
ISO12100リスクアセスメントによる機械類の制限の決定や危険源の同定の具体的なやり方とコツ
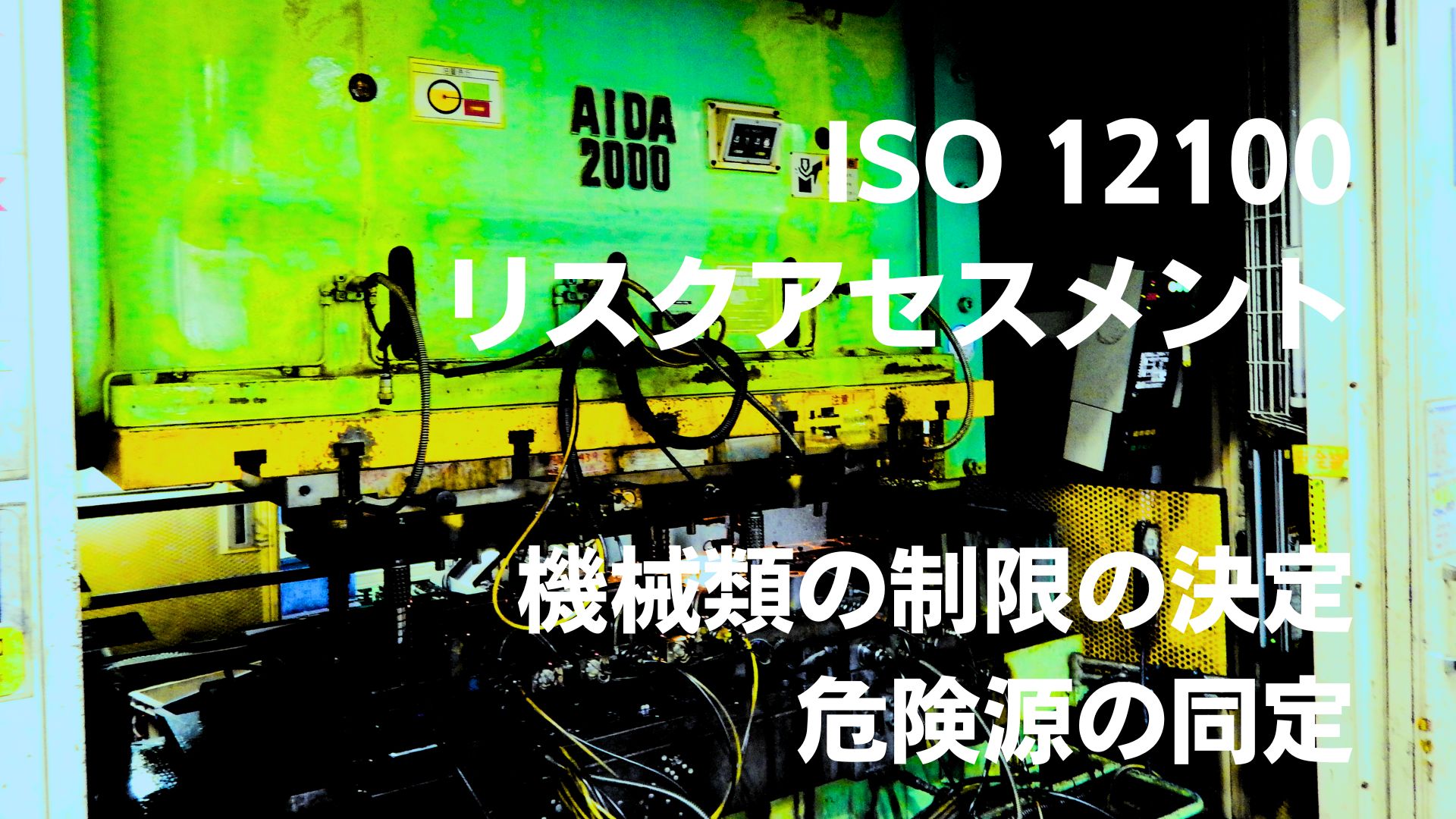
あらすじ
こんにちは!
ISO12100 リスクアセスメント機械類の制限の決定と危険源の同定について話してみたいと思います。
ISO12100 は、機械類の安全性に関する国際規格です。この規格は、機械類の設計者や製造者が、機械類に関連する危険を評価し、適切な安全対策を講じるための一般的な原則と方法論を提供しています。ISO12100 は、機械類の安全性に関する他の国際規格や技術仕様との整合性を確保するための基礎的な規格でもあります。
ISO12100 は、機械類の安全性に関するリスク評価とリスク低減のプロセスを定義しています。このプロセスは、以下の3つの段階からなります。
- 制限の決定
- 危険源の同定
- リスク評価とリスク低減
このブログでは、最初の2 つの段階について、わかり易く説明します。
機械類の制限の決定とは、機械の使用方法や条件、動作範囲や寿命などを明確にすることです。これは、リスクアセスメントを行う前提となる重要なステップです。例えば、機械はどんな人が使うのか、どんな目的で使うのか、どんな環境で使うのか、どんな材料を加工するのか、どんなメンテナンスが必要なのかなどを考えます。また、意図しない使い方や誤動作が起こる可能性も考慮します。
制限の決定とは、機械類の使用目的や使用条件を明確にすることです。制限の決定は、リスク評価とリスク低減の基準となります。制限の決定には、以下の要素が含まれます。
- 機械類の名称や型式
- 機械類の用途や機能
- 機械類が設置される場所や環境
- 機械類を操作する人員や対象物
- 機械類の使用期間や使用頻度
- 機械類に関連する指令や規格
制限の決定を行う際には、以下の点に注意する必要があります。
- 制限は、現実的で合理的であること
- 制限は、文書化されていること
- 制限は、必要に応じて見直されること
危険源の同定とは、機械に関連するすべての危険な場所や状況を見つけ出すことです。危険源とは、人に危害を与える可能性のあるものです。例えば、機械的な切断や挟み込み、電気的なショックや火災、熱的なやけどや凍傷、騒音や振動による聴覚障害やストレス、有害物質による中毒やアレルギー、人間工学的に不適切な姿勢や操作などが危険源になります。危険源は、機械のライフサイクル(機械が製造者の工場を出てから廃棄まで)のすべての段階で発生する可能性があります。
危険源の同定は、リスク評価とリスク低減の対象となります。危険源の同定には、以下の手順が含まれます。
- 機械類を各部分や各動作に分解する
- 各部分や各動作が発生させる可能性のある危険を列挙する
- 列挙した危険が制限に違反するかどうか判断する
- 制限に違反する危険を危険源として記録する
危険源の同定を行う際には、以下の点に注意する必要があります。
- 危険源は、具体的で明確であること
- 危険源は、文書化されていること
- 危険源は、必要に応じて見直されること
目次
ISO 12100 とは? ISO 12100 なぜ必要?
ISO 12100 とは? ISO 12100 なぜ必要? 復習
ISO 12100 は、機械の安全性を確保するための国際規格です。機械の設計者は、この規格に従ってリスクアセスメントとリスク低減のプロセスを実施する必要があります。リスクアセスメントとは、機械のライフサイクルのすべての段階で、危険源や危害を特定し、リスクを見積り、評価することです。リスク低減とは、リスクを許容可能なレベルまで減らすための方策を選択し、実施することです。ISO 12100 は、リスクアセスメントとリスク低減の原則や方法論を提供するとともに、基本用語や定義も規定しています。ISO 12100 は、タイプA 規格と呼ばれる基本安全規格であり、他のタイプB やタイプC の安全規格の策定にも基礎となります。ISO 12100 は、機械の安全性に関する知識や経験に基づいて作られた規格であり、機械の設計者にとって有用なガイドラインです。
ISO12100.com

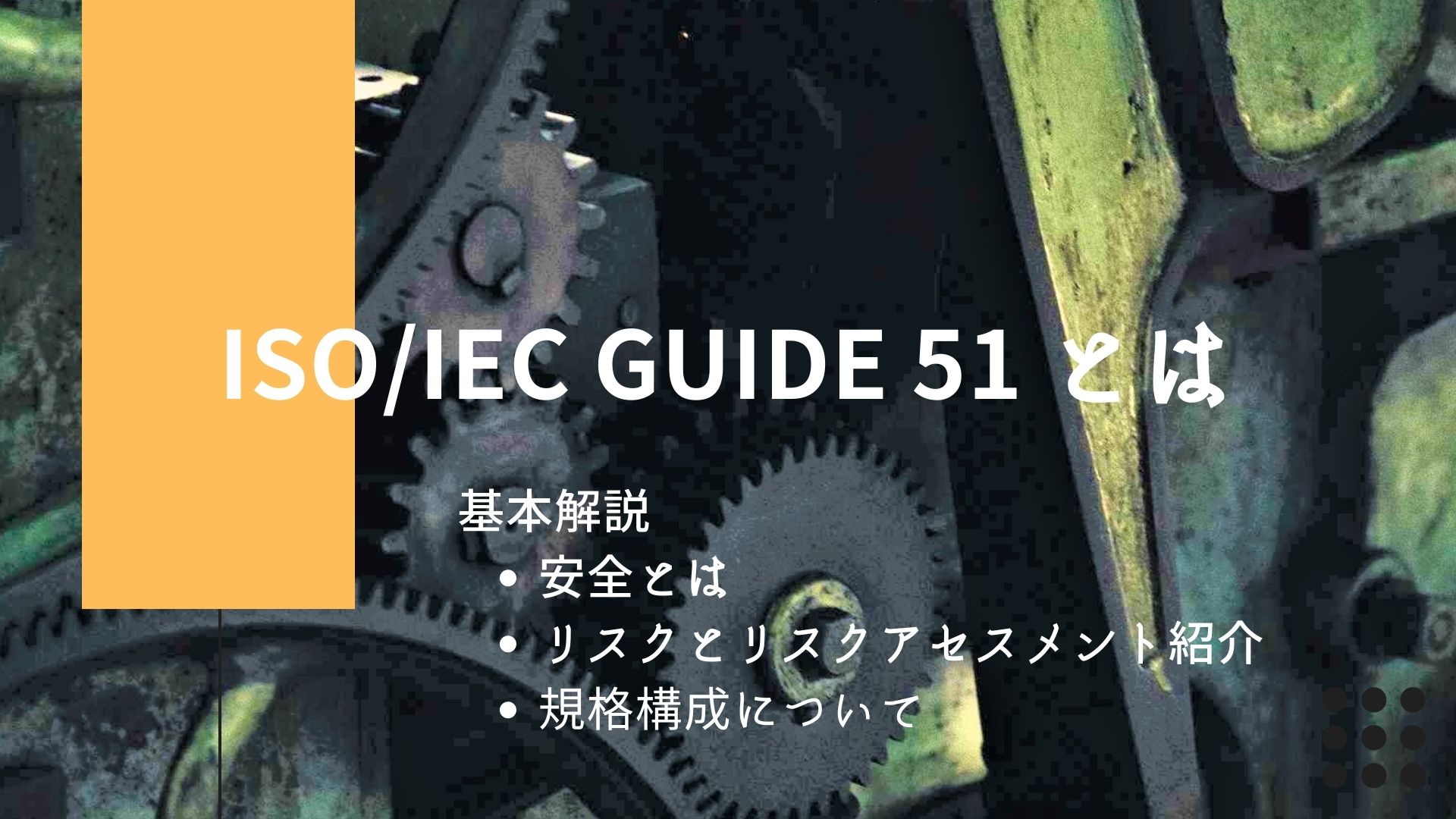
ISO/IEC GUIDE 51安全の定義「安全とは許容不可能なリスクがないこと」とリスクゼロはありえない
こんにちは! 今日はISO/IEC GUIDE 51という国際規格についてお話ししたいと思います。 ISO/IEC GUIDE 51は、製品やシステムの安全性に関する国際的なガイドラインです。こ…
ISO12100.com

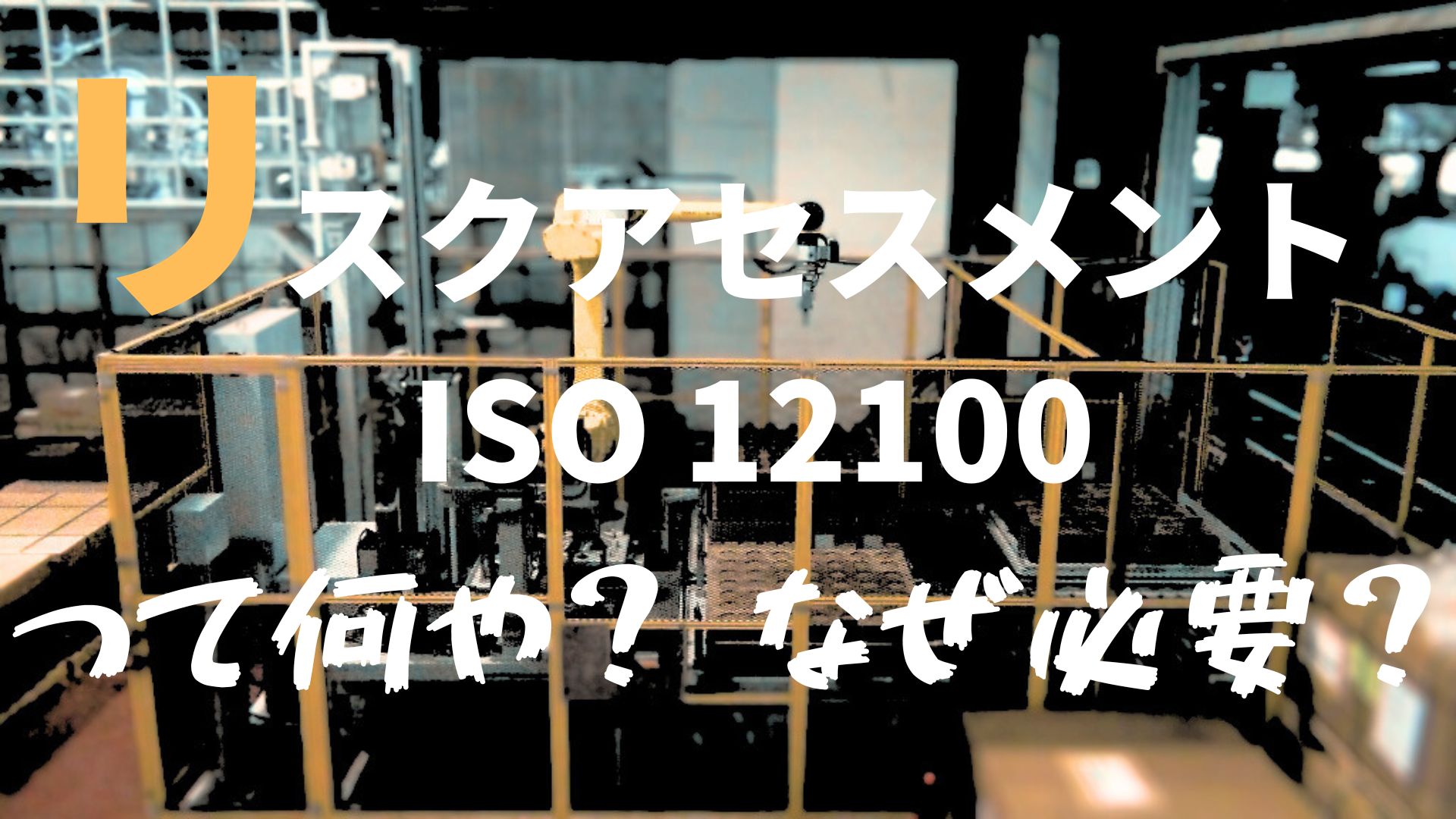
ISO12100リスクアセスメントって何?機械の安全化に必要なリスクアセスメントの理由を初心者向けに解説 | I…
こんにちは!今回は、機械の安全性に関する国際規格であるISO12100 について、リスクアセスメントの方法をわかりやすく説明してみたいと思います。リスクアセスメントとは…
リスクアセスメントの手順
リスクアセスメントとは「リスク分析及びリスク評価を含む全てのプロセス」と定義されています。具体的には以下の5つの手順で行うことができます。
STEP
機械の制限の決定
機械の制限とは、機械が設計された目的や使用条件、対象となるユーザーや作業者などを明確にすることです。機械の制限を決定することで、機械に関連する危険やリスクを特定しやすくなります。
STEP
危険源の同定
危険源とは、機械から発生する可能性のある物理的、化学的、生物的、心理的な要因のことです。危険源を同定するためには、機械のライフサイクル全体を考慮し、正常な使用状況だけでなく、異常な使用状況や故障時の状況も想定する必要があります。
STEP
リスクの見積もり
リスクの見積もりとは、危険源から発生する可能性のある事故や障害の頻度や重大度を評価することです。リスクの見積もりには、定量的な方法や定性的な方法がありますが、どちらの方法を選択するかは、利用可能な情報や資源に応じて決める必要があります。
STEP
リスクの評価
リスクの評価とは、リスクの見積もりの結果を基にして、リスクが許容範囲内かどうかを判断することです。リスクの評価には、法的な基準や社会的な基準、技術的な基準などが用いられます。リスクが許容範囲を超えている場合は、リスク低減策を講じる必要があります。
STEP
リスク低減策の実施
リスク低減策とは、リスクを許容範囲内にするために行う措置のことです。リスク低減策には、3 ステップメソッドと呼ばれる以下のような階層があります。リスク低減策を実施した後は、その効果を確認し、必要に応じて改善することが重要です。
- 本質安全設計 (機械設計上の対策(危険源の除去や隔離))
- 安全防護、付加保護方策(安全装置や保護ガードなどの技術的な対策)
- 使用上の情報(機械に警告標識、取り扱い説明書など)
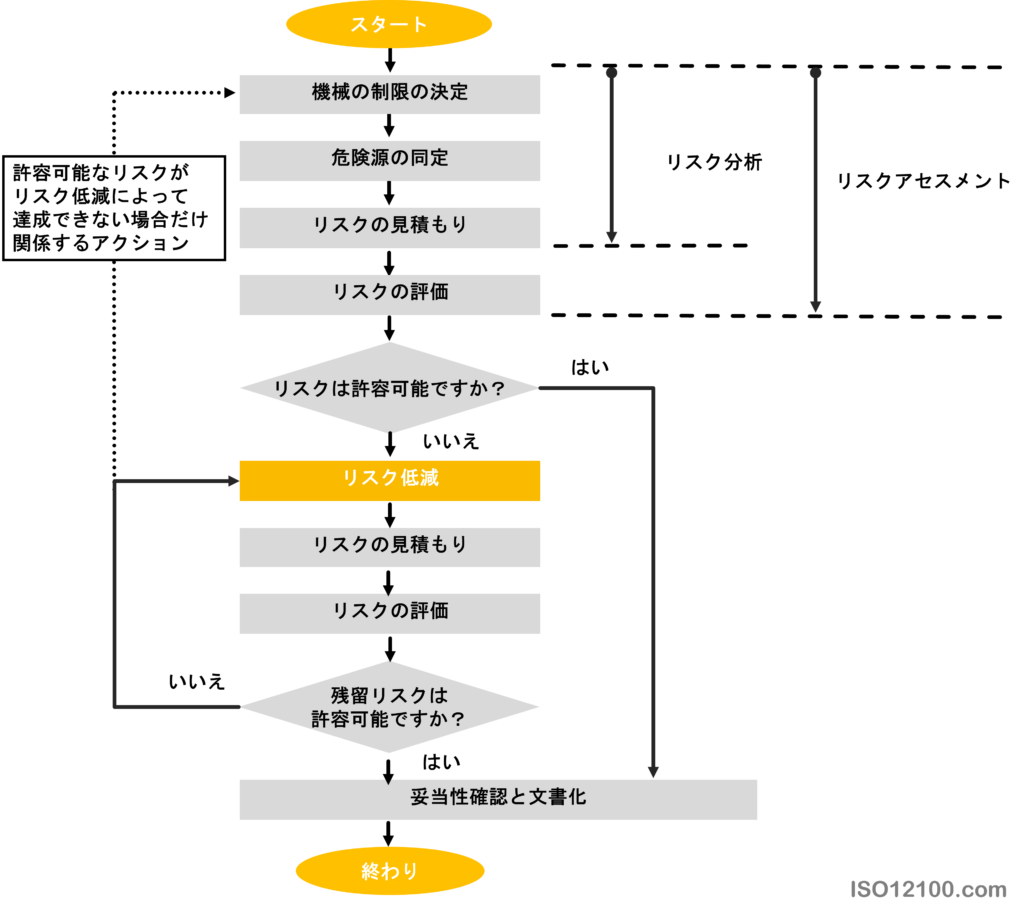
機械の制限の決定
ISO 12100 での「機械の制限の決定」は、リスクアセスメントの最初の手順であり、対象となる機械の仕様や条件を明確にすることが重要です。機械の危険な場所を見つけて安全にするためには、まず機械が何をするか、誰が使うか、どこで使うか、何を作るかなどを決めることから始めます。これは、機械の目的や特徴をはっきりさせることが大切だからです。機械の制限は、以下の4 つから構成されています。
機械の制限の種類
- 使用上の制限
- 空間上の制限
- 時間上の制限
- その他の制限
使用上の制限
使用上の制限とは、機械の設計や使用に必要な情報のことです。1. 機械が壊れたらどうするか 2. 機械を使う人の特徴 3. 機械を使う人のレベル 4. 機械が危ないときに他の人が近づく可能性。2. の情報がない場合は、製造者は一般的な情報(例えば、身長や体重など)で考えます。
- 機械が故障したときなどに必要な操作や手順
- 機械の使い手の性別や年齢、左右どちらの手で使うか、身体的な特徴
- 例えば、目や耳の状態、体型、体力など
- 機械を使う人の訓練や経験、能力のレベル
- オペレーター
- 保守や技術者
- 見習いや初心者
- 一般人
- 機械に関係する危険なものに第三者が触れる可能性
- 隣の機械を使っている人など、危険なものを知っていると思われる人
- 管理者など、危険なものは知らないが、現場の安全ルールや決められた道順は知っていると思われる人
- 訪問者や子供など、機械や現場の安全ルールについてほとんど知らないと思われる人
空間上の制限
空間上の制限とは、機械の可動範囲や作業領域に関する制限についてです。例えば、ロボットのアーム部分やクレーンの移動範囲などが該当します。また、「オペレーター」-「機械」の適切な位置関係やインターフェイスも重要です。空間上の制限は、機械の安全性や効率性に影響する要素です。空間上の制限を考慮することで、機械の設計や運用における危険やリスクを低減することができます。
空間上の制限には、以下のようなものがあります。
空間上の制限
- 機械の可動範囲
- 作業領域
- オペレーター-機械の位置関係
- オペレーター-インターフェイス
- 機械の可動範囲
機械が動くことができる範囲です。例えば、ロボットのアーム部分やクレーンの移動範囲などが該当します。可動範囲は、機械の種類や目的に応じて決められます。可動範囲を適切に設定することで、機械の性能を最大限に発揮することができます。また、可動範囲を超えないようにすることで、機械の破損や事故を防ぐことができます。
- 作業領域
機械が作業することができる領域です。例えば、工作物や材料を置く場所や加工する場所などが該当します。作業領域は、機械の可動範囲と一致する必要はありませんが、可動範囲内に収まる必要があります。作業領域を適切に設定することで、機械の作業効率や品質を向上させることができます。また、作業領域を明確にすることで、オペレーターや他の人や物への危害を減らすことができます。
- オペレーター-機械の位置関係
オペレーターが機械に対してどのような位置にいるかです。例えば、オペレーターが機械の近くにいるか遠くにいるか、前面にいるか側面にいるかなどが該当します。オペレーター-機械の位置関係は、オペレーターの安全性や操作性に影響します。オペレーター-機械の位置関係を適切に設定することで、オペレーターが機械を正確に制御しやすくなります。また、オペレーターが機械から適度な距離を保つことで、オペレーターへの危険を低減することができます。
- オペレーター-インターフェイス
オペレーターが機械とコミュニケーションするための手段です。例えば、スイッチやボタンやディスプレイなどが該当します。オペレーター-インターフェイスは、オペレーターの操作性や理解性に影響します。オペレーター-インターフェイスを適切に設計することで、オペレーターの負担を減らし、機械の性能を最大限に引き出すことができます。
時間上の制限
時間上の制限とは、機械や部品が安全に長持ちするために、使う時間や修理する時間を決めることです。
時間上の制限
- 機械や部品がどれくらい使えるか、どんな間違いが起こりやすいか
- どのくらいの間隔で点検や修理をするか
ISO 12100は、機械の安全性に関する国際規格です。この規格では、機械や部品が壊れないようにするために、時間上の制限をわかりやすく説明することが求められています。時間上の制限とは、機械や部品が安全に使用できる期間や回数のことです。時間上の制限を決める際には、以下の要素を考慮する必要があります。時間上の制限をわかりやすく説明することは、機械の安全性を高めるだけでなく、コストや効率も改善することにつながります。
- 機械や部品がどれくらい使われるか、どんな間違いが起こりやすいか
機械や部品の使用頻度や使用方法によって、摩耗や劣化の速度が変わります。例えば、高温や高圧などの過酷な環境で使用される場合や、設計された目的以外で使用される場合は、時間上の制限を短く設定する必要があります。また、人間の操作ミスや外部からの衝撃などによって、機械や部品が破損する可能性も考慮しなければなりません。
- どのくらいの間隔で点検や修理をするか
時間上の制限を決めたら、それに応じて点検や修理の計画を立てる必要があります。点検や修理は、機械や部品の状態を確認し、必要な場合は交換や調整を行うことで、安全性を維持するための重要な作業です。点検や修理のタイミングは、時間上の制限だけでなく、メーカーの推奨や法令の要件なども参考にします。
その他の制限
その他の制限とは、機械を安全に使うときに注意する他のことです。
その他の制限
- どんな材料を使えるか
- どれくらいきれいにしなければならないか
- どんな場所や気温で使えるか、日光やほこりや湿気に強いかどうか
その他の制限とは、機械を使うときに考慮しなければならない、機械の性能や特性に関する制約や条件です。その他の制限は、機械の安全性や信頼性に影響する可能性があります。その他の制限の例としては、以下のようなものがあります。その他の制限は、機械を安全かつ効果的に使用するために重要な要素です。その他の制限は、機械の設計者や製造者や販売者から提供される情報に基づいて遵守しなければなりません。また、その他の制限は、オペレーターや管理者に十分に伝えられる必要があります。
- どんな材料を使えるか
機械に適した材料の種類や品質や形状や寸法など。機械に不適切な材料を使用すると、機械の故障や破損や事故の原因となる可能性があります。
- どれくらいきれいにしなければならないか
機械の清掃や保守や点検の頻度や方法など。機械を適切に清掃や保守や点検しないと、機械の劣化や汚染や故障の原因となる可能性があります。
- どんな場所や気温で使えるか、日光やほこりや湿気に強いかどうか
機械の使用環境や条件など。例えば、温度や湿度や気圧や振動や衝撃や電磁波や日光やほこりなど。機械に適さない環境や条件で使用すると、機械の性能低下や故障や事故の原因となる可能性があります。
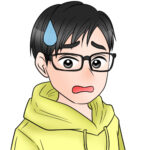
いろいろ想定しないといけないのですね😢
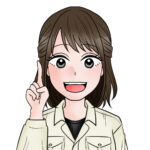
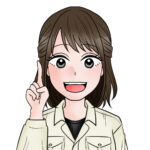
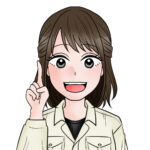
そうなんです。装置が出来上がって取返しがつかない、機械の制限の見落としには有名なものがあります。
装置が出来上がって取返しがつかないというのは、機械の設計者にとって最悪の事態です。しかし、機械の制限の見落としには有名なものがあります。それらは、装置の安全性や性能に大きな影響を与える可能性があります。以下に、そのような制限の例を挙げます。
・汚染度(沿面距離)
汚染度とは、基板の表面に付着する塵や水滴などの異物の程度を表す指標です。汚染度が高いと、基板間の絶縁距離が短くなり、漏電やショートの原因になります。汚染度は、装置の使用環境や保守方法によって変化します。したがって、装置を設計する際には、汚染度に応じた適切な沿面距離を確保する必要があります。
・過電圧カテゴリーや標高(空間距離)
過電圧カテゴリーとは、装置が接続される電源回路の種類や特性を表す指標です。過電圧カテゴリーが高いと、基板にかかる電圧が大きくなり、絶縁破壊や火花放電の危険性が高まります。過電圧カテゴリーは、装置の使用目的や場所によって異なります。したがって、装置を設計する際には、過電圧カテゴリーに応じた適切な空間距離を確保する必要があります。また、標高も空間距離に影響します。標高が高いと、空気の密度が低くなり、絶縁性能が低下します。したがって、装置を設計する際には、標高に応じた適切な空間距離を確保する必要があります。
・保護クラス (アースの方法)
保護クラスとは、電気機器の感電に対する保護の分類のことです。各保護クラスは、基礎絶縁、二重絶縁、強化絶縁、接地などの方法で、ユーザーが危険な電圧に触れることを防ぐように設計されています。例えば、クラスI の電源は、基礎絶縁と接地された導電性シャーシの二重の保護 (PELV) を備えています。クラスII の電源は、基礎絶縁と補助絶縁の二重絶縁か、強化絶縁の一重絶縁 (SELV) を備えています。クラスIII の電源は、入力電圧が安全特定低電圧 (ELV) であるため、保護は不要です。
以上のように、機械の制限の見落としは重大な問題につながる可能性があります。装置が出来上がって取返しがつかない前に、これらの制限を十分に考慮して設計することが重要です。
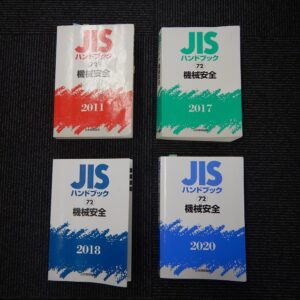
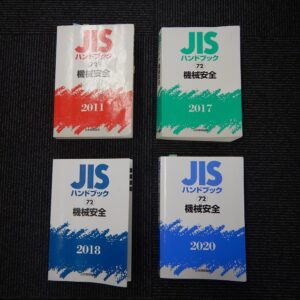
リンク
危険源の同定
危険源の同定は、この規格の中で重要なプロセスとして説明されています。危険源の同定とは、機械に関連する危険な現象や状況を特定することです。英語で「同定」とは identification (identify) と表されています。identification とは、何かを見分けることや認めることを意味します。
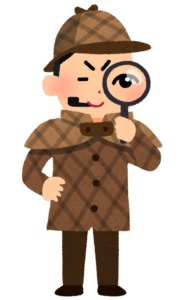
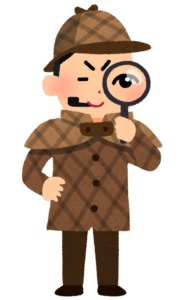
危険源 hazard
「危険源 hazard」とは、「危害を引き起こす潜在的根源」と定義されています。この定義に基づいて、機械の安全性を評価する、つまり、リスクアセスメントをする際には、まず危険源を同定し、その危険源から発生する危険状態 hazardous situation とリスク risk を分析する必要があります。
危険源は、人や物に対して傷害や損害を与える可能性があるものと理解できます。例えば、機械の動く部分や高温の表面、電気的なエネルギー、有毒な物質などが危険源となり得ます。危険源は、機械の設計や製造、運用や保守などのライフサイクルの各段階で発生したり、変化したりすることがあります。危険源は、機械の動作や環境によって変化する可能性があるため、常に監視し、適切な対策を講じることが重要です。ISO 12100 では、危険源の種類として、機械的、電気的、熱的、騒音、振動、放射、材料、人間工学などが挙げられています。
危険源の例
ISO 12100 付属書B には「危険源,危険状態及び危険事象の例」が紹介されています。この附属書は、危険源、危険状態、および、危険事象の例をリストで示しています。これらの概念を明確にすることで、危険源を同定し、リスクアセスメントをする人を支援しています。このリストが全てでもありませんし、優先順位もありません。設計者は、機械にある他の危険源、危険状態、または、危険事象も見つけて文書化する必要があります。
1. 機械的危険源


2. 電気的危険源


3. 熱的危険源
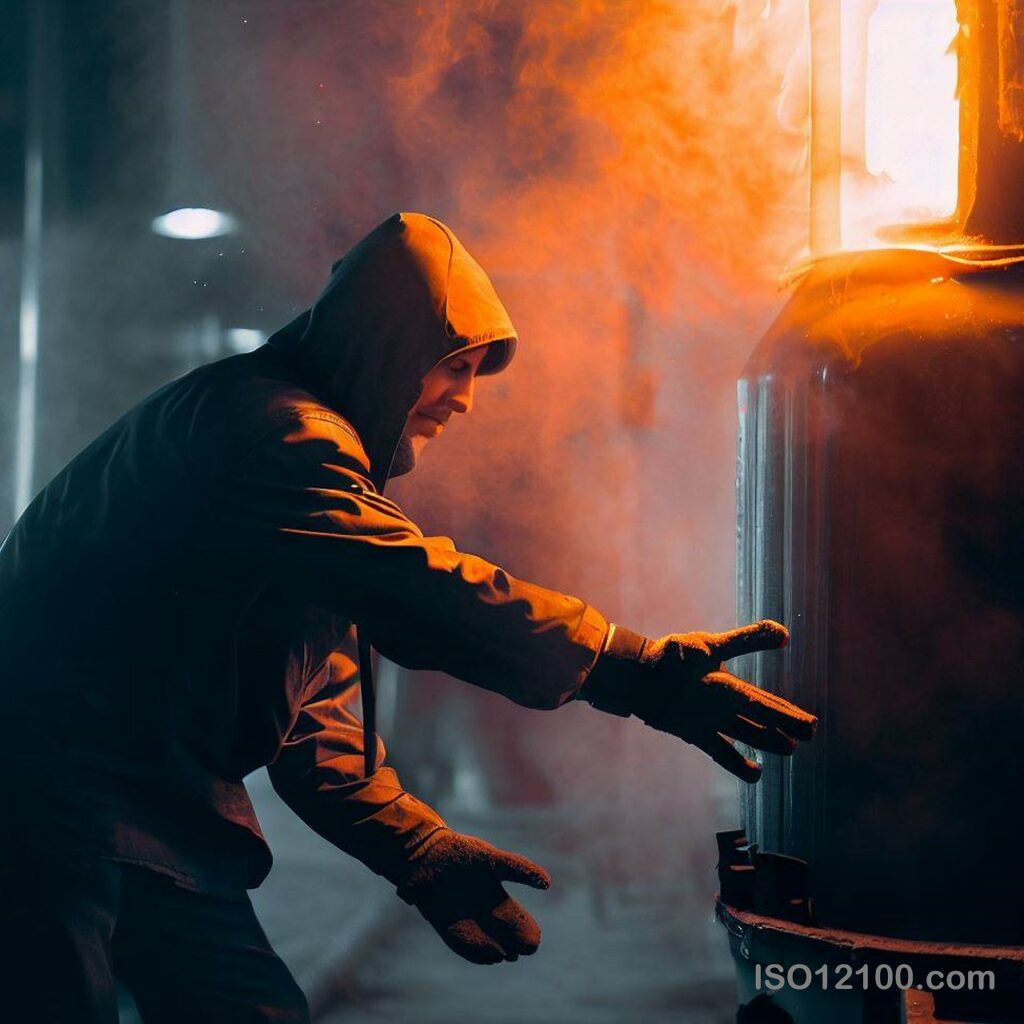
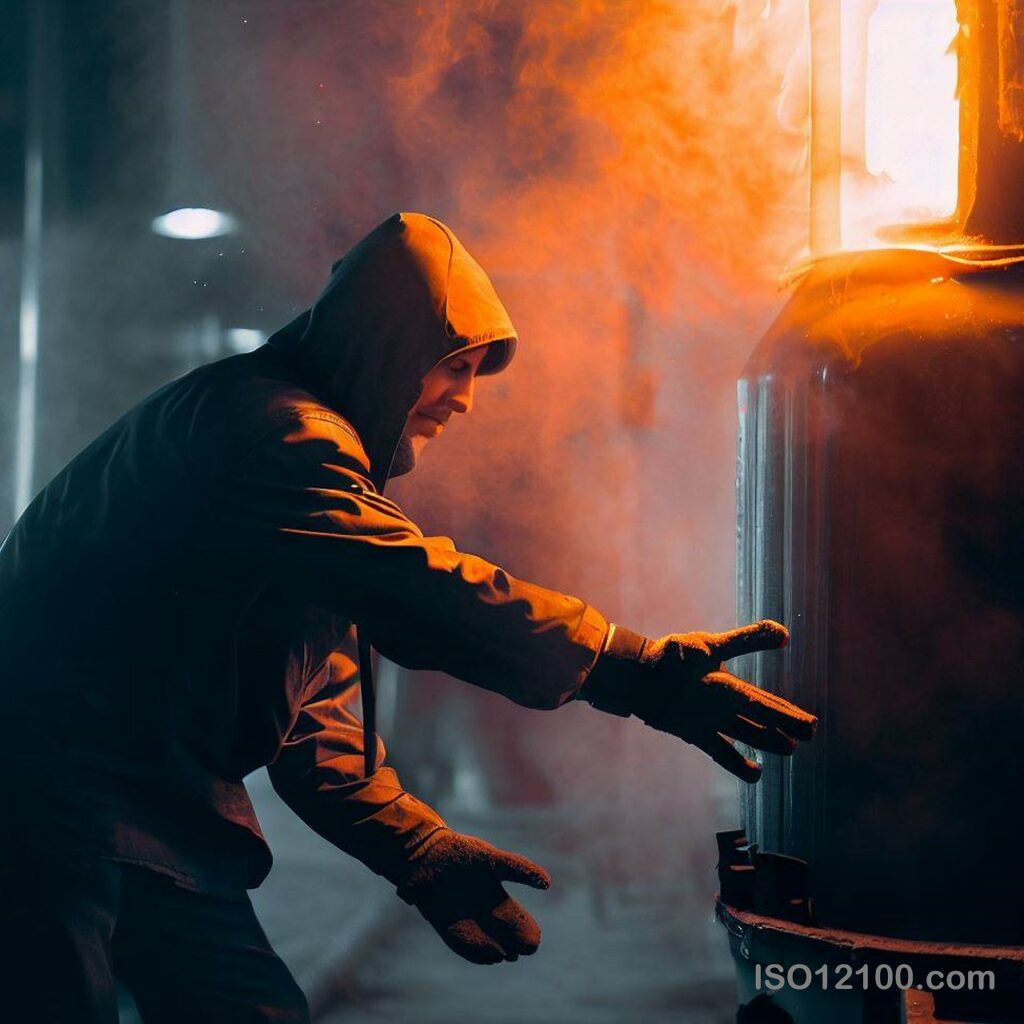
4. 騒音による危険源
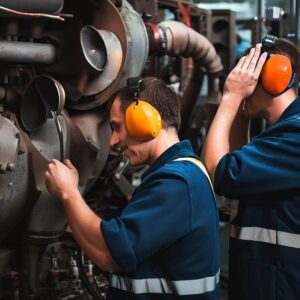
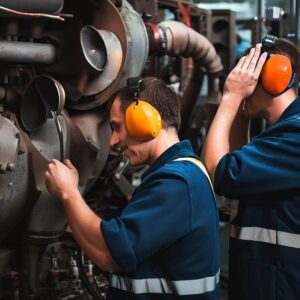
1 機械的危険源 | 危険源の例 原因 | No. | 結果 |
---|---|---|---|
A | 加速度、減速度 | 1 | 轢かれる |
B | 角張った部分 | 2 | 投げ出される |
C | 固定部分への可動要素の接近 | 3 | 押しつぶし |
D | 切断部分 | 4 | 切傷又は切断 |
E | 弾性要素 | 5 | 引込み又は捕捉 |
F | 落下物 | 6 | 巻き込み |
G | 重力 | 7 | こすれ又はすりむき |
H | 床面からの高さ | 8 | 衝撃 |
I | 高圧 | 9 | 噴出による人体への注入 |
J | 不安定 | 10 | せん断 |
K | 運動エネルギ | 11 | 滑り、つまずき及び墜落 |
L | 機械の可動性 | 12 | 突き刺し又は突き通し |
M | 可動要素 | 13 | 窒息 |
N | 回転要素 | – | – |
O | 粗い、滑りやすい表面 | – | – |
P | 鋭利な端部 | – | – |
Q | 蓄積エネルギ | – | – |
R | 真空 | – | – |
5. 振動による危険源
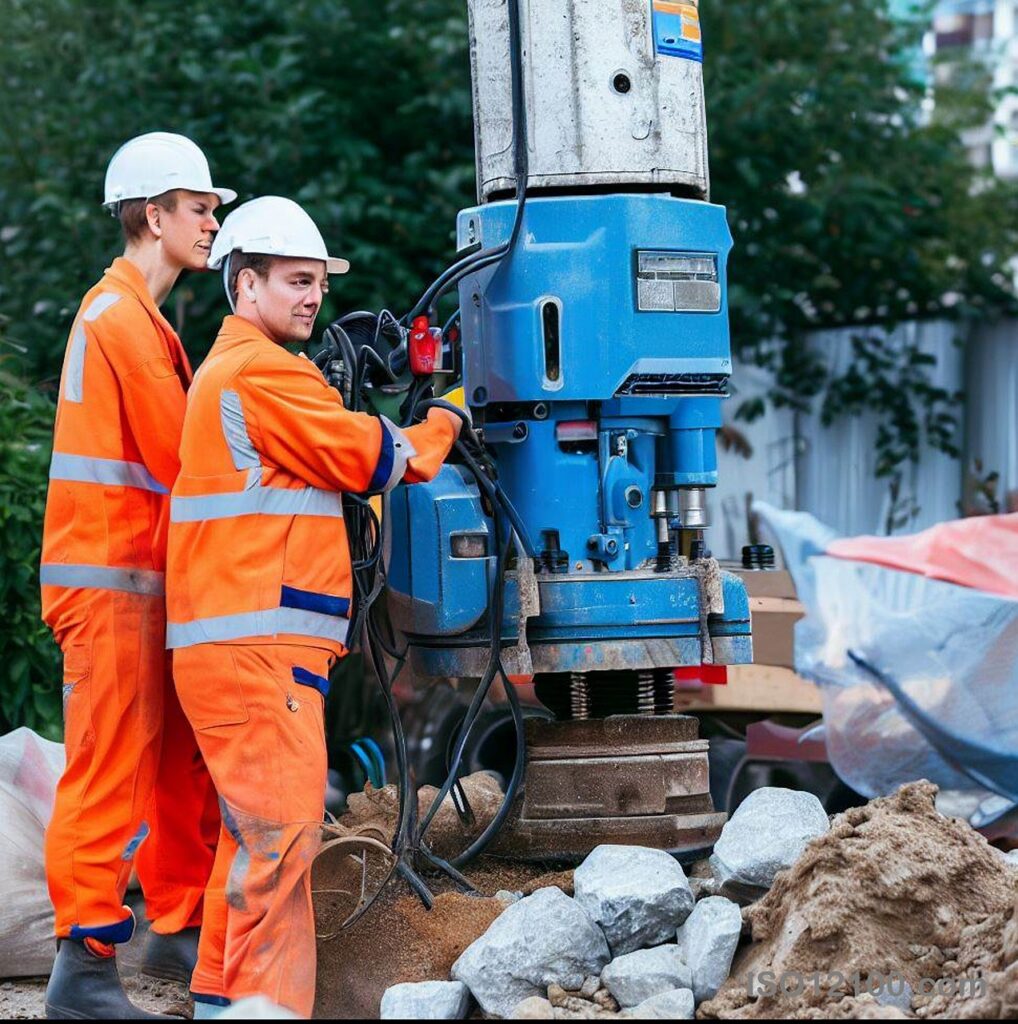
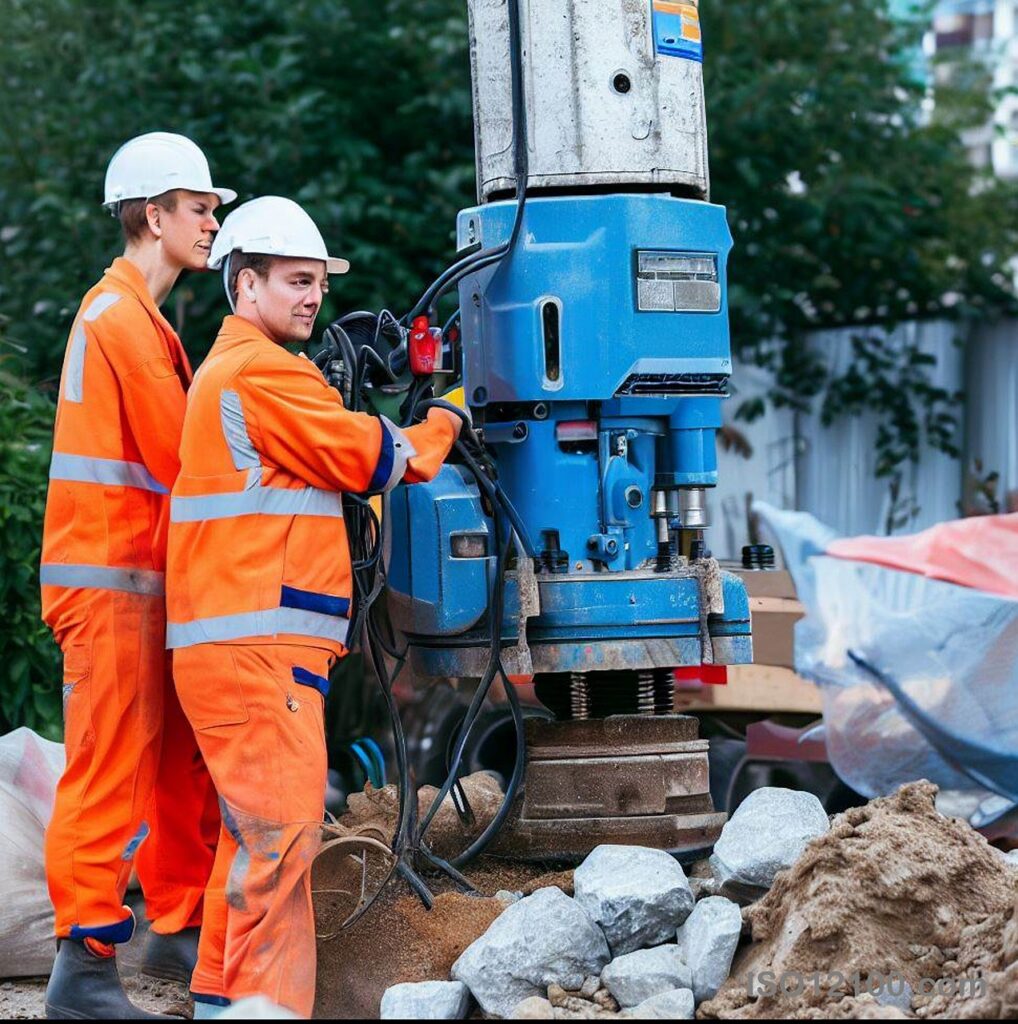
6. 放射による危険源
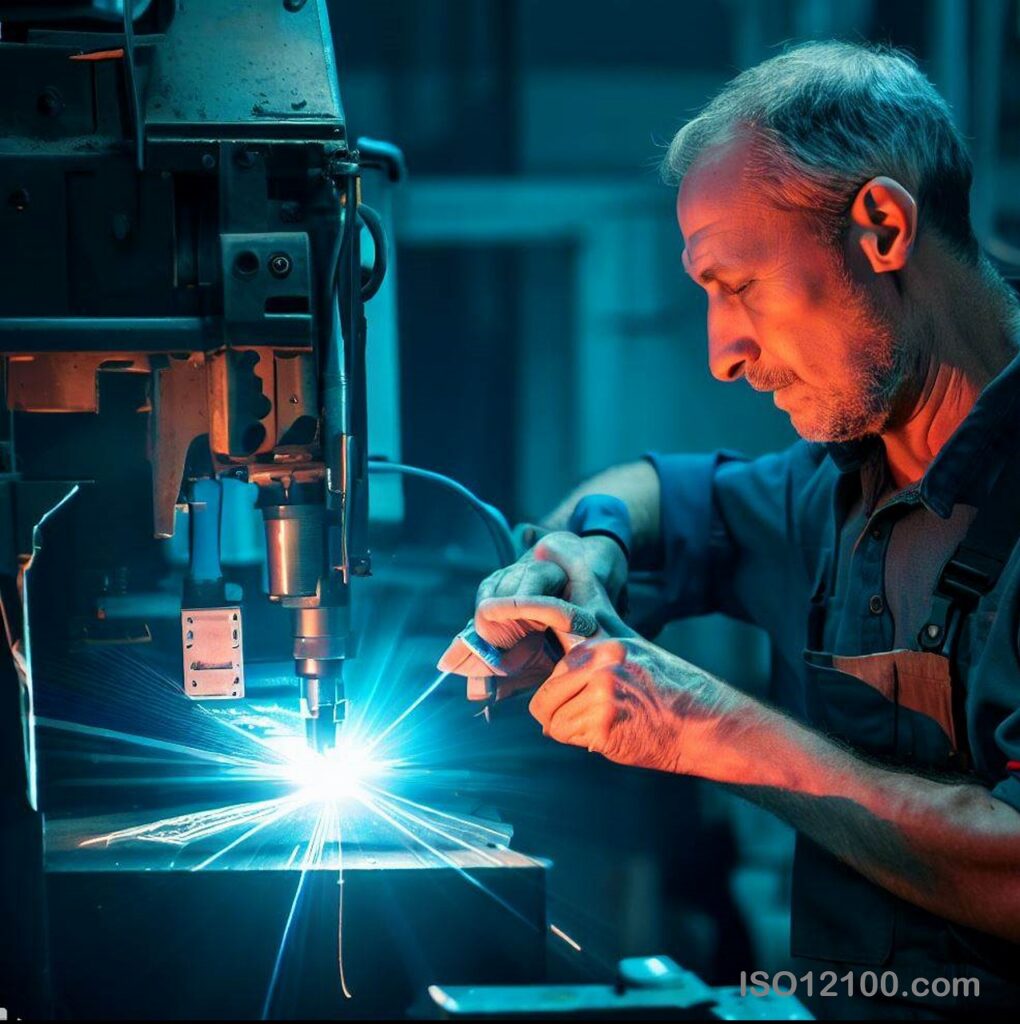
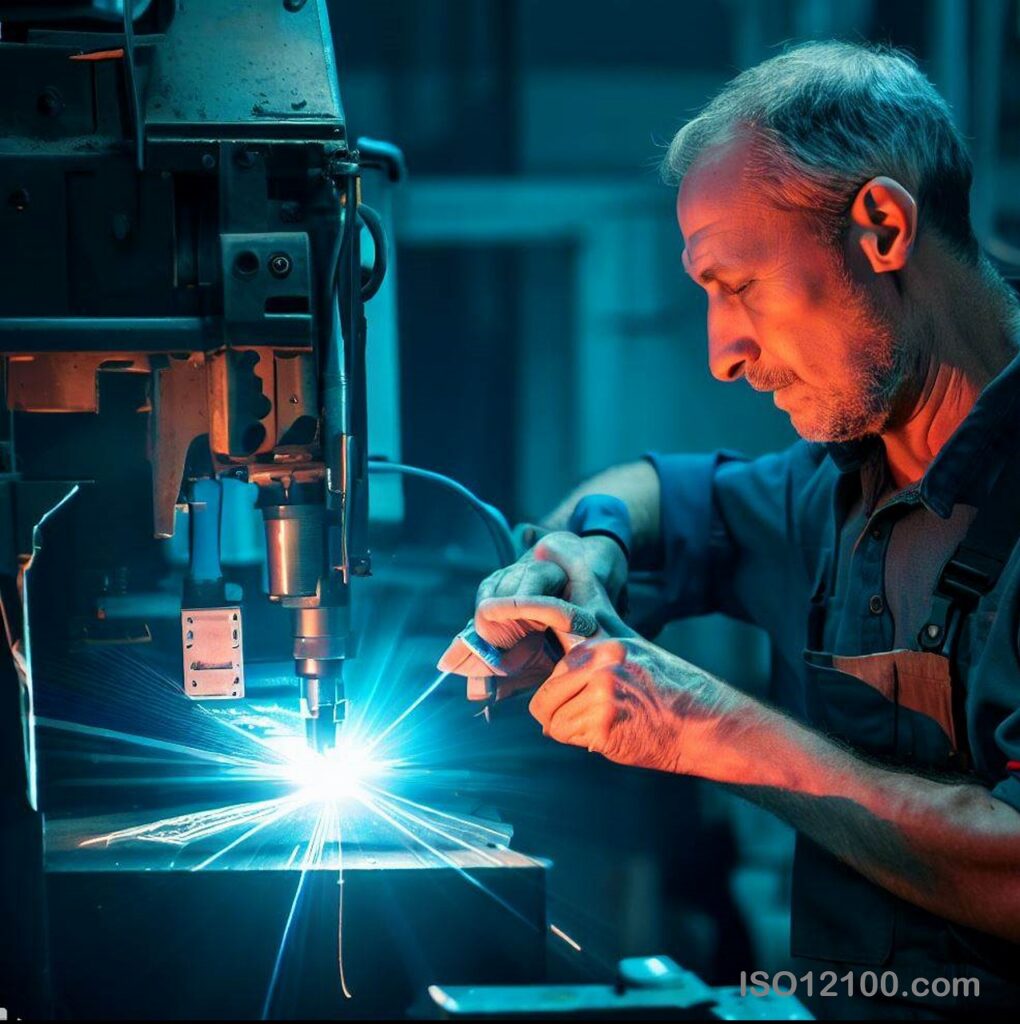
7. 材料・物質による危険源
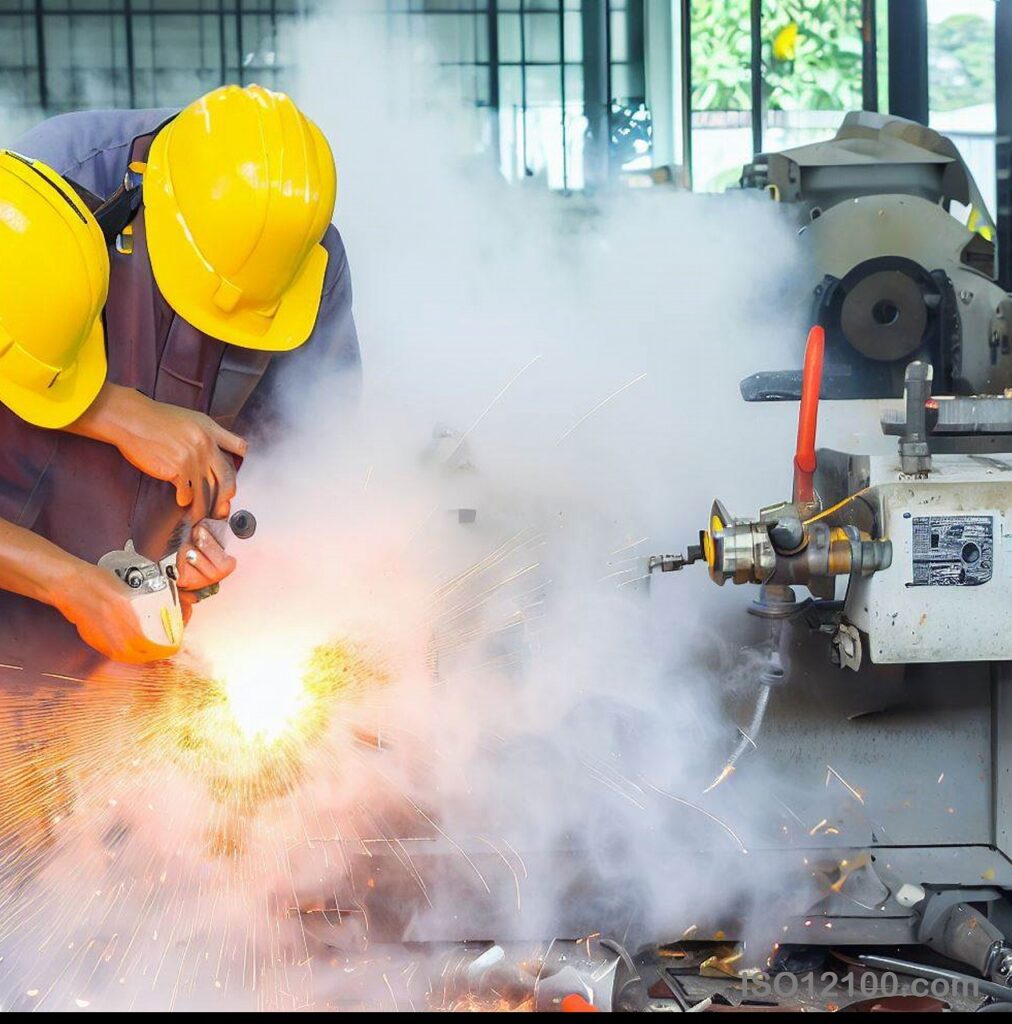
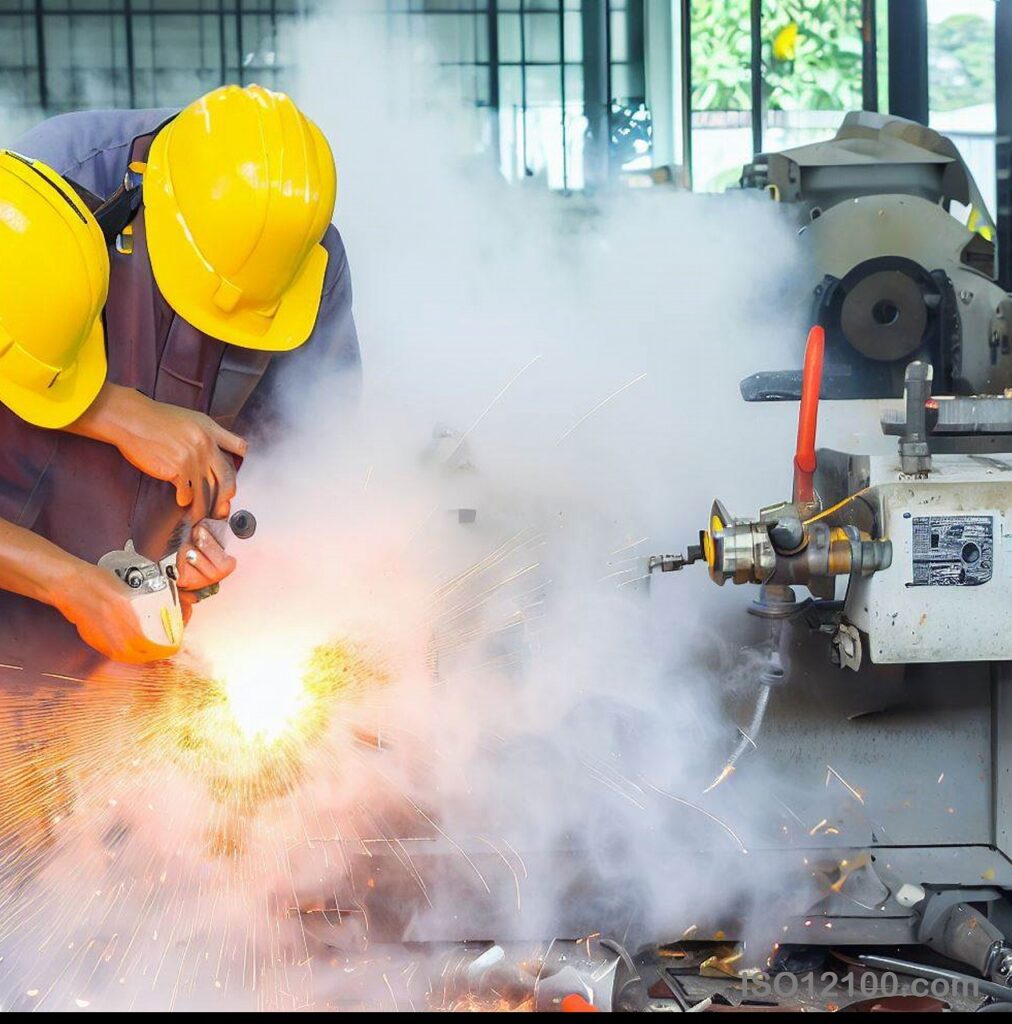
8. 人間工学原則の無視
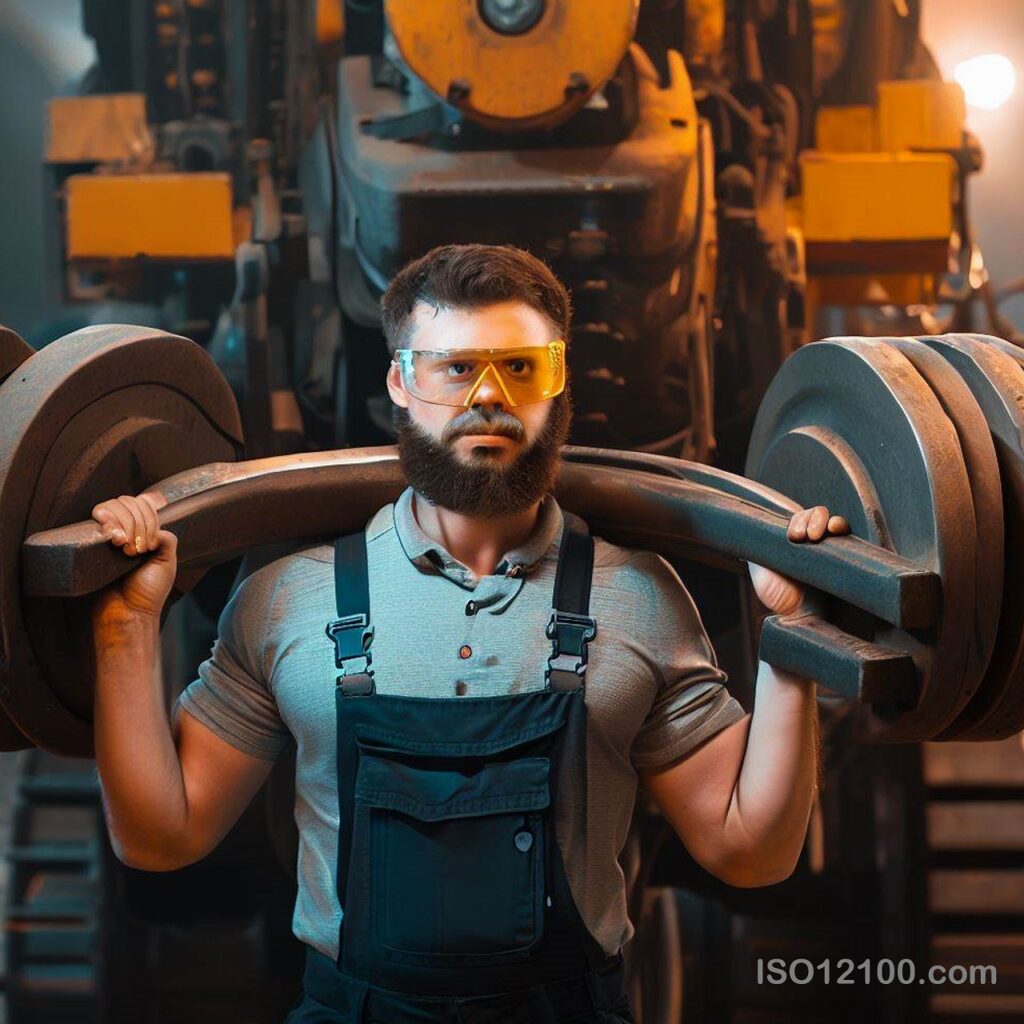
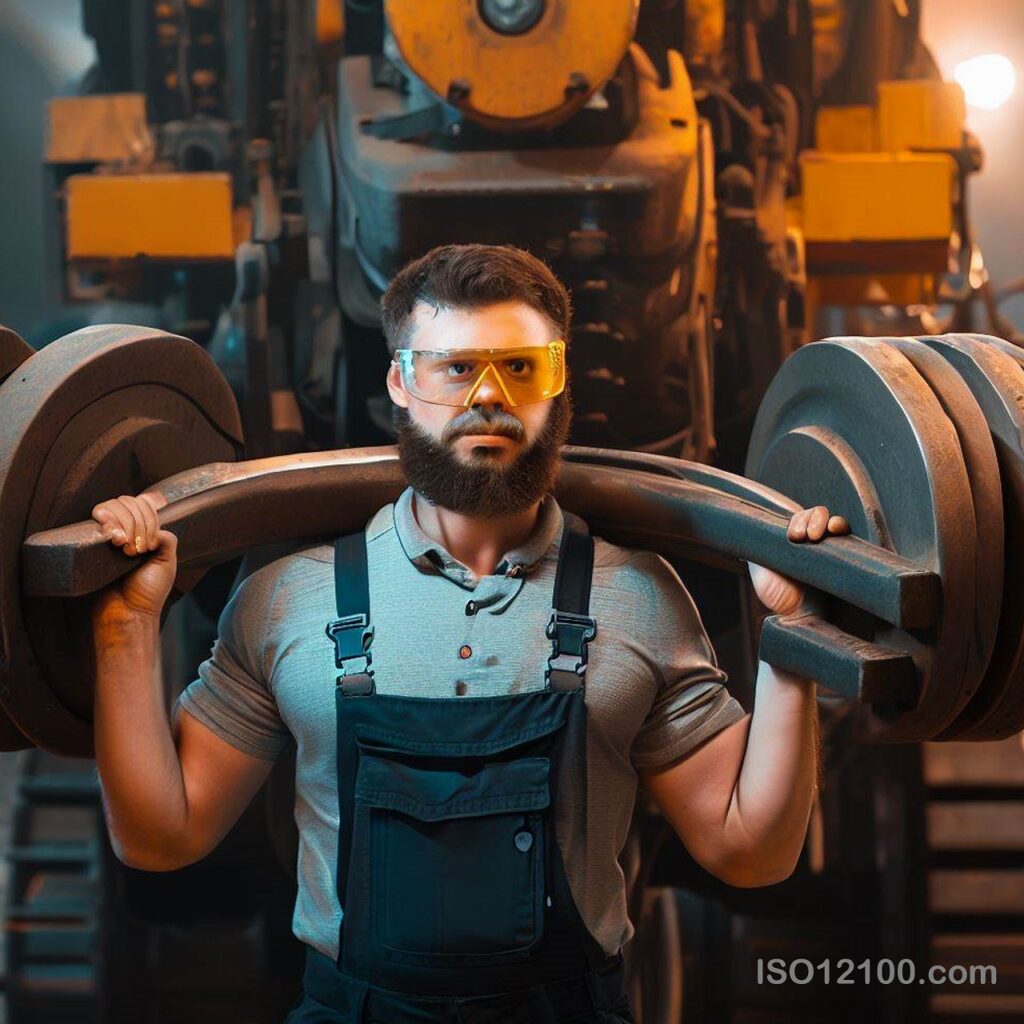
5 振動による危険 | 危険源の例 原因 | No. | 結果 |
---|---|---|---|
A | キャビテーション | 1 | 不快感 |
B | 可動部分の調整ミス | 2 | 腰部の障害 |
C | 移動式装置 | 3 | 神経疾患 |
D | 表面のこすれ・ひっかき | 4 | 骨関節障害 |
E | バランスの悪い回転部品 | 5 | 脊柱・脊推骨の外傷 |
F | 振動する装置 | 6 | 血管障害 |
G | 部品の劣化・摩耗 | – | – |
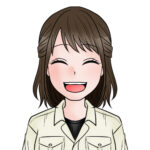
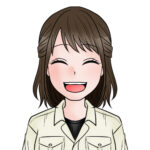
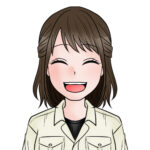
リスクアセスメントシートに記入するときは記号で表してみるのもいいかもしれませんね。例
1N6 機械的危険源 回転要素 巻き込み
2F6 電気的危険源 過負荷 火災
同定
危険源の同定では、機械の設計、製造、運転、保守、廃棄などのライフサイクルの各段階で、どのような危険源が存在するかを洗い出します。例えば、機械の動く部分に挟まれたり、切断されたりする危険源や、電気的なショックや火災を引き起こす危険源などがあります。危険源の同定には,機械の仕様や構造、使用環境や操作方法などを考慮し、専門家や利用者の意見も参考にします。
危険源の同定は、リスクアセスメントの基礎となります。リスクアセスメントでは、危険源が発生する確率とその影響度を評価し、リスクのレベルを判断します。リスクが高い場合は、リスク低減策を講じます。ISO 12100 危険源の同定は、機械の安全性を向上させるために必要不可欠な作業です。
設計者は、機械が危なくないようにするために、次のことを考えなければいけません。機械が作られてから廃棄されるまでの間に、人がどうやって関わるか。機械がどんなトラブルを起こすか。オペレーターが間違えてやってしまうことや、普通に考えられること。
設計者が危険源を同定のために考慮すべきポイント
- 機械の全ライフサイクルにおける人の介入
- 機械で起こる可能性のある状況
- オペレーターの意図しない挙動又は合理的に予見可能な機械の誤使用
機械の全ライフサイクルにおける人の介入
機械の全ライフサイクルにおける人の介入の同定は、機械のライフサイクルの全ての局面とタスクカテゴリを考慮することが望ましいです。タスクに関連する危険源、危険状態または危険事象だけでなく、タスクに関連しない危険源、危険状態、または危険事象も同定する必要があります。
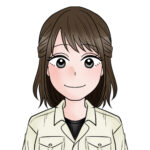
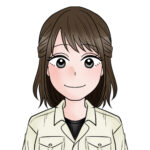
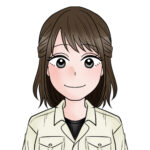
つまり、タスクごとに同定が必要ってことです
機械のライフサイクルとは、機械の設計、製造、運用、保守、廃棄などの一連のプロセスを指します。機械のライフサイクルにおいては、人の介入が必要なタスクが多く存在します。人の介入は、機械の性能を向上させたり、安全性を確保したり、故障や事故を防止したりするために重要です。しかし、人の介入には、人が危険にさらされる可能性もあります。したがって、人の介入に関するタスクを同定し、それらに伴う危険を評価し適切な対策を講じることが必要です。
タスクの同定は、上に掲げた機械のライフサイクルの全ての局面に関連する全てのタスクを考慮するのが望ましいです。タスクの同定は、次のタスクカテゴリを考慮するのが望ましいですが、これらに限定されません。
- 設定(段取りなど)
- 試験
- ティーチング、プログラミング
- 工具、工程の切替え
- 起動
- 全ての運転モード
- 機械への材料供給
- 機械からの製品の取出し
- 正常停止
- 非常事態の場合の機械の停止
- 機械異常からの復帰
- 計画外停止後の再起動
- 不具合(障害)の発見、トラブルシューティング(オペレーターの介入)
- 清掃・維持
- 予防保全
- 事後保全
これらのタスクに関連する全ての合理的に予見可能な危険源、危険状態または危険事象を同定しなければなりません。例えば、設定や試験中には、感電や火傷、挟まれや切断などの危険があります。ティーチングやプログラミング中には、誤動作や暴走などの危険があります。工具や工程の切替え中には,落下や飛散などの危険があります。
これら以外にも、各タスクに応じた危険を考える必要があります。例えば、地震、雷、過度の雪の負荷、騒音、機械の破損、油圧ホースの破裂などが挙げられる。これらの危険因子は、人の介入によって引き起こされるかもしれないし、人の介入によって回避されるかもしれません。
機械で起こる可能性のある状況
設計者は、機械で起こる可能性のある状況を考慮して危険源を同定しなければなりません。これらは、次のように分類されます。危険源とは、機械が意図された機能を果たさないことによって発生する可能性のある危険な状況や事象のことです。設計者は、危険源を同定するために、機械がどのように使用されるか、またどのように使用されないかを考慮し、機械が意図された機能を果たさない理由も考慮しなければなりません。
- 機械は、意図された機能を果たす(機械は正常に作動する)
この場合、設計者は、機械の使用者や周囲の人々が危険源に暴露される可能性がある危険状態や危険事象を特定しなければなりません。例えば、回転部分や高温部分、放出物や騒音などが危険源となり得ます。また、意図する使用や合理的に予見可能な誤使用も考慮に入れる必要があります。
- 機械は、次を含む多様な理由で意図された機能を果たさない(すなわち、機能不良である。)
- 加工材料、ワークピースの特性、寸法の変化
- 構成部品、機能の一つ(または複数)の故障
- 外乱(例えば、衝撃、振動、電磁妨害)
- 設計誤り、設計不具合(例えば、ソフトウェアのエラー)
- 動力供給異常
- 周囲の状態(例えば、損傷した床の表面)
オペレーターの意図しない挙動又は合理的に予見可能な機械の誤使用
設計者は機械の使用に関連する危険源を同定するために、オペレーターの意図しない挙動や合理的に予見可能な機械の誤使用を考慮しなければなりません。これらの挙動や誤使用はオペレーターや他の人の安全に影響を及ぼす可能性があります。例えば、以下のような場合があります。
- オペレーターによる機械の制御不能(特に、手持ち機械、移動機械)
この場合、オペレーターは、機械の動きや方向を予測できないか、制御できない状況に陥る可能性があります。例えば、手持ち機械がオペレーターの手から滑り落ちたりすることが考えられます。このような状況では,オペレーター自身や周囲の人や物に危害を及ぼす恐れがあります。
- 機械を使用中に機能不良、事故、故障が生じたときの人の反射的な挙動
この場合、オペレーターは機械の正常な動作とは異なる状況に直面し本能的に反応する可能性があります。例えば、機械が突然停止したり、異音や異臭を発したり、火花や煙を出したりすることが考えられます。このような状況では、オペレーターはパニックに陥ったり、過剰に反応したり、不適切な行動をとったりする恐れがあります。非常停止装置を押さずに手で機械を止めようとしたり、保護装置を外して原因を調べようとしたりすることが考えられます。
- 集中力の欠如、不注意から生じる挙動
この場合、オペレーターは作業中に気を散らしたり、注意力が低下したりする可能性があります。例えば、疲労やストレス、退屈や、単調さ、騒音、温度などの環境要因が影響することが考えられます。このような状況では、オペレーターは操作ミスや判断ミスをしたり、安全上重要な情報や指示を見落としたりする恐れがあります。
- 近道行為をとった結果として生じる挙動
この場合、オペレーターは作業を効率的かつ容易に行うために、安全上望ましくない方法や手順を選択する可能性があります。例えば、保護装置を無効化したり、回避や無効化したりすることが考えられます。このような状況では、オペレーターは危険源に直接さらされるリスクを高めることになります。
危険源の同定 練習
ベルトと滑車が見える機械があります。オペレーターはいつでもこの機械に近づけます。この機械にはどんな危険があるでしょうか。


この機械には「回転するベルトや滑車に手や髪の毛などが巻き込まれる危険」があります。これは「機械的危険源」の一種です。この時、危険源は ISO 12100 付属書B の表より「1. 機械的危険源」「N 回転要素」「6 巻き込み」と同定されます。「1N6」という記号で表されます
この危険源によって発生する可能性のある事故は、オペレーターがベルトや滑車に手や服などを巻き込まれて引きずり込まれたり、切断されたりすることです。これらの事故は重大な人身事故につながる可能性が高く、リスク低減策が必要です。
リスク低減策としては、以下のようなものが考えられます。
- ベルトや滑車を完全に覆う固定式ガードを設置する。
- ガードにはロック式保護インターロックなどの安全装置を付けて、機械が停止している時にしか開けられないようにする。
- オペレーターにはベルトや滑車に近づかないように注意喚起する。
- オペレーターには手袋や長袖などの巻き込みを防ぐ服装を着用させる。
- オペレーターには非常停止ボタンなどの非常対応手段を教育する。
以上のように、危険源の同定と予防策の提案は、機械の安全性を向上させるために重要な作業です。ISO 12100 付属書B の表は、危険源の同定に役立つ参考資料ですが、それだけでは十分ではありません。実際の機械の使用状況やオペレーターの行動を考慮して、適切な予防策を選択する必要があります。
ここまでお読みくださりありがとうございます。次回は 「ISO 12100 リスクの見積もり」へ進みます。