
ISO12100リスクアセスメントって何?機械の安全化に必要なリスクアセスメントの理由を初心者向けに解説
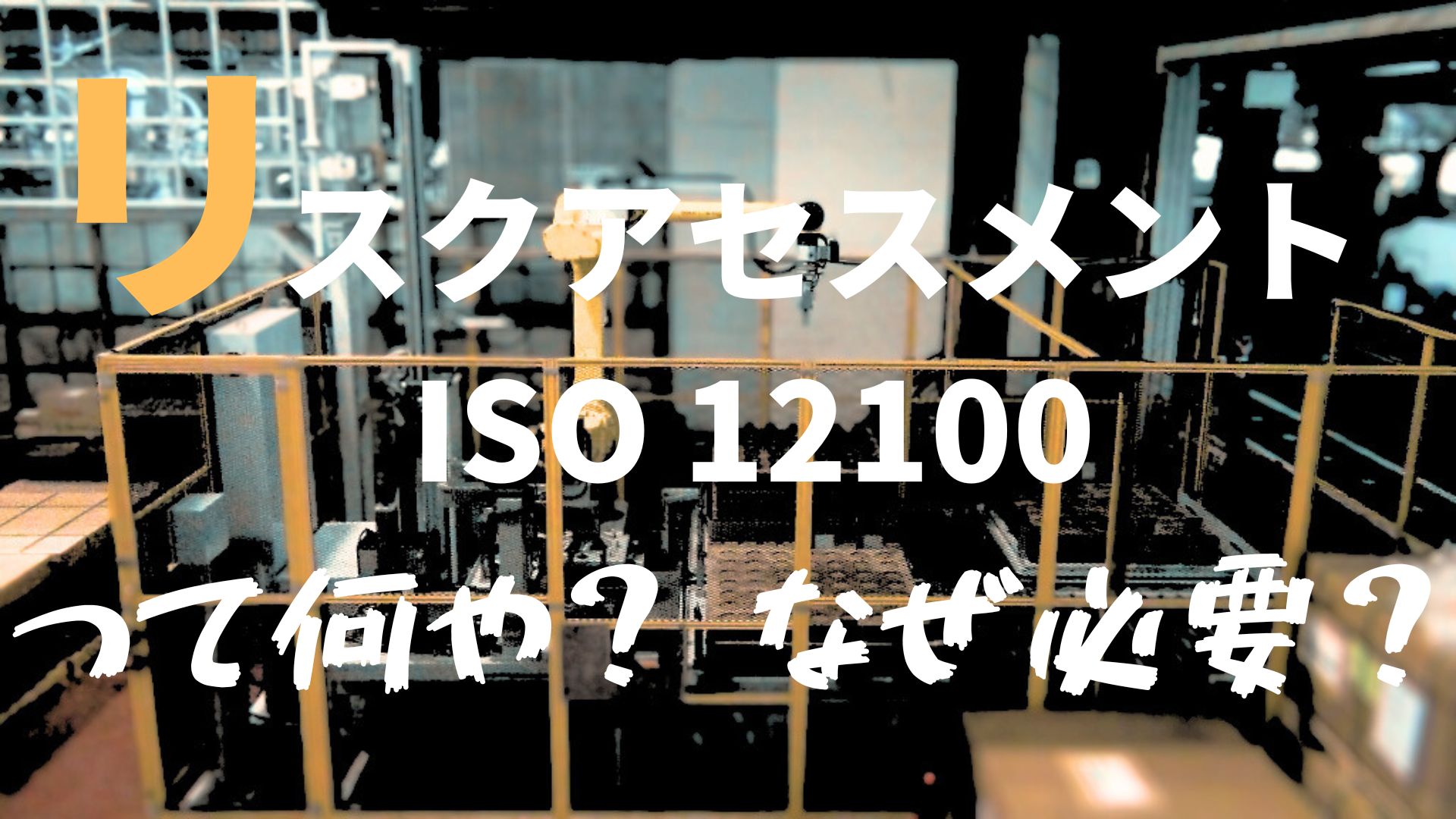
あらすじ
こんにちは!今回は、機械の安全性に関する国際規格であるISO12100 について、リスクアセスメントの方法をわかりやすく説明してみたいと思います。
リスクアセスメントとは、機械に付随する危険源や危険状態を見つけ出し、それらが引き起こす危害の確率とひどさを評価し、許容可能なレベルまでリスクを低減するためのプロセスです。ISO12100 では、リスクアセスメントを以下の5つの手順で行うことを推奨しています。
- 機械類の制限の決定
- 危険源の同定
- リスク見積り
- リスク評価
- リスク低減
機械の安全化にリスクアセスメントが必要な理由は、以下のとおりです。
- 機械の使用者や周囲の人々の生命や健康を守るため
- 機械の故障や事故による経済的な損失や信頼性の低下を防ぐため
- 機械の法的な適合性や市場へのアクセスを確保するため
- 機械の性能や効率を向上させるため
ISO12100 リスクアセスメントは、機械の安全性を確保するために欠かせない活動です。
目次
ISO 12100 とは何ですか?
- ISO 12100:2010
-
Safety of machinery – General principles for design – Risk assessment and risk reduction
- JIS B 9700:2013
-
機械類の安全性−設計のための一般原則−リスクアセスメント及びリスク低減
ISO 12100 とは題名を「Safety of machinery – General principles for design – Risk assessment and risk reduction」といい、JIS 規格ではJIS B 9700:2013「機械類の安全性−設計のための一般原則−リスクアセスメント及びリスク低減」が整合しています。
ISO 12100 では、機械の安全性に関する基本的な概念と設計原則を定めています。この規格は、機械のリスク評価とリスク低減のプロセスを説明し、安全な機械を設計するための一般的なガイドラインを提供しています。ISO 12100 は、以下のポイントを含んでいます。
- 機械の安全性に関する用語と定義
- 機械のライフサイクルにおける安全性の要素
- 機械の危険性とリスクの特定、推定、評価
- リスク低減の階層的なアプローチ(安全な設計、保護装置、情報供与)
- 安全な機械の技術的要求事項
- 安全な機械の適合性評価と宣言
ISO 12100 では、機械の安全性に関する基本的な概念と設計原則を定めています。この規格は、機械のリスク評価とリスク低減のプロセスを説明し、安全な機械を設計するための一般的なガイドラインを提供しています。ISO 12100 は、以下のポイントを含んでいます。
- 機械の安全性に関する用語と定義
- 機械のライフサイクルにおける安全性の要素
- 機械の危険性とリスクの特定、推定、評価
- リスク低減の階層的なアプローチ(安全な設計、保護装置、情報供与)
- 安全な機械の技術的要求事項
- 安全な機械の適合性評価と宣言
ISO 12100 は機械の安全性に関する包括的な規格であり、他の特定の機種や産業に関する規格と一緒に適用されることが想定されています。
安全なぜ必要?
安全の定義は ISO/IEC GUIDE51:2014 または JIS Z 8051:2015 という規格で定義されています。下記、記事も参考してください。
Safety: Freedom from risk which is not tolerable (ISO/IEC GUIDE51:2014)
安全とは: 許容不可能なリスクがないこと (JIS Z 8051:2015)
ISO12100.com

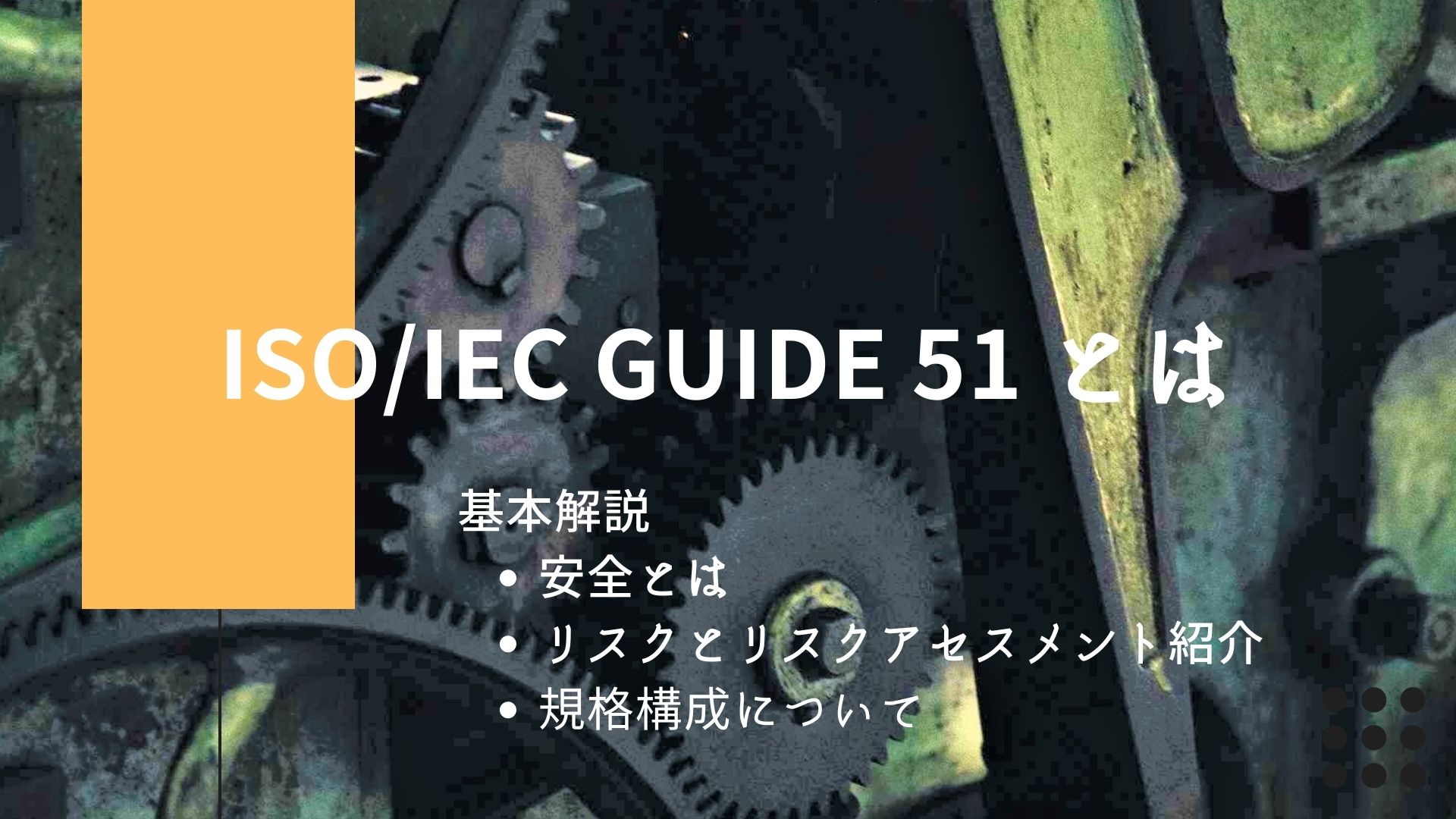
ISO/IEC GUIDE 51安全の定義「安全とは許容不可能なリスクがないこと」とリスクゼロはありえない
こんにちは! 今日はISO/IEC GUIDE 51という国際規格についてお話ししたいと思います。 ISO/IEC GUIDE 51は、製品やシステムの安全性に関する国際的なガイドラインです。こ…
世界人権宣言
ISO 12100 は、機械安全の基本概念規格として、機械を設計する際に行うべきリスクアセスメントとリスク低減の方法論を提供しています。この規格は、世界人権宣言の精神に基づいて、すべての人が安全で健康的な労働環境を享受する権利を尊重しています。世界人権宣言は、1948 年に国連総会で採択された普遍的な人権文書であり、その第23 条では、下記のとおり明記されています。
すべて人は、勤労し、職業を自由に選択し、公正かつ有利な勤労条件を確保し、及び失業に対する保護を受ける権利を有する
世界人権宣言(仮訳文)
ISO 12100 は、このような人権の保護に貢献することを目的としており、機械の設計者に対して、危険源の除去や低減、安全防護や付加保護方策の適用、使用上の情報の提供などのリスク低減の手順を示しています。ISO 12100 は、機械安全に関する他の規格(B 規格やC 規格)とも整合性を持っており、国際的な水準に適合した安全な機械を設計するための基礎となる規格です。
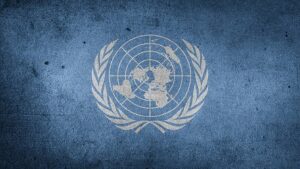
機械安全の大前提
機械安全の大前提
- 人はミスをする
- 機械は故障する
- 絶対安全は存在しない
機械安全の大前提として、人はミスをする、機械は故障する、絶対安全は存在しないということを忘れてはなりません。これらの事実を認めることで、機械の設計や運用において、安全性を高めるための工夫や対策を考えることができます。
例えば、人はミスをするということを前提にして、人が操作する機械にはエラー防止やエラー回復の機能を備えることが望ましいです。また、人が操作する際には、わかりやすいインターフェースやフィードバックを提供することで、人の認知負荷やストレスを軽減することができます。
一方、機械は故障するということを前提にして、故障時にも安全性を確保するための仕組みを設けることが重要です。例えば、冗長性や自己診断・自己修復の機能を持たせることで、故障した部分を切り離したり、代替したり、修復したりすることができます。また、故障時には、人に適切な警告や指示を与えることで、人が迅速かつ正確に対処することができます。
最後に、絶対安全は存在しないということを前提にして、万が一の事故・災害に備えることが必要です。例えば、事前にリスク分析やシミュレーションを行うことで、発生確率や影響度を評価し、予防策や緊急対応策を立てることができます。また、事後には事故・災害の原因や経過を分析し、教訓や改善策を導き出すことができます。
以上のように、機械安全の大前提を踏まえて、人も機械も安全に働けるようにすることが目的です。人と機械の協働や相互補完が可能な環境を作ることで、生産性や品質も向上することが期待できます。
日本における機械安全
日本の産業現場は伝統的に「労働安全」が重視され、「機械の安全化」は重視されにくい状況が続いています。しかし、このような考え方は時代遅れであると言わざるを得ません。なぜなら、「人に頼る安全」の思想からの転換が必要だからです。「人に頼る安全」とは、人間の判断や行動によって安全を確保しようとする考え方です。
例えば、機械に危険な部分があっても、人間が気を付けて操作すれば問題ないという考え方です。しかし、このような考え方は、人間のミスや不注意を完全に排除することはできないという事実を無視しています。人間は完璧ではないのだから、どんなに注意してもミスや不注意は起こります。
もし、災害が発生すると、人が受ける苦痛の計り知れないコストが発生する。人命や健康を失うだけでなく、裁判、起訴、その他の法的活動の脅威にさらされる可能性もある。また、将来におけるビジネスの潜在的喪失も考えられます。顧客や社会からの信頼を失い、競争力や収益性を低下させることになるかもしれません。
そこで、「機械の安全化」が重要になってきます。「機械の安全化」とは、機械自体に安全性を高める仕組みや装置を取り付けたり、危険な部分を隔離したりすることです。例えば、保護インターロックや警告音や表示器などが該当します。これらの仕組みや装置は、人間のミスや不注意を防ぐことができます。また、万一災害が発生しても、被害を最小限に抑えることができます。
「機械の安全化」は、「労働安全」よりもコストがかかると思われがちです。しかし、長期的に見れば、「機械の安全化」は「労働安全」よりもコストパフォーマンスが高いと言えるかもしれません。なぜなら、「機械の安全化」は一度行えば継続的に効果があるからです。さらに「労働安全」は常に教育や監督が必要であり、それらにもコストがかかるります。
日本の産業現場は、「人に頼る安全」から「機械に頼る安全」へと思想を転換する必要があるかもしれません。災害が発生すると、人が受ける苦痛の計り知れないコストだけでなく、裁判、起訴、その他の法的活動の脅威や、将来におけるビジネスの潜在的喪失というリスクも増大します。産業現場では、「機械の安全化」を積極的に推進し、人間と機械の相互作用を最適化することが必要です。これには、機械やシステムの安全性や信頼性を高める技術的な対策だけでなく、人間の行動や心理を考慮した人間工学的な対策も含まれます。また、安全文化や安全教育を徹底し、安全意識や安全行動を従業員に浸透させることも重要です。こうした取り組みにより、「人に頼る安全」から「人と機械が協働する安全」へと転換することができるかもしれません。
ブラック企業リスト
平成29 年1 月20 日付け基発0120 第1 号「違法な長時間労働や過労死等が複数の事業場で認められた企業の経営トップに対する都道府県労働局長等による指導の実施及び企業名の公表について」に基づき、局長が企業の経営トップに対し指導し、その旨を公表した事案があります。
違法な長時間労働や過労死等が複数の事業場で発生していることは、社会的にも個人的にも深刻な問題です。厚生労働省は、この問題に対処するために、平成29年1月20日付けで新たな通達を発出しました。この通達では、違法な長時間労働等を複数の事業場で行うなどの企業に対して、都道府県労働局長又は労働基準監督署長が経営幹部や経営トップに対して指導を行い、その事実を企業名とともに公表することとしています。この制度は、経営トップが自ら率先して全社的な是正・改善に取り組むことを促すとともに、他の企業における遵法意識を啓発し、法令違反の防止や自主的な改善を促進させることを目的としています。
この制度に基づき、厚生労働省はこれまでにたくさんの事案を公表しています。これらの事案は、「厚生労働省長時間労働削減に向けた取組 労働基準関係法令違反に係る公表事案」で検索することができます。このサイトでは、公表された企業名や違反内容、指導内容や取組方針などの詳細情報を閲覧することができます。また、ハローワークでは、一定の労働関係法令違反があった事業所を新卒者などに紹介することのないよう、こうした事業所の新卒求人を一定期間受け付けません。
厚生労働省は、この制度を通じて、違法な長時間労働や過労死等が複数の事業場で認められた企業に対する指導・公表を継続的に行っていくとともに、全国的な監督指導体制の強化や啓発活動の充実などを通じて、長時間労働の是正及び過重労働による健康障害防止対策を推進していきます。
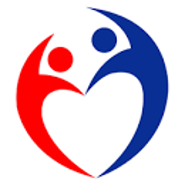
労働安全衛生法との関係
平成19 年に厚生労働省が「(改正)機械の包括的な安全基準に関する指針」を公表し、機械の安全化を図ってきました。この指針は、機械の設計・製造・販売・使用に関わる者に対して、機械の危険性を評価し、適切な安全対策を講じることを促すものです。指針には、機械の危険性評価の方法や安全対策の選択基準、安全表示や取扱説明書の作成などについて具体的な事例や参考資料が示されています。
さらに、労働安全衛生法の一部改正により、事業者に対し設備等の危険性又は有害性を調査し、その結果に基づく措置の実施が義務化されました。これは、事業者が自ら設備等の危険性又は有害性を把握し、必要な安全管理を行うことを目的としたものです。調査は、設備等の種類や使用状況に応じて適宜行うことが求められます。措置は、危険性又は有害性を除去することが最優先であり、それが困難な場合は、危険部位を遮断したり、警告表示や保護具の使用を求めたりすることが必要です。
機械類の安全性に関する国際規格が制定されたことを踏まえ、危険又は健康障害の防止措置等を講ずることを求め (法第28条の2)、平成18 年4 月1 日より施行されることになりました。この規定は、国際規格に準拠した機械類の導入や使用を促進することで、国際的な競争力の向上や事故防止に寄与することを目的としたものです。国際規格に準拠した機械類は、「CE マーキング」などの表示がされています。これらの表示は、機械類が安全性に関する基本要件を満たしていることを示すものです。
労働安全衛生規則24 条の13 では機械危険情報の通知を努力義務化しました。これは、機械の設計・製造・販売に関わる者が、自ら発見したり、他から知ったりした機械の危険性について、使用者や関係者に速やかに通知することを義務づけたものです。通知することで、事故の防止や被害の軽減につながります。
以上のように、平成19 年以降、機械の安全化に向けてさまざまな取り組みが行われてきました。しかし、依然として機械による事故は発生しており、注意が必要です。機械の安全化は、設計・製造・販売・使用に関わるすべての者が協力して実現するものです。
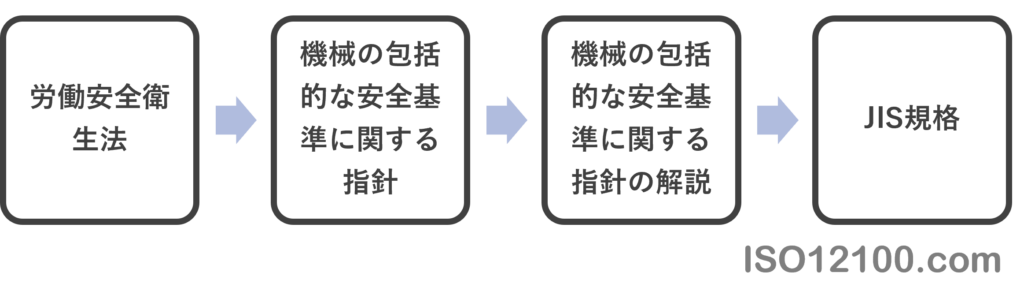
企業の責任
労働災害とは業務上または通勤中に従業員が負傷や病気にかかることをいいます。労働災害が発生した場合、企業は以下の3種類の責任を負う可能性があります。
企業の責任
- 行政責任
- 刑事責任
- 民事責任と労災補償
行政責任
行政責任とは、労働安全衛生法や労働基準法などの法令に違反した場合に、労働基準監督署から是正勧告や改善指導、機械設備の使用停止や作業停止などの行政処分を受けることです。また、重大な法令違反があった場合には、書類送検されて刑事罰を受けることもあります。
労働災害が発生した場合、事業主や従業員には様々な責任が発生します。その中でも、行政責任は労働安全衛生法に基づくもので、労働基準監督署が行う臨時の検査や監督によって判断されます。労働災害の原因や状況によっては、労働安全衛生法に違反したとみなされ、是正勧告や是正命令、罰金や懲役などの行政処分を受ける可能性があります。行政責任は事業主だけでなく、従業員や安全衛生委員会などにも及ぶ場合があります。したがって、労働災害を防止するためには、事業主や従業員は労働安全衛生法を遵守し、安全衛生管理を徹底する必要があります。
刑事責任
労働災害が発生した場合、事業主や管理者は、労働安全衛生法や刑法などの法律に違反していた場合、刑事責任が問われることがあります。例えば、労働安全衛生法では、事業主は安全衛生管理責任を負い、必要な安全措置や教育を行わなければなりません。また、刑法では、業務上過失致死傷罪や業務上過失致死罪などの罪があります。刑事責任が問われる場合、捜査機関による捜査取り調べ→起訴→刑事裁判の流れになります。
労働安全衛生法に違反することについて。この法律は、労働者の安全や健康を保護するために、事業者や労働者にさまざまな義務を課しています。例えば、危険な作業を行う場合には、事前に教育や指導を行ったり、安全装置や保護具を設置したりしなければなりません。安衛法違反がある場合には、ほぼ過失が認められて業務上過失致傷罪が成立します。
労働安全衛生法に違反が無い場合でも、過失が認められれば業務上過失致死傷罪が成立します。例えば、安衛法には定められていないが一般的に危険と知られている作業を行った場合や、安衛法には定められているが不十分な措置しか取らなかった場合などです。このような場合には、行為者の注意義務違反が問われます。
民事責任と労災補償
民事責任とは、労働災害によって被災者やその遺族が受けた損害を賠償することです。民事責任は、不法行為や債務不履行(安全配慮義務違反)などの事由によって被災者等から事業主に対して民法上の損害賠償請求がなされる場合に発生します。しかし、事業主が労災保険に加入している場合は、労災保険から給付が行われることで、労働基準法上の補償責任を免れます。ただし、休業1~3日目の休業補償は労災保険から給付されないため、事業主が直接労働者に支払う必要があります。また、民法上の損害賠償請求があった場合には、労災保険から給付された価額分は免れますが、それ以上の部分は賠償する必要があります。
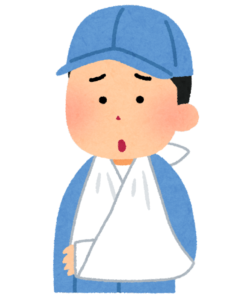
リスクアセスメントはなぜ必要?
EU でのリスクアセスメント
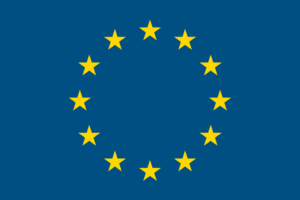
EU 機械指令2006/42/EC は、機械の安全性と品質を確保するための法的な枠組みを提供しています。この指令により、機械製造業者または正当な代理人は、その機械に適用される必須健康安全要求事項を決定するために、リスクアセスメントが確実に実施されるようにしなければなりません。その場合、リスクアセスメントの結果を考慮して機械を設計および構築する必要があります。
ISO12100.com

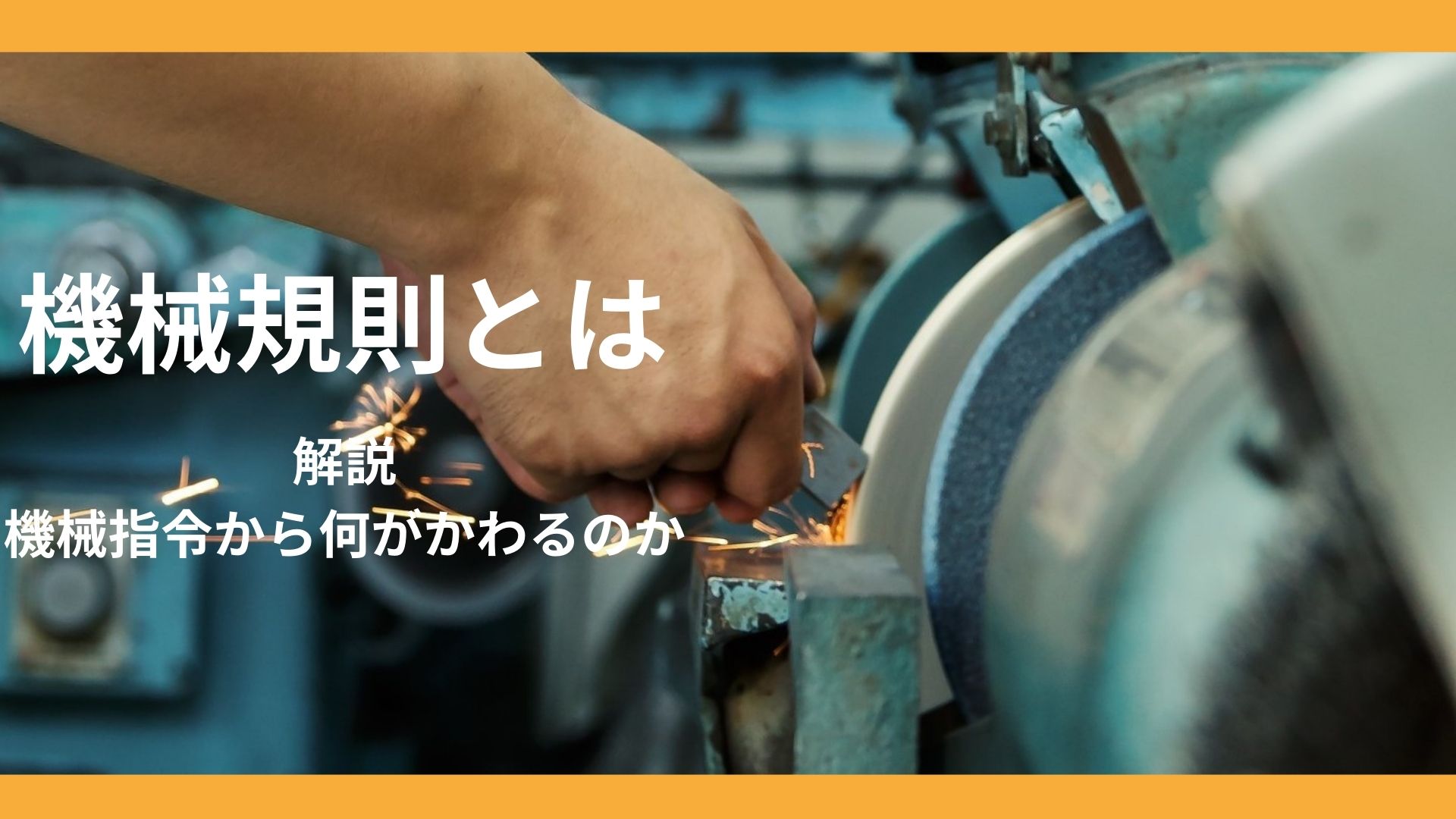
機械規則(Machinery Regulation)と機械指令(Machinery Directive)との違い。機械規則発行30ヶ月後で困らな…
こんにちは! 今日はISO/IEC GUIDE 51という国際規格についてお話ししたいと思います。 ISO/IEC GUIDE 51は、製品やシステムの安全性に関する国際的なガイドラインです。こ…
EU 委員会が指令の発行を行います。これは、EU 加盟国で職業上の健康、安全、福祉に関する最低基準を定めるものです。指令は、目的と結果を示すだけで、具体的な方法は示しません。そのため、各国は自国の状況に合わせて指令を実施することができます。
承認された認定機関 (CEN, CENELEC) がEU(EN) 規格を発行します。これは、指令に基づいて製品やサービスの品質や安全性を保証するための技術的な基準です。EU(EN) 規格は、業界や消費者団体などの関係者の合意によって作られます。EU(EN) 規格は、自主的に適用することができますが、指令に準拠することを証明するために有用です。
欧州各国は職業上の健康、安全、福祉を守るための政府機関を持ちます。これらの機関は、指令やEU(EN) 規格に関する情報や助言を提供し、職場での事故や病気の予防や対策を支援します。また、職場での検査や監督も行います。
各国政府がこれらの指令を国内法令に置き換え、各国の実施官庁は法令を施行し、ガイダンス文書を発行します。これは、指令が法的な効力を持つために必要なプロセスです。各国は、指令に従って法令を作成し、職場での健康や安全に関する義務や権利を明確にします。ガイダンス文書は、法令を理解し遵守するための参考資料です。
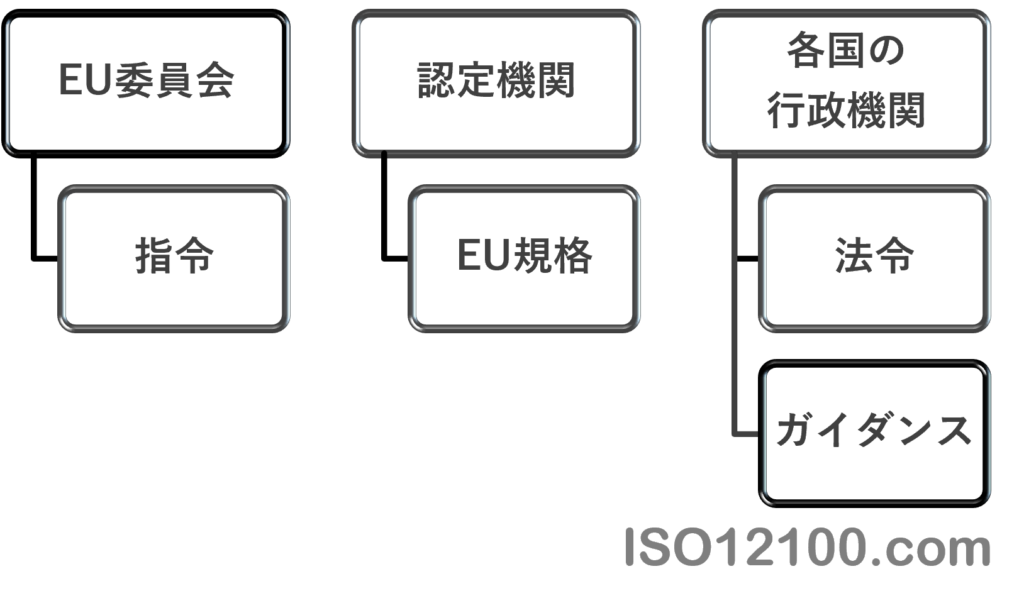
機械指令 2006/42/EC リスクアセスメントの要求
機械指令 2006/42/EC は、EU の市場に導入するために機械が遵守しなければならない安全上の要求事項を規定したEU法です。この指令は、機械の安全性を高めるとともに、EU 内での自由な貿易を促進することを目的としています。機械指令に従って設計および製造された機械は、CE マーキングを付けることができます。CE マーキングは、機械が指令の要求事項に準拠していることを示しています。
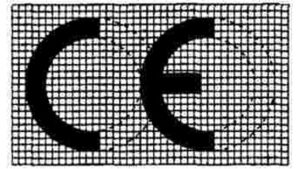
機械指令の付属書I には、指令の対象となるすべての機械に適用される必須健康安全要求事項が含まれており、次のように述べています。
「機械製造業者やその正当な代理人は、その機械に適用される必須健康安全要求事項を決定するために、確実にリスクアセスメントを実施しなければならない。またリスクアセスメントの結果を考慮して機械を設計および製造する必要がある」
北米でのリスクアセスメント
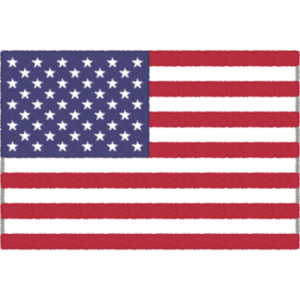
アメリカでは、1970 年に労働安全衛生法(Occupational Safety and Health Act of 1970) が制定されました。この法律は、世界で初めての総合的な労働安全衛生立法であり、雇用者に従業員の安全と健康を保障する義務を課しました。この法律に基づいて、労働省に労働安全衛生局(OSHA) と保健福祉省に労働安全衛生研究所(NIOSH) が設置され、労働安全衛生の基準の策定、執行、研究、教育などの活動を行っています。
この法律の第5 条には、「雇用者は、自分の従業員に死亡または重大な身体的危害を引き起こしている、または引き起こしそうな、認識されている危険から解放された雇用の場所を提供する」という規定があります。これは、一般的な義務条項と呼ばれ、雇用者は、この法律で公布された基準だけでなく、その他の危険に対しても適切な対策を講じる必要があります。この条項に違反した雇用者には、罰金や刑事罰が科せられる可能性があります。
アメリカでは労働安全衛生は、アメリカ労働省の連邦機関のひとつである労働安全衛生管理局 (OSHA: Occupational Safety and Health Administration) よって規制されています。OSHA は1970 年に法制化された労働安全衛生法に基づき設立されました。この法律は、労働者の安全と健康を保護するために、雇用主に対して様々な基準や規則を定めています。例えば、危険な物質や機械からの防護、救急処置や訓練の提供、事故や病気の報告などです。OSHA はこれらの基準や規則を監督し、違反した場合には罰金や差し止め命令などの措置をとることができます。
OSHA の姉妹機関として、アメリカ厚生省の疾病管理予防センターの下部組織のひとつである国立労働安全衛生研究所(NIOSH: National Institute of Occupational Safety and Health) が設立されました。NIOSH は研究を主体とした連邦機関であり、OSHA は法律の施行を主体とした規制連邦機関です。NIOSH は労働安全衛生に関する科学的な知識や情報を提供し、新しい技術や方法を開発し、推奨事項やガイドラインを作成します。NIOSH はまた、労働者の健康状態や職業災害の原因を調査し、予防策や対策を提案します。NIOSH はOSHA と協力して、労働安全衛生の改善に貢献しています。
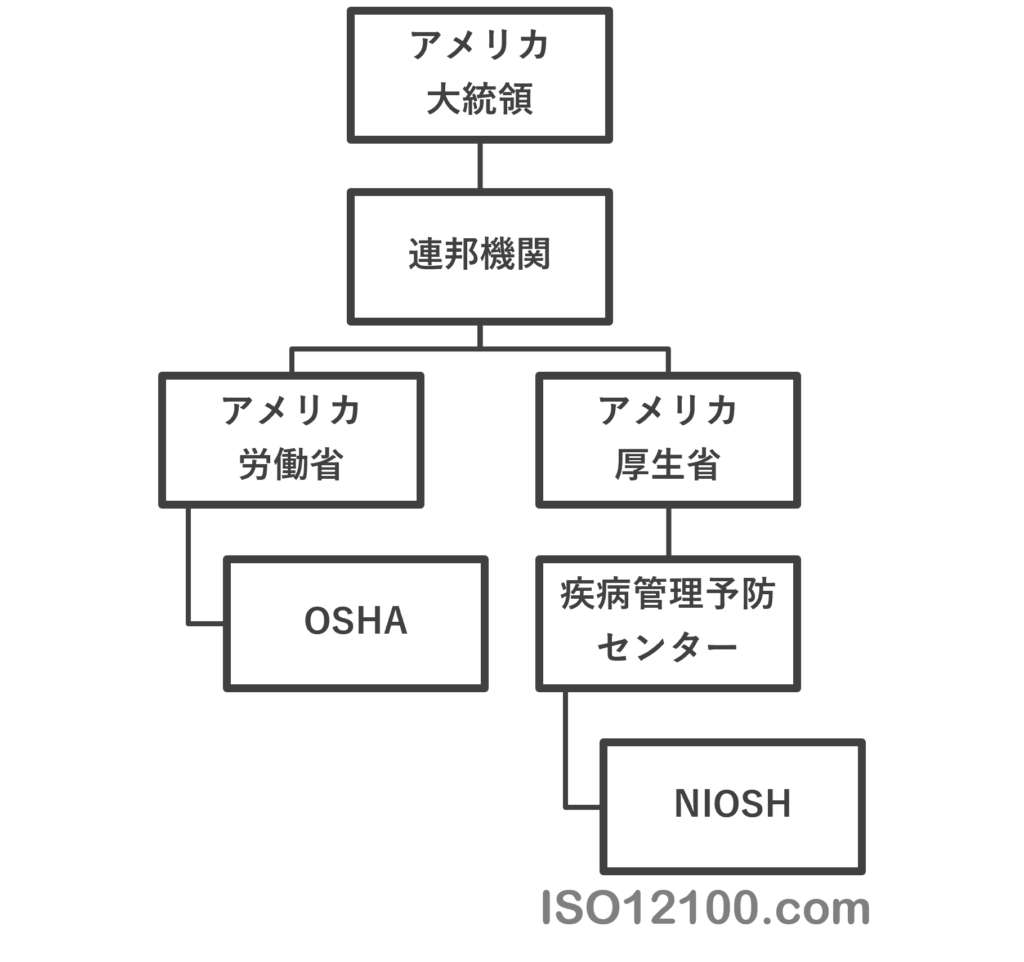
OSHA は、労働安全衛生法のあらゆる側面を管理する機関です。労働安全衛生法は、労働者の安全と健康を守るために、化学物質や機械などの危険性や有害性を評価し、適切な対策を講じることを義務付けています。この評価は、リスクアセスメントと呼ばれます。
リスクアセスメントとは、危険性や有害性の程度と発生する可能性を分析し、リスクのレベルを判断することです。リスクのレベルに応じて、必要な措置を計画し、実施し、効果を確認することも含まれます。リスクアセスメントは、事業者が自主的に行うものであり、労働局はその方法や結果について指導や監督を行います。
労働安全衛生法では、化学物質等による危険性又は有害性等の調査等に関する指針を定めており、これに基づいてリスクアセスメントを行うことが求められます。指針では、化学物質等の表示や安全データシート(SDS) などの情報源を活用することや、作業場の状況や労働者の特性を考慮することなどが示されています。
また、労働安全衛生規則では 29 CFR Part 1910 について言及しています。29 CFR Part 1910 は、アメリカ合衆国の連邦規則集であり、一般産業における労働安全衛生基準を定めています。この規則集は、化学物質等の危険性又は有害性等の調査等に関する指針の参考資料として挙げられており、リスクアセスメントに役立つ情報が含まれています。
日本でのリスクアセスメント
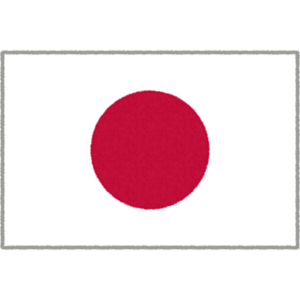
我が国日本では、平成19 年に厚生労働省が「(改正)機械の包括的な安全基準に関する指針」を公表してまいす。この指針では、機械の設計及び製造等を行う製造者等並びに当該機械を労働者に使用させる事業者に適用するもので、機械の安全性を確保するための基準や手順を示しています。指針は、EU 機械指令と整合性を持たせることで、国際的な安全水準に適合するとともに、国際市場への参入を容易にすることを目的としています。
公表されたのは、以下の理由があります。
欧州では、1989 年にEU 機械指令が公布され、機械の流通に際して安全要求事項に適合することが求められるようになりました。この安全要求事項は、EU 規格(EN 規格)に具体的に定められており、リスクアセスメントを含む機械安全の基本原則や方法論が示されています。日本国内でも、これらのEU 規格を参考にしたJIS 規格が発行されています。
日本では、労働安全衛生法に基づいて、機械を使用する事業者は危険性や有害性等の調査等を行い、必要な措置を講じることが義務付けられています。また、機械を設計・製造・輸入する者は、労働災害の防止に資するよう努めることが求められています。しかし、これらの法令は具体的な方法や基準を示していないため、実務上の判断や対応に困難が生じる場合がありました。
そこで、厚生労働省は、2001 年に「機械の包括的な安全基準に関する指針」を策定しました。これは、すべての機械に適用できる包括的な安全確保の方策に関する基準として定められたもので、リスクアセスメントを含む機械の安全化の手順や実施事項を示しています。しかし、この指針は2000 年に発行されたISO12100(国際規格)を参考にしたものであり、その後ISO12100 が改正されたことや新たな安全衛生に係る知見が集積されたことから、2007 年に「(改正)機械の包括的な安全基準に関する指針」が公表されました。「(改正)指針」では、「指針」よりも詳細かつ具体的な内容や例示が追加されています。
JIS 規格との関係
日本工業規格(JIS 規格) とは、日本の産業分野で使用される製品やサービスに関する規格のことです。JIS 規格は、国際標準化機構(ISO) や国際電気標準会議(IEC) などの国際規格との整合性を図りながら、日本の技術水準や社会的要求に応えるように策定されます。JIS 規格は、WTO/TBT 協定に基づいて、強制規格と任意規格に分けられます。WTO/TBT 協定は、工業製品などの規格や適合性評価手続きが不必要な貿易障害とならないようにするための国際協定です。この協定は、強制規格と任意規格について、国際規格を基礎として用いることや透明性を確保することなどを義務づけています。JIS 規格は、日本の任意規格であり、TBT 協定の適正実施規準に従って策定されています。
WTO (世界貿易機関)協定の一部を構成する「TBT 協定(貿易の技術的障害に関する協定)」は、途上国を含むすべてのWTO 加盟国に関し、以下の義務を課している
① 貿易相手国によって差別的に国内規格を適用してはならない
(A 国からの輸入品にはa 規格、B 国からの輸入品にはb 規格といった適用はできない。)
② 国内規格は、国家安全保障上の必要性など正当な理由が無い限り、国際貿易上の不必要な障害をもたらす目的で作られてはならない
③ 国内規格は、気候上の理由など正当な理由が無い限り、国際規格を基礎として作成しなければならないこのように、TBT 協定は、各国の規制等で用いられる強制規格や任意規格を国際規格に整合化していくことで、規格による不必要な国際貿易上の障害を排除し、公正で円滑な国際貿易の実現を目的としている
経済産業省
強制規格とは、法律や条例で遵守が義務付けられた規格で、人命や安全、環境などに関わるものです。任意規格とは、自主的に適用することができる規格で、品質や性能、互換性などに関わるものです。JIS 規格に適合した製品やサービスは、適合性評価手続を経て、JIS マークを表示することができます。JIS マークは、消費者や利用者に対して、信頼性や安全性を示すものです。JIS 規格は、国際規格との整合化を図ることで、日本の産業の国際競争力を高めるとともに、貿易の技術的障害を低減することに貢献しています 。
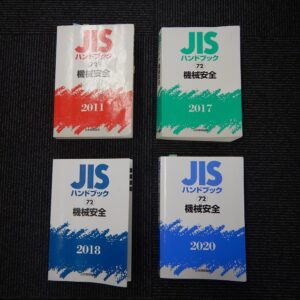
リンク
リスクアセスメント
リスクアセスメントの概要
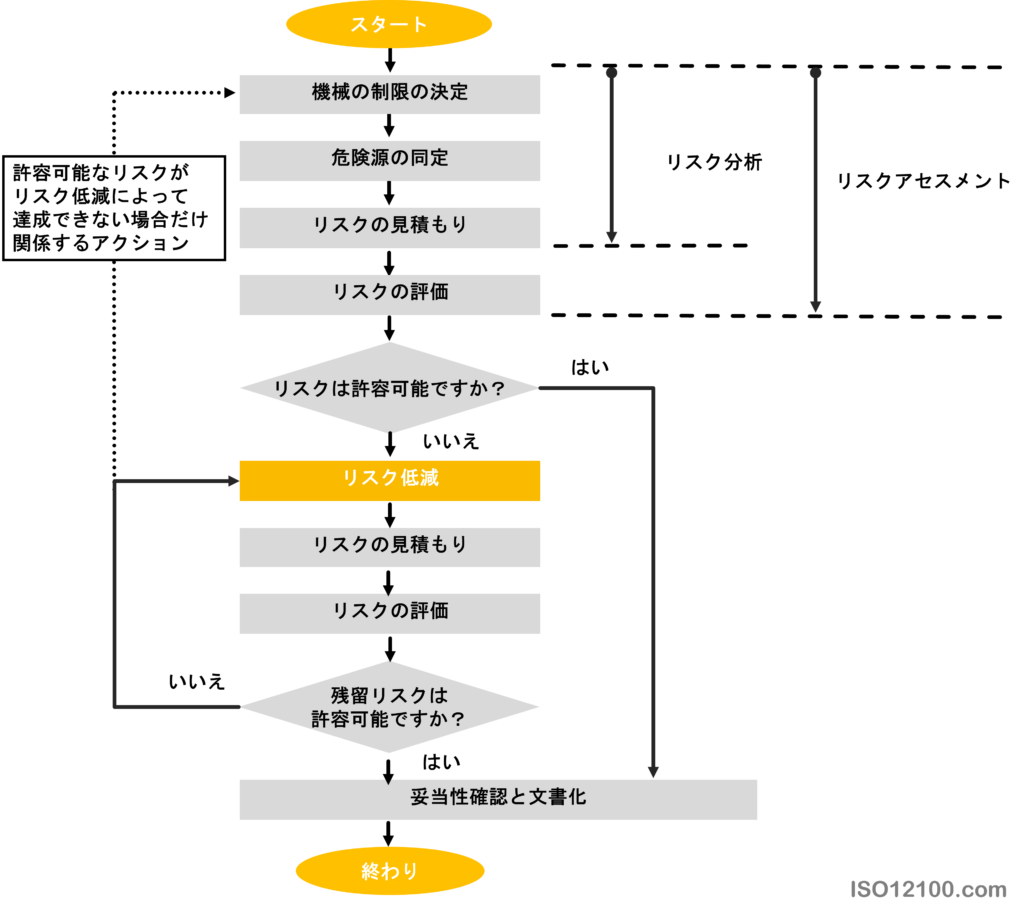
定義
ISO 12100 リスクアセスメントを学ぶ上で重要な定義を記します。
- 機械類 機械(machinery, machine)
-
連結された部品又はコンポーネントで構成される駆動部分を備え、または備えることを意図したものであって、構成要素である連結部品又はコンポーネントのうち、少なくとも一つは、特定の目的のために稼働し、かつ、協働するもの。
- 危害 (harm)
-
身体的傷害または健康障害
- 危険源(hazard)
-
危害を引き起こす潜在的根源
- リスク(risk)
-
危害の発生確率と危害のひどさとの組合せ
- リスク見積り(risk estimation)
-
起こり得る危害のひどさ及びその発生確率を明確にすること
- リスク分析(risk analysis)
-
機械の制限に関する仕様、危険源の同定およびリスク見積りの組合せ
- リスク評価(risk evaluation)
-
リスク分析に基づき、リスク低減目標を達成したかどうかを判断すること
- リスクアセスメント(risk assessment)
-
リスク分析およびリスク評価を含む全てのプロセス
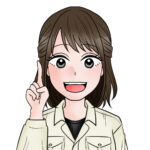
このブログでは「hazard」 を「危険源」、「risk」を「リスク」として呼んでいます。日本語では「hazard」も「risk」も「危険」となり、ややこしいのであえて区別しています。
リスクアセスメントとは、機械に付随する危険源や危険状態を見つけ出し、それらが引き起こす危害の確率とひどさを評価し、許容可能なレベルまでリスクを低減するためのプロセスです。ISO 12100 では、リスクアセスメントを以下の5つの手順で行うことを推奨しています。
- 機械の境界と使用条件を定義する。機械の範囲、目的、機能、性能、寿命などを明確にする。
- 危険源や危険状態を特定する。機械の各部分や動作において、人や物に危害を及ぼす可能性のある要因や状況を洗い出す。
- リスクの評価を行う。危険源や危険状態から発生する危害の種類、程度、頻度などを考慮し、リスクの大きさを定量的または定性的に判断する。
- リスクの低減策を決定する。リスクが許容可能なレベルに達していない場合は、リスク低減の原則に従って、安全設計や保護装置、警告表示などの対策を講じる。
- リスクアセスメントの結果と効果を文書化する。リスクアセスメントの過程と結果を記録し、リスク低減策が適切に実施されたことを確認し、必要に応じて見直しや改善を行う。
リスクアセスメント
ISO 12100 リスクアセスメントでは「リスク分析およびリスク評価を含む全てのプロセス」と定義されています。具体的には下記の流れになっています。
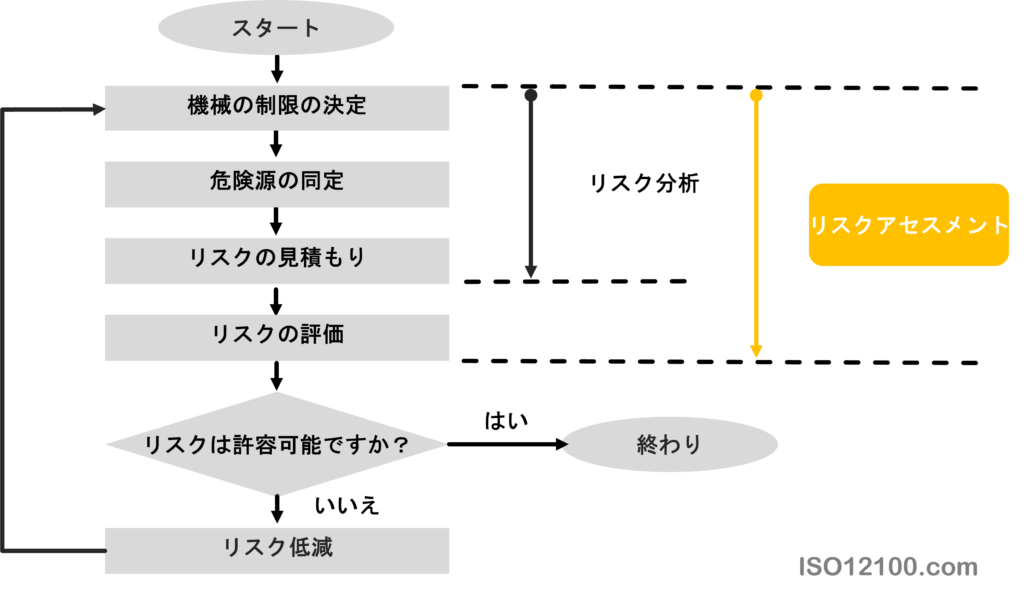
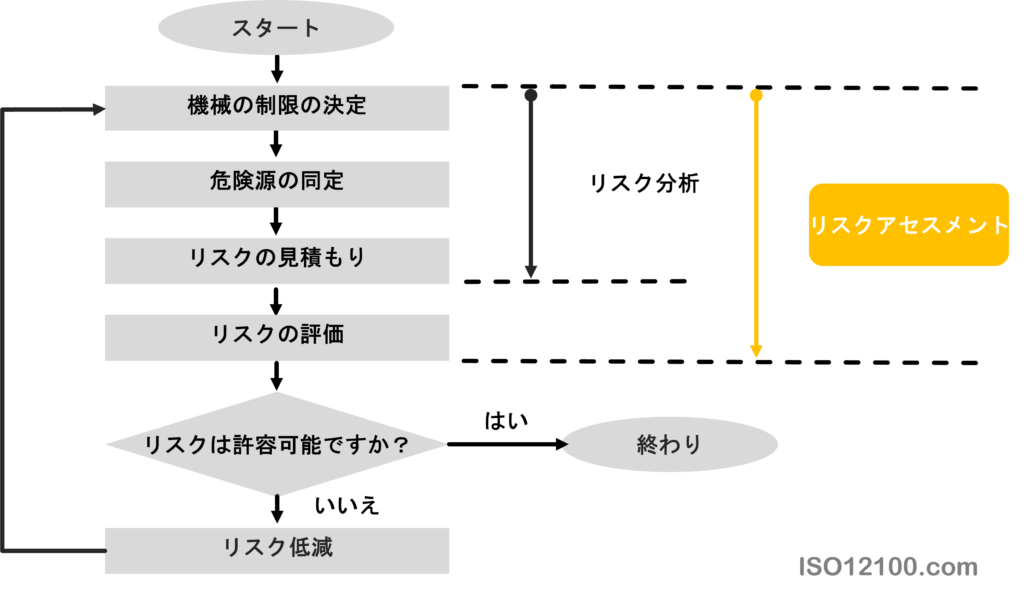
機械安全コンサルティングサービス | インテリスク株式会社

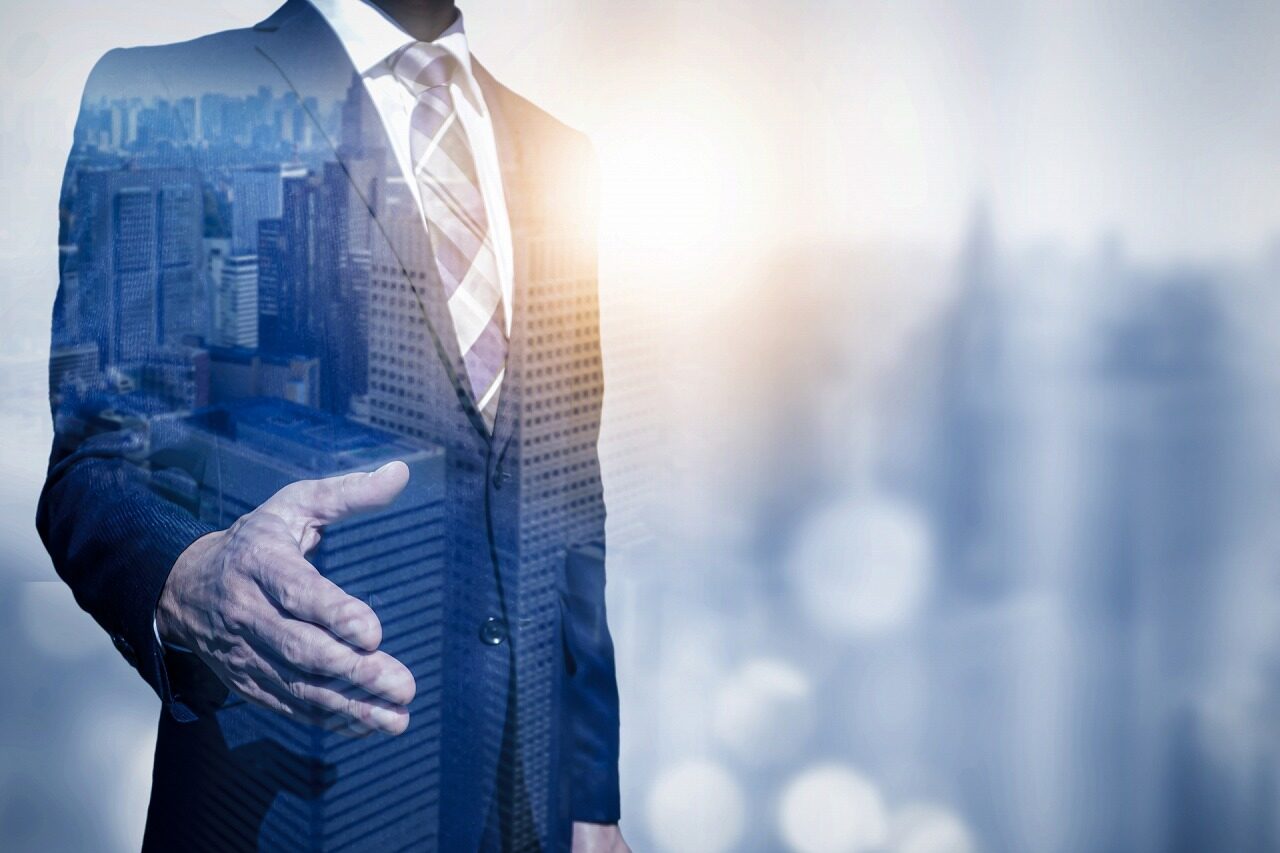
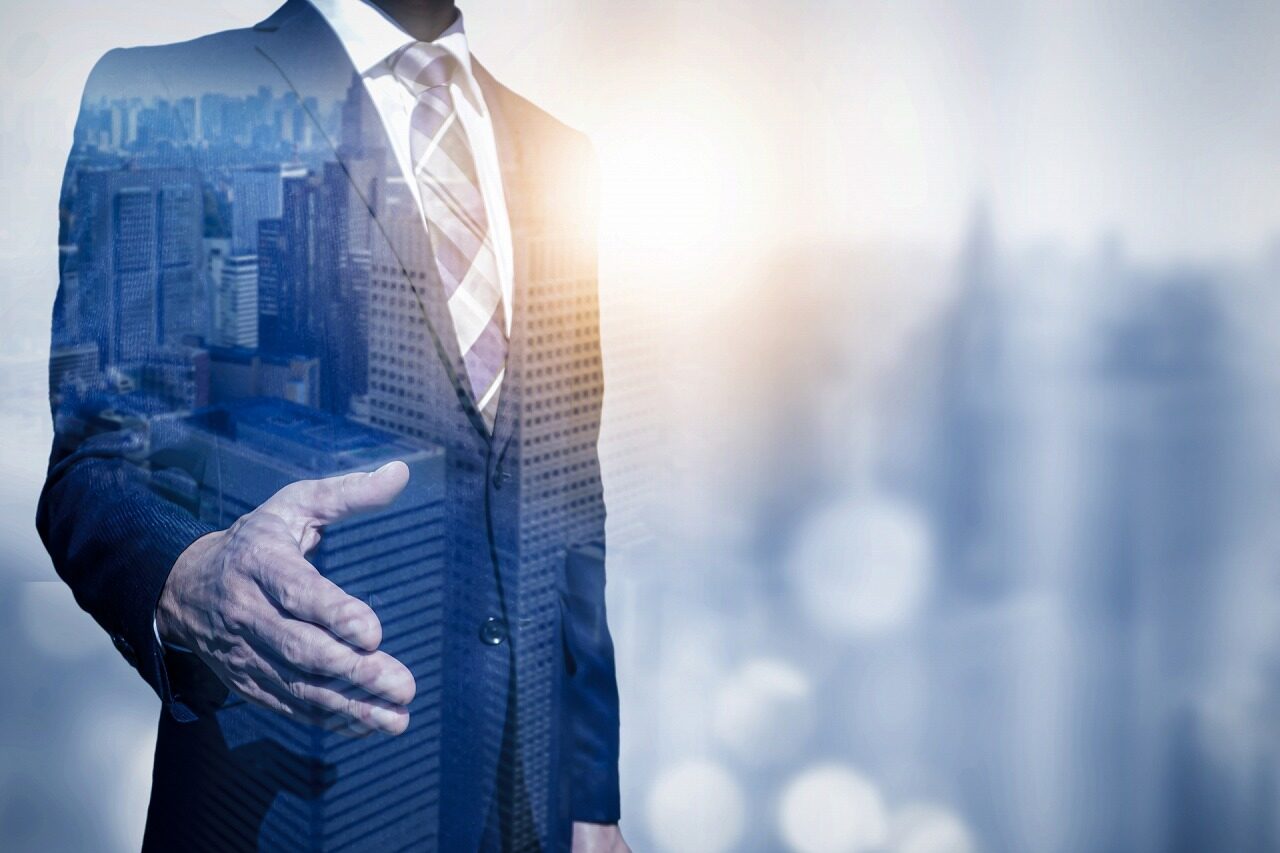
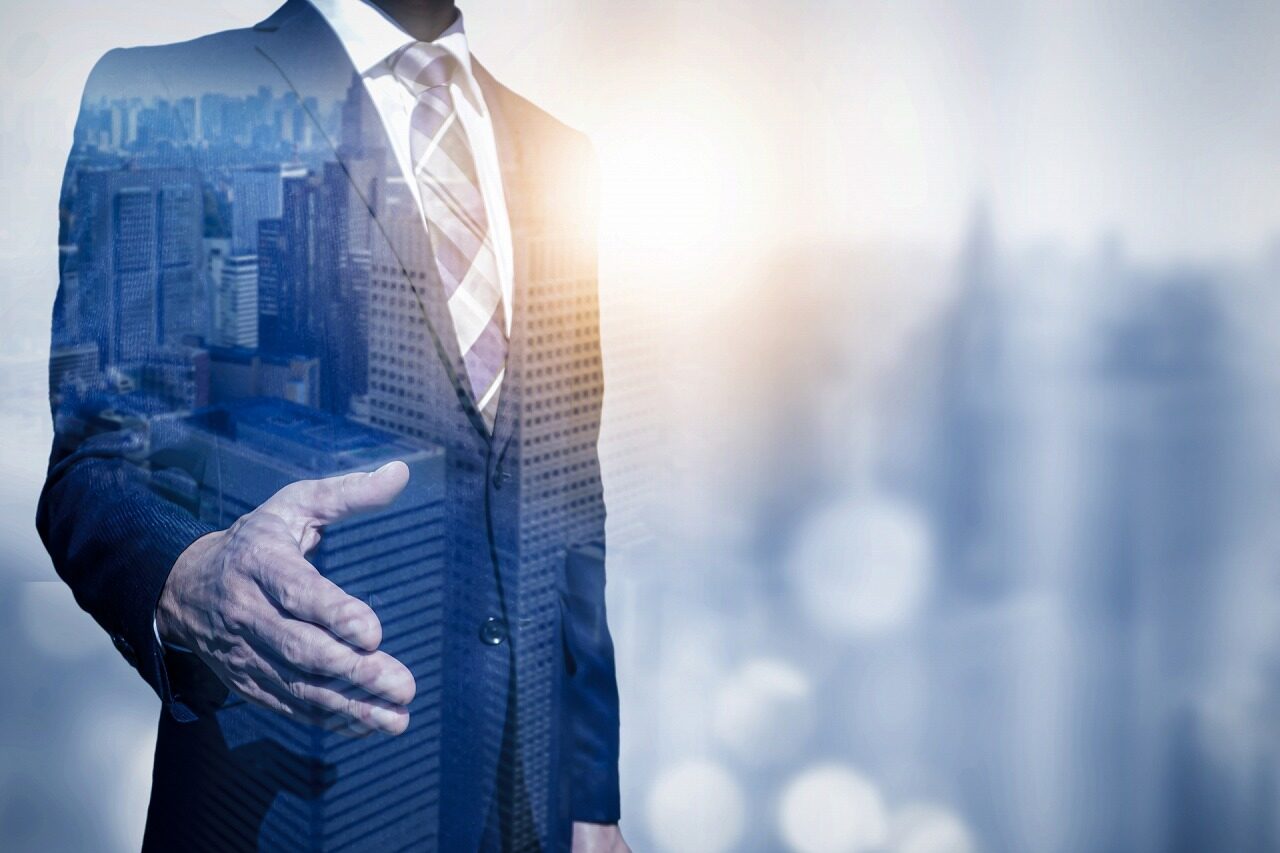
機械安全コンサルティングサービス 事業案内 | インテリスク株式会社
インテリスク株式会社は、機械安全総合コンサルティング企業として、機械や電気電子機器の海外規格・法規制への対応と国内でのリスクアセスメントサービスを提供しています…
ここまで、お読みくださいましてありがとうございました。次回はISO 12100 リスクアセスメント本編に進みます。