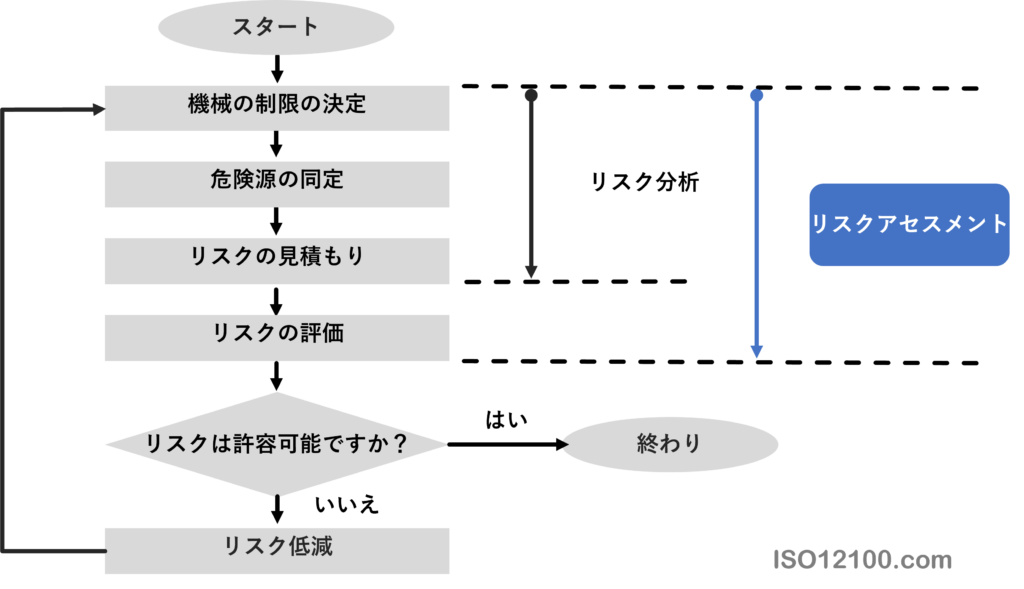
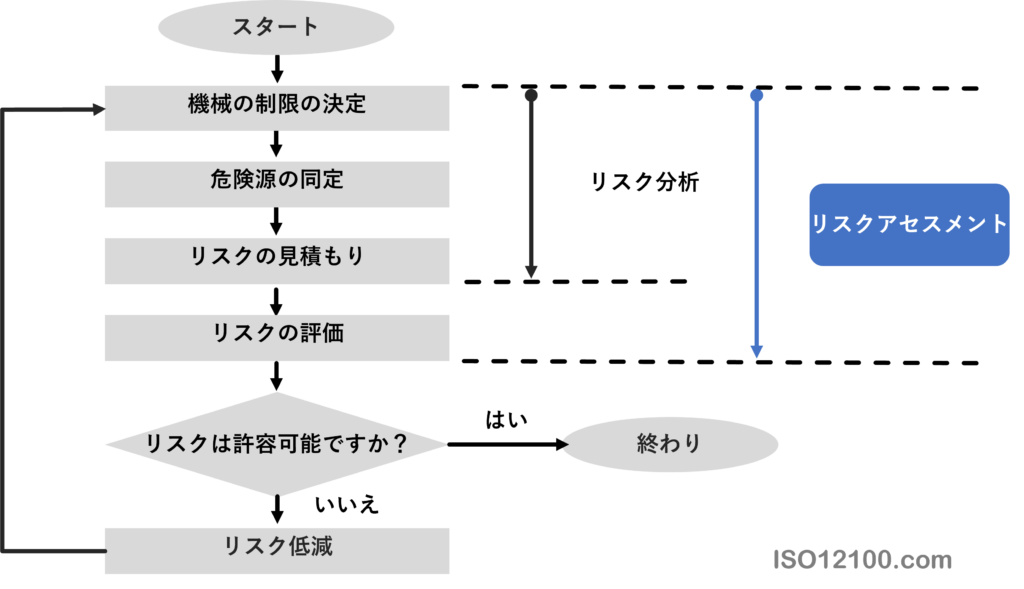
ついつい、機械が停止した状態で危険源を探し始めてしまいがちです。もちろん、生産スケジュールの都合上、止まっている機械しか見られない、時間がない、という状況も多いと思います。ジュンイチロウさんも、過去には止まっている機械だけでリスクアセスメントをせざるを得ない状況もあったそうです。
しかし、今回のリスクアセスメントでは、ジュンイチロウさんは4日間かけて、すべての機械が動いている状態を観察する時間を確保していました。そこには、大きく分けて2つの理由がありました。
理由1: 稼働状態だからこそ見える、オペレーターの「癖」と「潜在的な危険」
1つ目の理由は、実際に機械が動いている状態を見ることで、オペレーターの「癖」や、それが生み出す「潜在的な危険」が見えてくるからです。例えば、今回の現場では、あるオペレーターが生産効率を上げるために、定められたルールを無視して近道行動を取っている場面を目撃しました。これは、重大な事故に繋がりかねない、非常に危険な行動です。
- 図面上と実際の取り付け位置が異なる
- 作業標準手順書には記載されている手順が、実際には省略されている
他にも、普段の稼働状態でなければ見えてこない問題点が、次々と明らかになりました。ジュンイチロウさんは、「リスクアセスメントで最も重要なのは、重大な危険源、危険事象を見逃さないこと」だと強調します。停止状態だけでは、これらの「実働状態の危険」を見落としてしまう可能性が高くなってしまうのです。
理由2: 安全回路の「本当の姿」を確認する
2つ目の理由は、機械の停止条件(ドアが開いてドアスイッチが反応する、非常停止ボタンが押されるなど)と復帰条件(リセットボタンが押されるなど)を明確にすることで、安全回路が正しく機能しているかを確認するためです。機械が停止している状態では、電源が入っていないため、どのように機械が停止・復帰するのかを、オペレーターへのヒアリングや、最悪の場合は作業手順書だけで判断することになります。
- 「ここを押せば止まる」とオペレーターが言った場所と、実際に停止する場所が違う
- 使われていないボタン(機能していないボタン)がある
- オペレーターが何のボタンか理解していない箇所がある
しかし、今回の現場では、実際に機械を動かしてみないと分からない問題が、数多く見つかりました。さらに、配線切れやボタンの故障だけでなく、「安全回路になっていない」という、より深刻な問題も明らかになりました。
例えば、非常停止後の意図しない再起動の防止については、ISO 13850 や ISO 14118 などに規定があります。非常停止ボタンを押してラッチを戻した際に、すぐに機械が動き出さないように設計する必要があるのです。しかし、汎用PLCに非常停止ボタンを接続しただけの場合、ラッチを戻すと自動的に再起動してしまう、PLCが故障した場合には同様の危険な状態が発生する可能性があります。
今回の設備の中にも、非常停止ボタンを押して停止させた後、ラッチを戻した途端に動き出してしまう機械がありました。実際に機械を動かして停止させることで、安全回路が正しく組まれているかを、目で見て確認できるのです。
プロの技:ジュンイチロウさんの「観察眼」と「手際の良さ」
ジュンイチロウさんは、これらの確認作業を、驚くほどスムーズに進めていました。
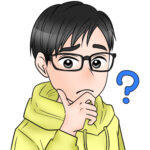
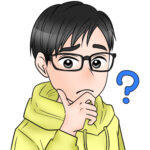
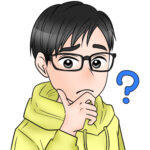
ここのボタンを押したらどうなりますか?
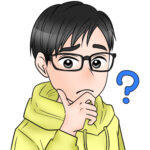
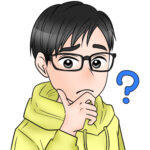
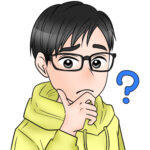
ボタンを戻したらどうなりますか?
オペレーターの認識と実際の動作とのギャップを、一つ一つ丁寧にメモに取りながら、手際よく確認していく姿は、まさにプロフェッショナル。予定していた時間よりも早く作業を終えてしまうほどでした。
まとめ: 稼働状態の観察は、リスクアセスメントの「必須工程」
今回の経験を通して、私は、稼働状態の機械を観察することが、リスクアセスメントにおいて「必ず必要な工程」であると痛感しました。
- 動いている状態だからこそ、オペレーターの意識や癖、そして潜在する危険源が見えてくる
- 安全機器は、ただ取り付けられているだけでは意味がない。
- 見た目が良くても、本来の機能を果たさなければ、リスクを低減したことにはならない
この2点を意識することで、形だけの、書面上だけで終わってしまうリスクアセスメントから、本当に危険を取り除くための、もう一段階上のリスクアセスメントへとステップアップできると、私は確信しています。
オペレーターとの対話で「見えない危険」をあぶり出す
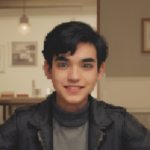
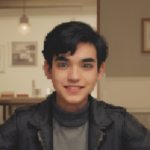
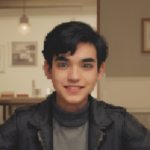
リスクアセスメントって、機械だけを見ていればいいんじゃないの?
そう思っていた時期が、私にもありました。でも、それは大きな間違い。実は、オペレーターとの対話こそが、リスクアセスメントの成否を握る、非常に重要なポイントなのです。
なぜオペレーターとの対話が重要なのか?
ISO 12100 では、危険源を特定する際に、ある程度、種類を絞り込む必要があるとされています。機械的な危険源や電気的な危険源など、目に見えやすい危険源や危険事象は、図面を見たり、機械をざっと見たりするだけでも、ある程度は想像できます。
しかし、忘れてはならないのが、「人間工学無視による危険源」の存在です。これは、オペレーターとの対話なしには、なかなか見えてきません。
実は、この台車が重くて、腰を痛めやすいんです
この作業台、使いづらいけど、仕方なく使っているんです
今回の現場でも、人間工学的な配慮が不足しているために生じる危険源が、数多く見つかりました。
さらに、危険源の特定には、オペレーターの「意図しない挙動」や「合理的に予見可能な誤使用」を考慮する必要があります。その中には、「近道行動をとった結果として生じる挙動」も含まれており、オペレーターがどのような状況で近道行動をとるのかを把握することが、非常に重要になってきます。
ジュンイチロウさん流、対話術の極意
ジュンイチロウさんは、冗談を交えながら、オペレーターから自然に話を引き出す名人です。1日の稼働時間、生産数、日々の習慣など、様々な情報を聞き出し、そこから見落としがちな危険源を、次々とあぶり出していました。
ジュンイチロウさんの話を聞いていると、現場の方は、良くないことをしている自覚がある場合、正直に話さないことがある、ということに気づかされました。人間、誰しも自分を守ろうと無意識に行動してしまうものです。
- 「しんどさ」に共感する
- 「本当はこうしたいんじゃないですか?」と寄り添う
そんな彼らから、正直な意見を引き出すためには、といった、ジュンイチロウさんのような、相手に寄り添う姿勢が大切だと感じました。「そうなんですよー、実は…」という言葉を引き出せた時、初めて、本当の危険が見えてくるのかもしれません。私も、ぜひ実践してみたいと思います!
チーム編成の「落とし穴」と「最適解」
今回のリスクアセスメントでは、設計や保全担当者が同行していなかったため、オペレーターの話と実際の機械の挙動にズレがある場面もありました。これは、次回への改善点です。一方で、同じ役割の人が大勢同行することも、あまり良くないと感じました。工場の現場は騒音が大きい場所が多く、大人数いても、手持ち無沙汰になってしまう人が出てきてしまうからです。
お客様の中には、「外注したからには、一人でも多くの社員にリスクアセスメントを学んでほしい」と思われる方もいらっしゃるかもしれません。しかし、実際には、同行して説明を聞いても、3、4人程度しか状況を理解できず、他の人は雑談を始めてしまったり、自分の仕事が気になってしまったり…ということが少なくありません。
- まずは、外注先を通して、3、4人の「できる人」を育てる
- その3、4人を、それぞれの機械に分散させ、さらに3、4人ずつ指導する
リスクアセスメントをできる人を増やしたいのであれば、少人数から始めていくのが、効果的だと感じました。
「初心者」の視点が、新たな発見を生む
また、リスクアセスメントのチームには、「初心者」を1人入れておくことも重要です。
普段、設備を見慣れている人は、「危険な状態」が「いつもの光景」になってしまい、危険だと認識できない可能性があります。初心者の、新鮮で率直な意見は、新たな危険源を発見する、貴重なきっかけになるかもしれません。もし、人員が足りない場合は、手が空いている業務の方や、普段は現場にいない部署の方でも構いません。ただし、社内でリスクアセスメントをできる人材を増やしたいのであれば、異なるライン、異なる設備の担当者の方が、より多くのメリットがあるかもしれません。
図面とレポートは、リスクアセスメントの「羅針盤」…そして、未来への「架け橋」
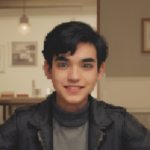
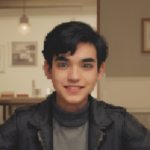
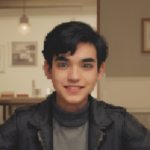
リスクアセスメントって、現場を見るだけでしょ?
…と、私も最初は思っていました。しかし、現場での作業を進めるうちに、図面やレポートが、まるで航海の羅針盤のように、リスクアセスメントを正しい方向に導く、非常に重要な役割を果たしていることに気づきました。そして、それらは単なる「過去の記録」ではなく、安全な未来を築くための「架け橋」でもあると、私は感じています。
なぜ図面とレポートが重要なのか?
リスクアセスメントは、「危険を見つける」だけでは終わりません。見つけた危険事象を改善して、初めて意味を成します。特に、電気的な危険源など、実機を見ただけでは分からない部分の対策を検討する際、図面やレポートは、対策の有無を証明する、非常に重要な書類となるのです。
例えば、通常、図面と一緒に保管されているはずのEMC試験のテストレポートがない場合、リスクアセスメントの報告書には、「問答無用で(EMC試験を)やりましょう」と書かざるを得なくなります。これは、ISO 13849-1 に記載されているCCF(共通原因故障)評価において、EMC 試験を行わないだけで25点もマイナスになってしまい、結果として、要求されるPLr(パフォーマンスレベル)を達成できなくなる可能性があるからです。
実は(EMC試験は)やってあったのに…
もし、後からそう判明しても、レポートがないために、再度EMC試験が必要となり、1台につき100万円前後の追加費用が発生してしまう…なんてこともあり得るのです。多くのお客様が、こうした文書の保管に、あまり注意を払っていないのが現状です。非常にもったいない状況を生まないためにも、図面やレポートの重要性を、改めて認識する必要があると感じました。
あわせて読みたい

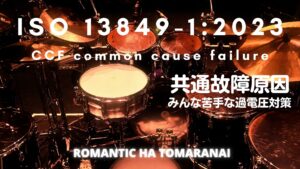
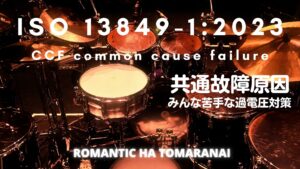
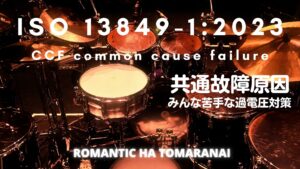
ISO13849-1:2023付属書F共通故障原因CCF(Common Cause Failure)を解説と過電圧(overvoltage)の解説
あらすじ みなさん、こんにちは! 最近、ISO 13849-1 のCCF(共通故障原因) について、たくさんの質問や問い合わせが寄せられています。 PL(パフォーマンスレベル)を求…
「リスクアセスメントレポート」と「セーフティコンセプトレポート」の違い
もう一つ、私が学んだ重要なポイントは、「リスクアセスメントレポート」と「セーフティコンセプトレポート」の違いを理解することです。
リスクアセスメントは、危険事象を洗い出す作業であることは、多くの方が理解しています。しかし、セーフティコンセプトレポートを、「図面に赤ペンで修正を入れる作業」だと思っている方もいらっしゃるのではないでしょうか? 実は、私もそう思っていました。
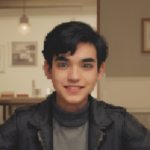
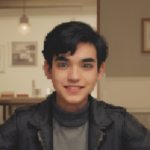
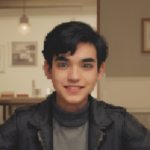
セーフティコンセプトって図面に赤ペン先生では??
しかし、実際には、セーフティコンセプトレポートは、リスクアセスメントの結果に基づいて、対策案をより具体的に説明するレポートです。例えば、リスクアセスメントで ISO 13849-1 に従って、PLr=d が必要と判断された危険事象に対して、具体的なメーカーの型式を挙げながら、推奨する対策案を提示する、といったイメージです。
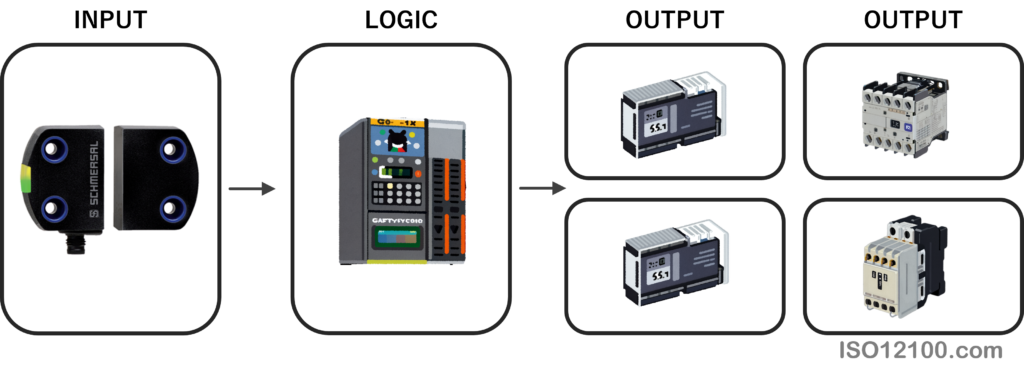
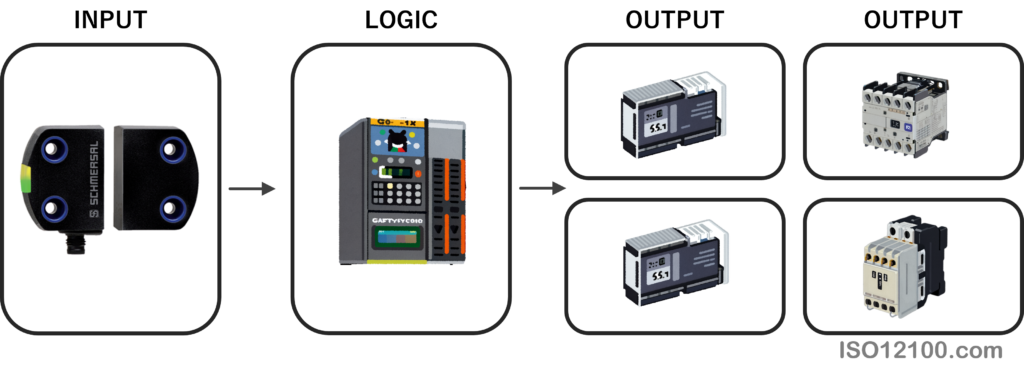
もし、セーフティコンセプトレポートの段階で、図面に直接修正を加えて、何か問題が発生した場合、「ごめんなさい」では済まされません。図面の作成を依頼する場合は、「セーフティコンセプト」ではなく、「安全設計」として、コンサルティング契約を結び、正式な手順を踏む必要があるのです。
安全構築のステップ
安全を構築する際には、以下の手順で、外注業者とレポートの内容について、認識を一致させることが重要です。
- リスクアセスメントレポート
- セーフティコンセプトレポート
- 安全設計(図面作成)
- 施工
- バリデーションレポート(妥当性確認)
今回のリスクアセスメントでは、この認識合わせに、少し時間がかかってしまいました。今後は、より分かりやすい説明を心がけ、お客様とのスムーズな連携を目指していきたいと思います。
図面とレポートは、過去と未来をつなぐ
図面やレポートは、リスクアセスメントを行う時だけでなく、その後のすべての工程においても、非常に重要な役割を果たします。もし、これらが十分に用意されていないと、危険源を正確に洗い出すことができず、十分な対策が施されていないレポートが出来上がってしまう可能性があります。
そして、万が一、事故が発生してしまった場合、対策について問われることになります。その時、内容が不十分なレポートでは、全く意味を成さない…という事態にもなりかねません。
リスクアセスメントの本来の目的は、事故が起こらないような、安全な設備を構築することです。図面やレポートが、その目的達成のために、いかに重要であるか…この認識を事前にしっかりと持つことで、図面やレポートの保存体制、そして活用方法が、大きく変わってくるのではないかと、私は感じています。
ジュンイチロウさんの「目」
とはいえ、図面を見ただけで、どこが安全回路で、どこが汎用制御回路なのか…私には、まだ一目で判断することはできません。しかし、ジュンイチロウさんは、全体図面をパッと見ただけで、「安全回路はここからここまでなので、この情報だけください」と、非常に短時間で判断していました。
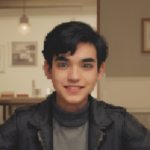
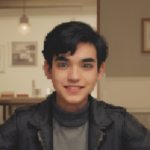
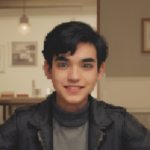
すごすぎる…
私も、いつかジュンイチロウさんのように、図面から瞬時に安全回路を見抜けるようになりたい!…そう強く思いました。
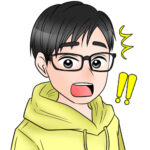
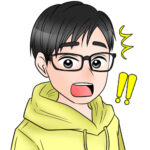
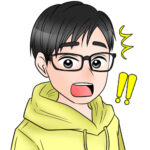
うっ
事前の準備で、スムーズな連携を
最後に、私のオススメは、リスクアセスメントを依頼する機械が決まった時点で、図面とレポート一式を用意していただき、実機を確認してリスクアセスメントの見積もりを行う際に、それらを活用させていただくことです。
事前に必要な情報が明確になれば、図面やレポートを用意する側も、開示すべき部分が明確になります。そして、見積もりを行う側も、より正確な情報に基づいて、見積もりを提示することができます。
双方がスムーズに連携し、より安全な設備を共に築き上げていく…そんな未来を目指して、私も日々、学びを深めていきたいと思います!
リスクアセスメントは「時間」との戦い!? ~現場で学んだスケジューリングの重要性~
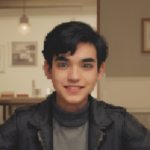
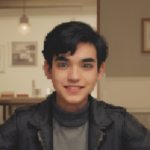
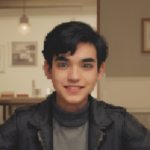
リスクアセスメントって、機械が動いているところを見るんでしょ?
…と、私も最初は思っていました。確かに、リスクアセスメントの冒頭では、機械が稼働している状態を確認することも重要です。しかし、実際に現場に同行して分かったのは、リスクアセスメントにかける時間の多くは、機械が「停止している時」に確認作業を行う、ということでした。
なぜ「停止時間」が重要なのか?
リスクアセスメントでは、機械の内部構造や、安全装置の動作など、稼働中には確認できない部分を、詳細にチェックする必要があります。そのため、「稼働しているが、生産していない時間」と「停止している時間」を、意図的に確保することが、非常に重要になってくるのです。
これは、お客様側の生産スケジュールとの兼ね合いもあり、最も部署間での調整が必要となる部分かもしれません。
スケジュール調整の落とし穴…
実は、この日程調整が遅れてしまい、本来リスクアセスメントを行う予定だった時期を逃してしまう…というケースが、少なくないそうです。
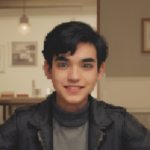
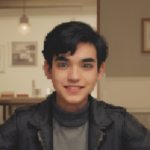
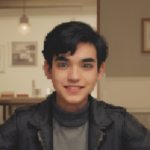
せっかくリスクアセスメントをしようと思ったのに…
そんな事態にならないためにも、事前の準備段階で、しっかりとスケジュール調整を行うことが重要だと、私は学びました。
見積もり時の「時間」チェック!
スケジュール調整をスムーズに進めるためのオススメの方法は、見積もり時に、金額だけでなく、「稼働しているが生産していない時間」と「停止している時間」が、それぞれどれくらい必要か…を、外注業者に提示してもらうことです。
リスクアセスメントって、具体的に何時間くらいかかるの?
…と、疑問に思われる方も多いと思います。事前に必要な時間を把握しておくことで、お客様側も、生産スケジュールとの調整がしやすくなるはずです。
リスクアセスメントの業者選び…「時間」は重要な判断基準!?
リスクアセスメントを依頼したいけど、どこに頼めばいいか分からない…
そんな悩みをお持ちの方も、いらっしゃるかもしれません。
もし、業者選びで迷った時は、「金額」や「メーカーブランド」だけでなく、「実施時間」も、重要な判断基準になる…ということを、ぜひ覚えておいてください。
見積もりの内容があまりにも大雑把だったり、実施時間が明らかに短すぎる、または長すぎる…さらに言うと、「稼働時間」と「停止時間」を提示してこない場合は、質の高いレポートを期待できない可能性がある…と、ジュンイチロウさんは言っていました。
ジュンイチロウさんの「時間感覚」
ジュンイチロウさんは、機械の大きさや複雑さに合わせて、必要な稼働時間と停止時間を、的確に判断していました。今回は、お客様から見積もり時に提供された情報が少なかったため、大まかな時間設定となりましたが、それでも、当日の稼働時間に関しては、ほぼ予定通りに作業を終えていました。
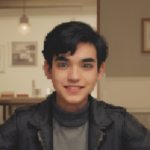
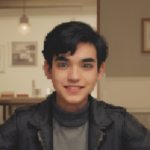
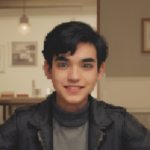
さすが、ジュンイチロウさん…!
私も、ジュンイチロウさんのような、鋭い「時間感覚」を身につけたい…と、改めて思いました。
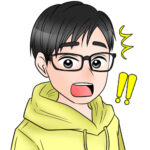
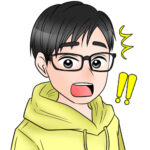
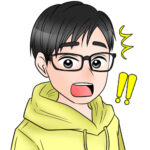
ひょえー
「学び」を「自社」の力に
多くのお客様が、「リスクアセスメントを、どう進めれば良いか分からない…」と感じていると思います。最初は外部の業者に依頼し、その作業を社員に学ばせて、将来的には自社でリスクアセスメントを実施できるようにしたい…と、考えている担当者の方も多いのではないでしょうか。
今回の学びを通して、私も、リスクアセスメントの知識やスキルを、さらに深めていきたい…と、強く感じています。そして、いつか、この「学び」を、自社の力に変えていけるよう、日々、努力を続けていきたいと思います!
リスクアセスメントは「準備」が9割! ~新人ガンタが学んだ、現場で活かせる4つのポイント~
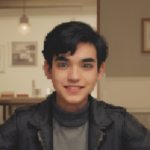
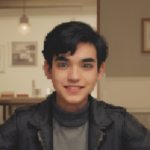
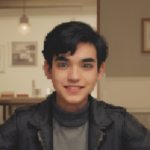
リスクアセスメントって、奥が深い…!
初めての現場同行を終えた、私の率直な感想です。今回の経験から、「次回からは、こうしよう!」と強く思ったポイントを、4つにまとめてみました。
1.メンバー選定は「多角的」に!
リスクアセスメントには、普段から機械を操作しているオペレーターだけでなく、設計担当者や保全担当者も参加するのが理想的です。それぞれの視点から意見を集めることで、より多角的に、そして正確にリスクを評価することができます。
ただし、人数が多すぎると、作業の邪魔になってしまったり、手持ち無沙汰になってしまう人が出てくる可能性も…。ジュンイチロウさんによると、以下のメンバー構成がオススメだそうです。
- ファシリテーター(リスクアセスメントを主導できる人)
- オペレーター(普段から設備を稼働させ、日々の癖まで分かっている人)
- 保全員(設備の不具合やチョコ停が発生した際のメンテナンス要員)
- 設計者(設備の仕様が分かり、理想は回路まで理解している人)
- 一般社員(設備を全く知らない人)
「一般社員」を入れることで、固定概念にとらわれない、新たな視点からの意見が出てくることもあるそうです。
2.コミュニケーションは「共感」から!
見落としがちな危険源や危険事象を発見するためには、円滑なコミュニケーションと、全員の意識が重要です。事前に危険源リストに目を通しておくと、会話がよりスムーズに進むかもしれません。
人は、ついつい近道をしてしまいがちなもの…。「これ、やっちゃうんですよね~」「分かります~」…そんな、”共感”の雰囲気作りも、危険事象を見逃さないための、大切なテクニックだと、ジュンイチロウさんは言っていました。日頃から、何でも言い合えるような、風通しの良い環境を整えておくことが、重要だと感じました。
3.図面やレポートは「宝物」!
日本では、国際規格に基づいたリスクアセスメントを行う習慣が、まだ十分に浸透していない…という現状があります。だからこそ、図面やレポートの重要性を、丁寧に理解していく必要があると、私は感じました。
可能であれば、見積もりの際に実機を確認する時に、全ての図面、レポート、文書を揃えておけると理想的です。これらの資料の有無によって、見積もり金額や、リスクアセスメントの実施時間が、大きく変わる可能性もあるからです。
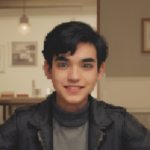
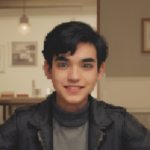
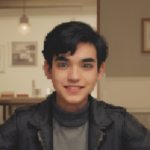
設備の文書は、会社の財産!
今回の現場で、私が最も強く感じたことです。図面やレポートは、大切に保管しましょう!
4.スケジュールは「早め」が肝心!
リスクアセスメントは、金額も時間も、実際にやってみないと分からない部分が多い…というのが、正直なところです。それは、外注業者にとっても同じこと。だからこそ、早め早めのスケジュールを組むことが、非常に重要になってきます。
特に、過密な生産スケジュールの合間を縫って、「稼働時間」と「停止時間」を確保するのは、至難の業…。この工程を必ず頭に入れて、今年度の安全対策のスケジュールを組んでいきましょう。
そして、生産に関わる部署に、リスクアセスメントの必要性と、スケジュールについて、しっかりと周知徹底することが、何よりも重要だと感じました。必ず見積もり時に、「稼働時間」と「停止時間」を提示してもらい、コストパフォーマンス良く、かつスムーズに、安全対策を実現させましょう!
最後に リスクアセスメント初日を終えて
今回のリスクアセスメント初日は、私にとって、本当に学びの多い1日でした。ジュンイチロウさんから教わった、様々な視点や進め方は、今後、どんな現場でも必ず役立つと確信しています。
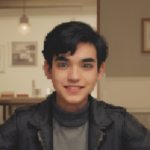
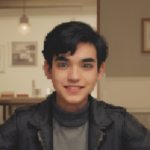
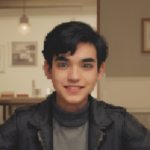
何事も”準備”が9割!
…これは、どんな仕事にも共通して言えることかもしれませんが、特にリスクアセスメントにおいては、”準備”が、本当に重要だと実感しました。もちろん、実機を見ることも大切ですが、その奥には、とてつもない危険事象が隠れている可能性があります。表面的なリスクアセスメントは、時間とお金の無駄遣いになりかねない…と、今回の経験を通して、強く感じました。
これからも、たくさんの現場を経験していく中で、今日学んだ、お客様とのコミュニケーションや、認識合わせの重要性を、常に心に留めて、頑張っていきたいと思います!
新人ならではの視点で学び続けながら、少しずつ成長していきたいと思っています!皆さんも、リスクアセスメントを行う際には、ぜひ、この記事で紹介したポイントを、参考にしてみてくださいね。
それでは、また次回!ガンタでした!